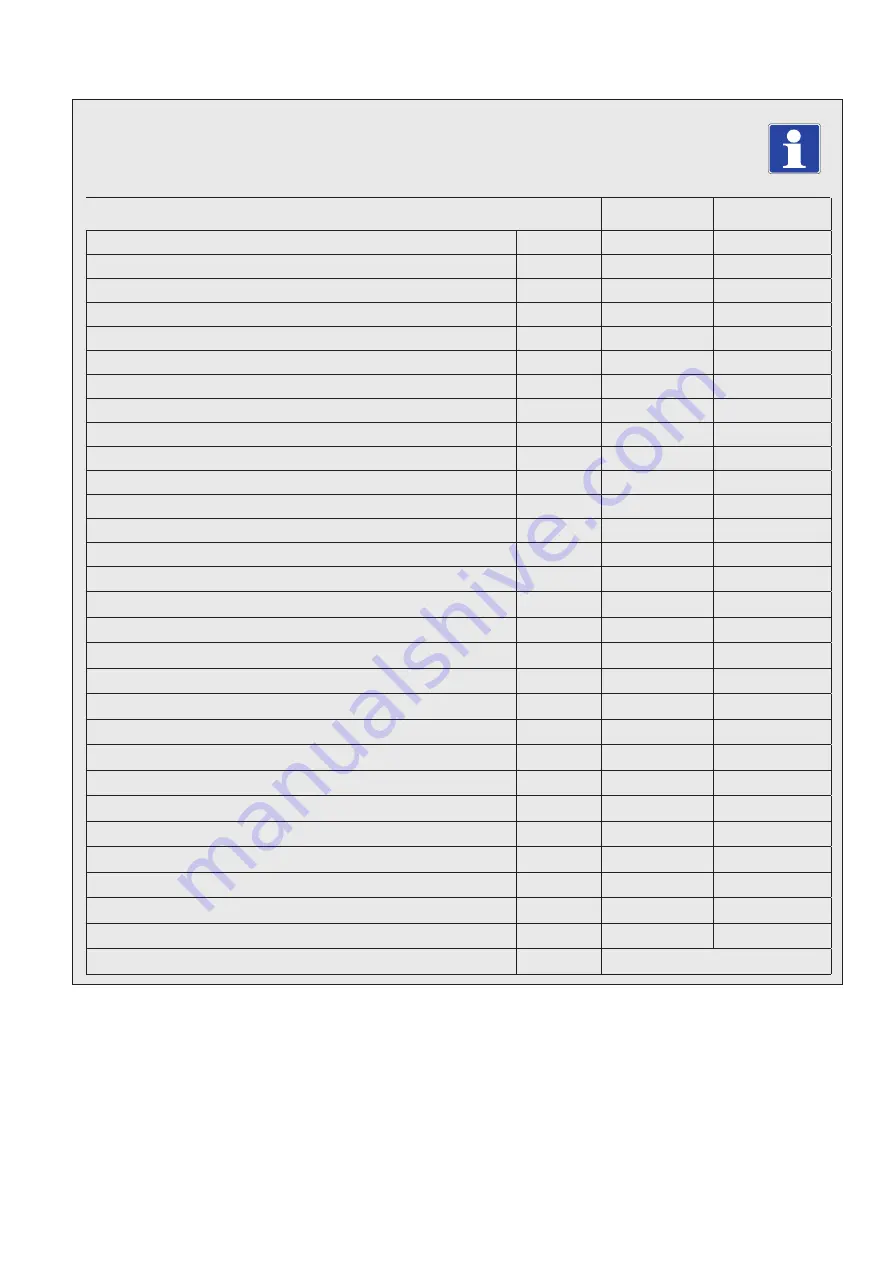
Alpha E-Tec Hybrid - Technical Data
Gas flow rates refer to the NHV at the temperature of 15° C and pressure of 1013 mbar.
Flue temperature values refer to an air inlet temperature of 15°C and flow/return temperature = 80/60°C.
Methane (G20)
LPG (G31)
Combustion efficiency 100% Pn (80/60°C)
%
97.8
97.8
Combustion efficiency P min (80/60°C)
%
97.8
97.8
Effective efficiency at 100% Pn (80/60°C)
%
97.8
97.8
Effective efficiency P min (80/60°C)
%
95.5
95.5
Effective efficiency at 100% Pn (50/30°C)
%
106.1
106.1
Effective efficiency P min (50/30°C)
%
106.1
106.1
Effective efficiency at 100% Pn (40/30°C)
%
108.2
108.2
Effective efficiency P min (40/30°C)
%
108.3
108.3
Chimney losses with burner on (100% Pn) (80/60°C)
%
1.7
1.7
Chimney losses with burner on (P min) (80/60°C)
%
2.2
2.2
Chimney losses with burner off
%
0.02
0.02
Casing losses with burner on (100% Pn) (80/60°C)
%
0.2
0.2
Casing losses with burner on (Pmin) (80/60°C)
%
2.3
2.3
Casing losses with burner off
%
0.34
0.34
Flue gas temperature Maximum Heat Input
°C
70
70
Flue gas temperature Minimum Heat Input
°C
64
63
Flue flow rate at Central Heating Maximum Heat Input
kg/h
38
37
Flue flow rate at Maximum Domestic Hot Water Heat Input
kg/h
44
43
Flue flow rate at Minimum Heat Input
kg/h
8
7
CO
2
at the Maximum Central Heating Heat Input
%
9.70
11.40
CO
2
at Maximum Domestic Hot Water Heat Input
%
9.70
11.40
CO
2
at Minimum Heat Input
%
8.80
10.60
CO at Maximum Heat Input
mg/kWh
321
316
CO at Minimum Heat Input
mg/kWh
5
5
NO
x
at the Maximum Heat Input
mg/kWh
59
85
NO
x
at Minimum Heat Input
mg/kWh
34
55
Weighted CO
mg/kWh
20
-
Weighted NO
x
mg/kWh
35
-
NO
x
class
-
6
6
Intake/exhaust available head (min-max flow rate)
Pa
2 - 240
3.2 TECHNICAL PERFORMANCE DATA BOILER COMBUSTION FEATURES
5