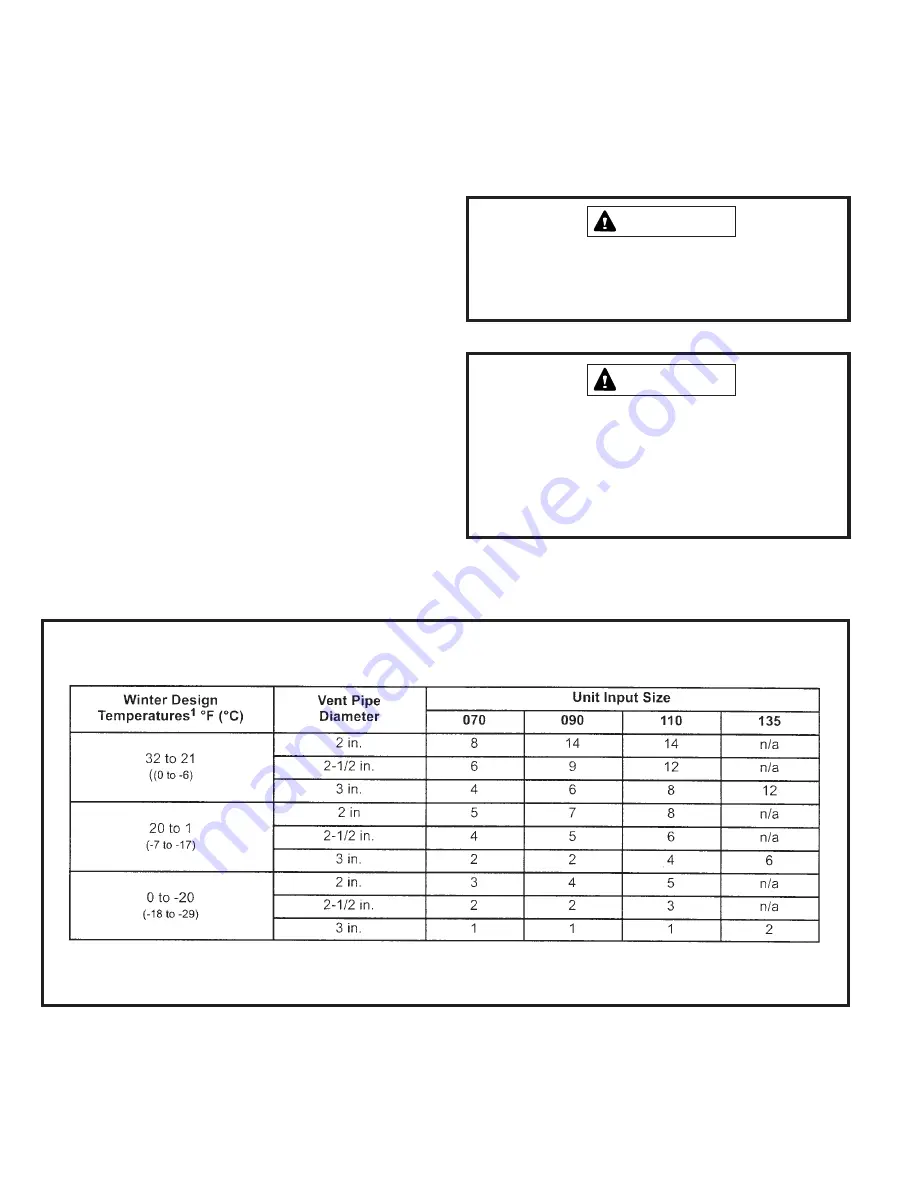
506887-01
Page 20 of 78
Issue 1213
Table 6
Maximum Allowable Vent pipe Length without Insulation in Unconditioned Space for Winter Design
Temperatures Modulating High Efficiency Furnace
¹Refer to 99% Minimum Design Temperature table provided in the current edition of the ASHRAE Fundamentals Handbook.
NOTE: Maximum unisulated vent lengths listed cannot exceedd the maximum allowable intake or exhaust vent length listed in Table 5.
General Guidelines for Vent Terminations
In Direct Vent applications, combustion air is taken from
outdoors and the flue gases are discharged to the outdoors.
This gas furnace is classified as a direct vent, Category IV
gas furnace.
In Direct Vent applications, the vent termination is limited
by local building codes. In the absence of local codes, refer
to the current National Fuel Gas Code ANSI Z223-1/NFPA
54 in U.S.A., and current CSA-B149 Natural Gas and
Propane Installation Codes in Canada for details.
Position termination according to location given in Figure
20. In addition, position termination so it is free from any
obstructions and 12" above the average snow accumulation.
At vent termination, care must be taken to maintain
protective coatings over building materials (prolonged
exposure to exhaust condensate can destroy protective
coatings). It is recommended that the exhaust outlet not
be located within 6 feet (1.8m) of a condensing unit because
the condensate can damage the painted coating.
NOTE:
See Table
6
for maximum allowed exhaust pipe
length without insulation in unconditioned space during
winter design temperatures below 32
°
F
0
°
C)
.
If equired
exhaust pipe should be insulated with
1
/
2
"
(13mm) Armaflex
or equivalent
.
In extreme cold climate areas
,
3
/
4
"
(19mm)
Armaflex or equivalent may be necessary
.
Insulation on
outside runs of exhaust pipe must be painted or wrapped
to protect insulation from deterioration
.
Exhaust pipe
insulation may not be necessary in some specific
applications
.
Do not use screens or perforated metal in exhaust
terminations. Doing so will cause freeze-ups and may
block the terminations.
IMPORTANT
FOR CANADIAN INSTALLATIONS ONLY:
In accorddance to CSA International B149 installation
codes, the minimum allowed distance between the
combustion air intake inlet and the exhaust outlet of other
appliances shall not be less than 12 inches (305 mm).
IMPORTANT
Summary of Contents for A97USMV
Page 3: ...506887 01 Page 3 of 78 Issue 1213 A97USMV Exploded View Figure 1 ...
Page 16: ...506887 01 Page 16 of 78 Issue 1213 Figure 17 ...
Page 28: ...506887 01 Page 28 of 78 Issue 1213 Trap Drain Assembly using 1 2 PVC or 3 4 PVC Figure 38 ...
Page 35: ...506887 01 Page 35 of 78 Issue 1213 ...
Page 36: ...506887 01 Page 36 of 78 Issue 1213 Figure 46 ...
Page 39: ...506887 01 Page 39 of 78 Issue 1213 ...
Page 40: ...506887 01 Page 40 of 78 Issue 1213 Typical A97USMV Wiring Diagram Figure 47 ...
Page 41: ...506887 01 Page 41 of 78 Issue 1213 Integrated Control Figure 48 ...
Page 42: ...506887 01 Page 42 of 78 Issue 1213 Low Voltage Field Wiring Table 14 2 Stage Single Stage ...
Page 46: ...506887 01 Page 46 of 78 Issue 1213 BLOWER DATA ...
Page 47: ...506887 01 Page 47 of 78 Issue 1213 BLOWER DATA ...
Page 48: ...506887 01 Page 48 of 78 Issue 1213 BLOWER DATA ...
Page 49: ...506887 01 Page 49 of 78 Issue 1213 BLOWER DATA ...
Page 50: ...506887 01 Page 50 of 78 Issue 1213 BLOWER DATA ...
Page 51: ...506887 01 Page 51 of 78 Issue 1213 BLOWER DATA ...
Page 52: ...506887 01 Page 52 of 78 Issue 1213 BLOWER DATA ...
Page 53: ...506887 01 Page 53 of 78 Issue 1213 BLOWER DATA ...
Page 54: ...506887 01 Page 54 of 78 Issue 1213 BLOWER DATA ...
Page 55: ...506887 01 Page 55 of 78 Issue 1213 TABLE 22 ...
Page 56: ...506887 01 Page 56 of 78 Issue 1213 TABLE 23 ...
Page 60: ...506887 01 Page 60 of 78 Issue 1213 Figure 50 ...
Page 68: ...506887 01 Page 68 of 78 Issue 1213 ...
Page 69: ...506887 01 Page 69 of 78 Issue 1213 ...