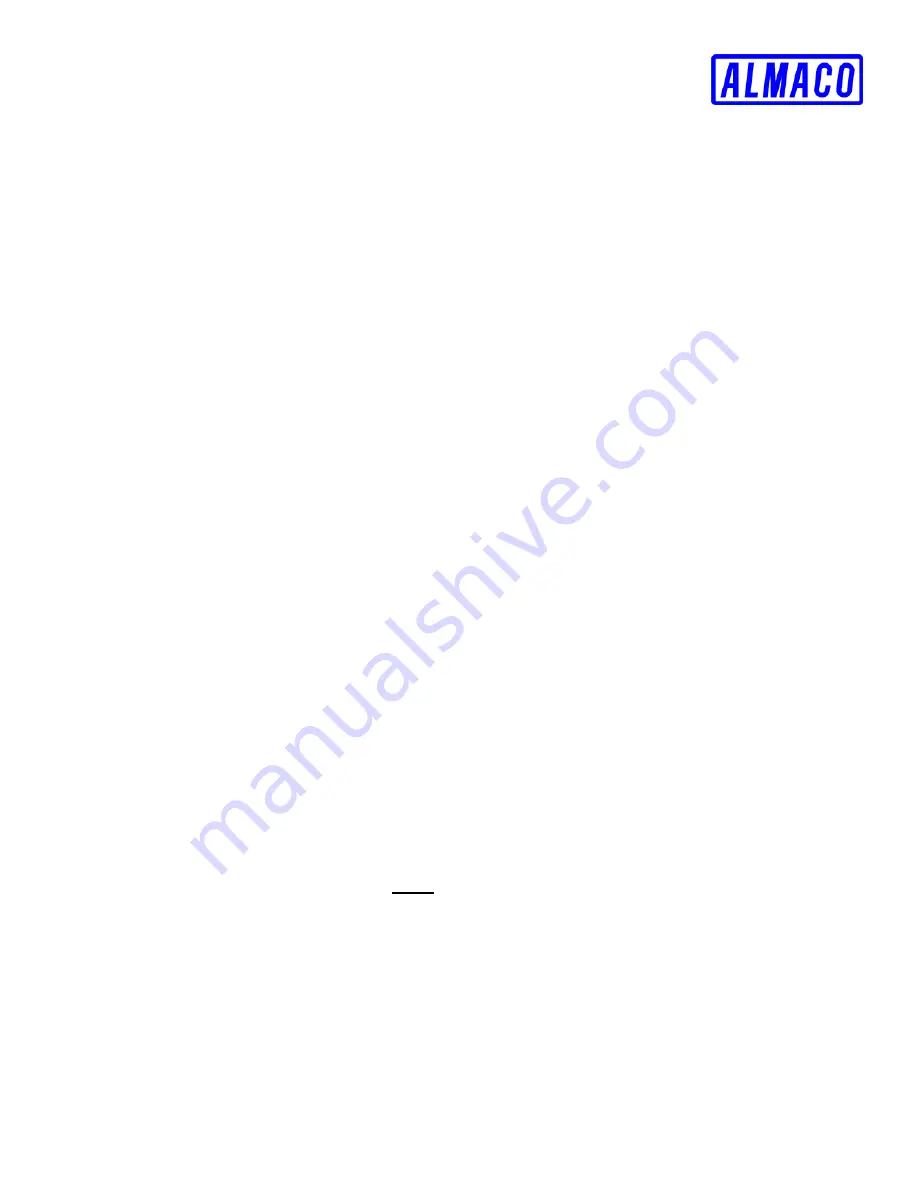
SPC 20
OPERATOR’S MANUAL
MAINTENANCE
E-13
SP Two Fuel Tank and Cap
Most machines produced prior January 1
st
, 1997 are equipped with a copper pick-up tube soldered
into a brass fitting and threaded into the top of the tank. It has a 45° cut on the lower end near the
bottom of the tank. If care was not taken during refueling, debris may have dropped into the fuel and
the pick-up tube may have became plugged or restricted. Remove the tube and blow it out with
compressed air in the opposite direction of fuel flow. Check the solder joint between the tube and
the fitting. If this joint is cracked, air may be sucked into the fuel system and cause a problem similar
to running out of fuel. This vintage will probably not have a filter between the tank and the auxiliary
pump. An after market inline filter such as NAPA #3031 should be installed at this time to protect the
auxiliary pump from plugging due to contamination in the fuel tank.
The standard fuel cap is cast brass and has a vented passage in it that may become plugged. A
cap with a plugged vent hole will cause a vacuum great enough that the auxiliary fuel pump cannot
draw from the tank. If the problem is severe enough, air will be heard rushing into the tank when the
cap is removed. Use compressed air to check and/or clear this passage.
Combines produced after January 1
st
, 1997 are equipped with a sock style filter on the pick-up tube
inside the fuel tank and the inline filter mentioned above. A damaged sock could allow the inline
filter to clog quickly. Most of the HP5 machines are equipped with a removable access plate on the
top of the tank to allow servicing of the sock. SPC20 and PMC20 models are serviced through the
fill neck or fuel gauge holes. They also have a breather style fuel cap that will not plug and a strainer
in the fill neck that can be removed and cleaned.
In-tank socks on pre 1/1/97 models or upgraded machines are serviced through the fill neck fitting or
the fuel gauge sender hole in the top of the tank. The sock is connected to the fitting on the top of
the tank via a length of urethane tubing. It is possible that some fuel additives could attack the
tubing and cause the sock to become disconnected from either the fitting on the sock or the fitting
into the tank. This condition will not allow the pump to pick up fuel from the tank unless it is entirely
full.
CONVEYOR AND ROLLER ADJUSTMENT
When installing replacement belts position the V-guide on the inside of the belt so that it rides in the
center of the V-groove in the roller. All conveyors should run straight and evenly across roller
surfaces without binding or scuffing the side frame. Procedure for proper adjustment is listed below:
1. Determine the cause of malfunction. Note: Belts may stretch somewhat during the break-in
period and may require tension adjustment.
2. Locate the adjustment assembly on either side of roller.
3. Loosen the stop nuts along the threaded rod and draw or extend the rod to obtain the desired
adjustment.
4. Should the conveyor run to one side, extend the threaded rod on that side to correct.
5. Proper Tension - Adjust tension so that all slack is removed and the belt runs evenly. Avoid
over-tightening.
6. Retighten all jam nuts securely.
NOTE:
Over tightening the belt can cause laces to pull apart.
Summary of Contents for SPC 20
Page 2: ......
Page 3: ...SPC 20 OPERATOR S MANUAL FORWARD A 1 SECTION A FORWARD Manual ID Number MOC0207095...
Page 4: ...SPC 20 OPERATOR S MANUAL A 2 FORWARD...
Page 6: ...SPC 20 OPERATOR S MANUAL A 4 FORWARD...
Page 8: ...SPC 20 OPERATOR S MANUAL A 6 FORWARD...
Page 13: ...SPC 20 OPERATOR S MANUAL SAFETY B 1 SECTION B SAFETY...
Page 14: ...SPC 20 OPERATOR S MANUAL B 2 SAFETY...
Page 29: ...SPC 20 OPERATOR S MANUAL OPERATION C 1 SECTION C OPERATION...
Page 30: ...SPC 20 OPERATOR S MANUAL C 2 OPERATION...
Page 44: ...SPC 20 OPERATOR S MANUAL C 16 OPERATION...
Page 45: ...SPC 20 OPERATOR S MANUAL TROUBLESHOOTING D 1 SECTION D TROUBLESHOOTING...
Page 46: ...SPC 20 OPERATOR S MANUAL D 2 TROUBLESHOOTING...
Page 53: ...SPC 20 OPERATOR S MANUAL MAINTENANCE E 1 SECTION E MAINTENANCE...
Page 54: ...SPC 20 OPERATOR S MANUAL E 2 MAINTENANCE...
Page 58: ...SPC 20 OPERATOR S MANUAL E 6 MAINTENANCE SERVICE RECORD DATE SERVICE PERFORMED...
Page 67: ...SPC 20 OPERATOR S MANUAL STORAGE AND TRANSPORTATION F 1 SECTION F STORAGE AND TRANSPORTATION...
Page 68: ...SPC 20 OPERATOR S MANUAL F 2 STORAGE AND TRANSPORTATION...
Page 72: ...SPC 20 OPERATOR S MANUAL F 6 STORAGE AND TRANSPORTATION...
Page 73: ...SPC 20 OPERATOR S MANUAL SPECIFICATIONS G1 SECTION G SPECIFICATIONS...