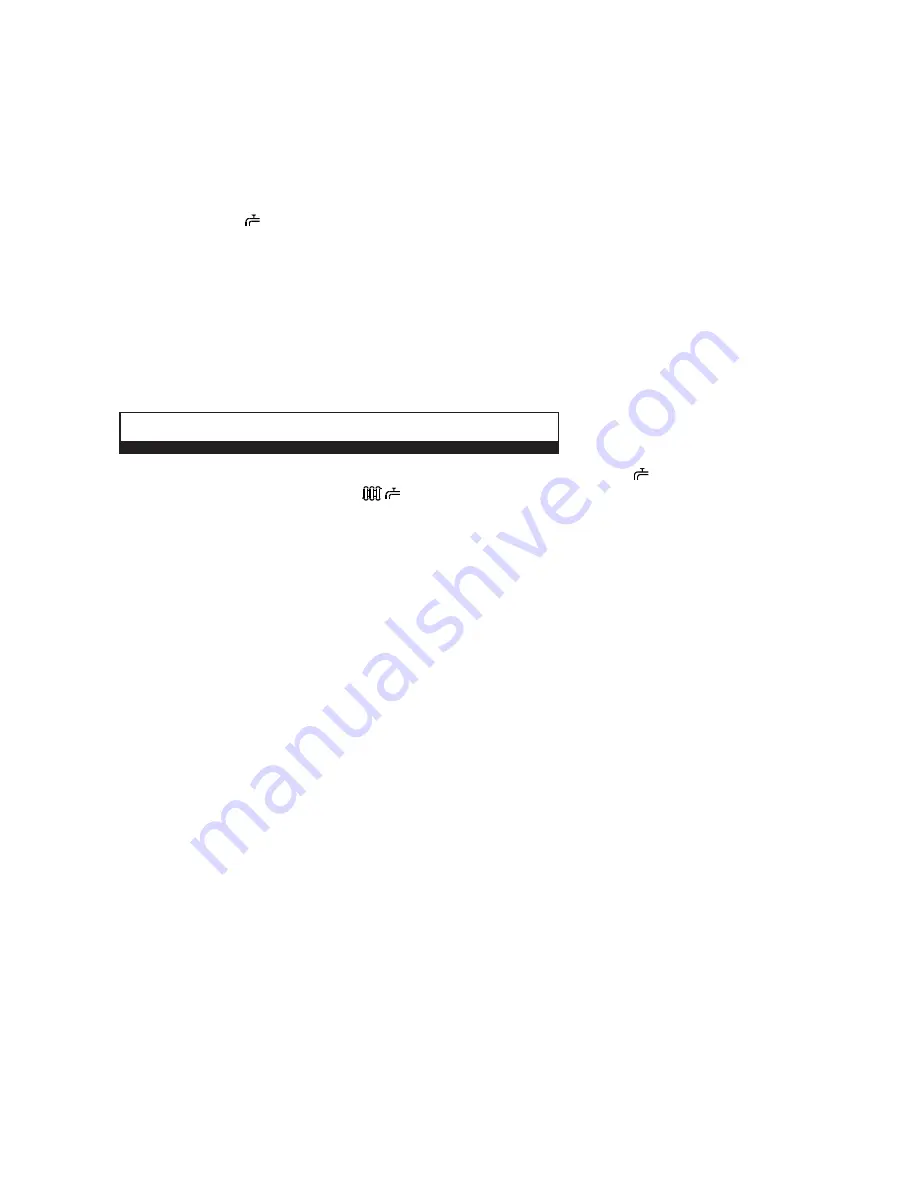
19
Alpha CB50 - Commissioning/Boiler Operation
5.8
USER INFORMATION
The User must be advised (and demonstrated if necessary) of the following important points:-
1.
How to light and turn off the boiler and how to operate the system controls.
2.
The importance of annual servicing of the boiler to ensure safe and efficient operation.
3.
That any servicing or replacement of parts must only be carried out by CORGI registered personnel.
4.
Ensure that the boiler controls and room thermostat (if fitted) are set to the User's requirements.
Note: The DHW (
) thermostat must be set between 7 and 9 to ensure maximum flow rate when a hot water tap is opened.
5.
Tell the User about the sealed system pressure.
6.
Tell the User that if the electrical supply is on and the boiler has not operated for 24 hours for heating or hot water, the
pump will automatically operate for 5 minutes.
7.
Explain to the User that an internal frost thermostat is fitted in the boiler, and that the electrical supply to the boiler must be
left on for the thermostat to operate.
8.
Show the User the position of the pressure relief valve discharge pipe.
9.
Hand the User's instructions and the Benchmark Log Book to the User.
10. Leave these Installation and Servicing instructions with the User for use on future calls.
11. Inform the User that the boiler bottom tray has the facility to store the instructions and log book.
6
BOILER OPERATION
The boiler operating mode is controlled by the selector switch on the facia panel. When set to
, the boiler will only operate in
the Domestic Hot Water mode. When set to
, it will operate in the Domestic Hot Water and Central Heating mode.
Note: The clock (if fitted) only controls the operating times of the central heating, not domestic hot water - DHW is available continuously.
Domestic hot water supply always takes priority over central heating. If a demand for hot water is required during a central
heating period, the boiler will automatically switch to the hot water mode until the demand is satisfied i.e. storage water is to the
required temperature. This interruption in the central heating is only when the demand for hot water is present and should not
be noticed by the User.
6.1
CENTRAL HEATING MODE
If there is a call for central heating the diverter valve is operated, the pump will start to circulate the primary heating water. The
fan will run at full speed; once the air pressure switch is proved the burner will light. The burner output then automatically
adjusts to suit the system demand; as the temperature of the heating water in the boiler approaches that set by the adjustable
central heating thermostat the burner output is reduced. When this set temperature is reached, the burner is turned off and the
fan stops. The pump continues to run for 3 minutes to remove residual heat build up in the boiler. The burner will not relight for
3 minutes; unless there is a demand for domestic hot water during this delay.
In this instance, the boiler will operate to satisfy the domestic hot water demand and the boiler will then immediately revert to
provide central heating, if there is a demand.
6.2
DOMESTIC HOT WATER MODE
When there is a demand for hot water (temperature of stored hot water is below that set by the thermostat), the pump will start to
circulate the primary heating water. The fan will run at full speed; once the air pressure switch is proved the burner will light. The
burner output then automatically adjusts to suit the demand required to raise the temperature of the domestic hot water within the
store to the temperature set by the adjustable domestic hot water thermostat. When this set temperature is reached the burner is
turned off and the fan stops. When the hot water temperature falls below approximately 48°C, the flow regulator valve automatically
reduces the flow of hot water supplied. Hot water is then allowed to be supplied continuously (at a reduced rate) until the stored water
has reheated.
When the hot water demand has been satisfied, the 3-way diverter valve operates to divert the primary heating water to the
central heating, if there is a demand.
6.3
FROST THERMOSTAT
The boiler incorporates a built in frost thermostat which automatically turns on the boiler and pump if the water in the boiler falls
below 8°C, providing the electrical supply is on. The boiler will operate until the water temperature in the system reaches
approximately 40°C.
6.4
PUMP
If the electrical supply is on and the boiler has not operated for 24 hours for heating or hot water, the pump will operate
automatically for five minutes every 24 hours.
Summary of Contents for Alpha CB50 Boiler
Page 29: ...29 9 WIRING DIAGRAMS 9 1 ILLUSTRATED WIRING DIAGRAM Alpha CB50 Wiring Diagrams ...
Page 30: ...30 9 2 FUNCTIONAL FLOW WIRING DIAGRAM Alpha CB50 Wiring Diagrams ...
Page 32: ...32 Alpha CB50 Fault Finding 10 3 DOMESTIC HOT WATER Follow operational sequence ...
Page 33: ...33 Alpha CB50 Fault Finding 10 4 FAULT FINDING SOLUTIONS A to F ...
Page 34: ...34 Alpha CB50 Fault Finding 10 5 FAULT FINDING SOLUTION SECTIONS G to L ...