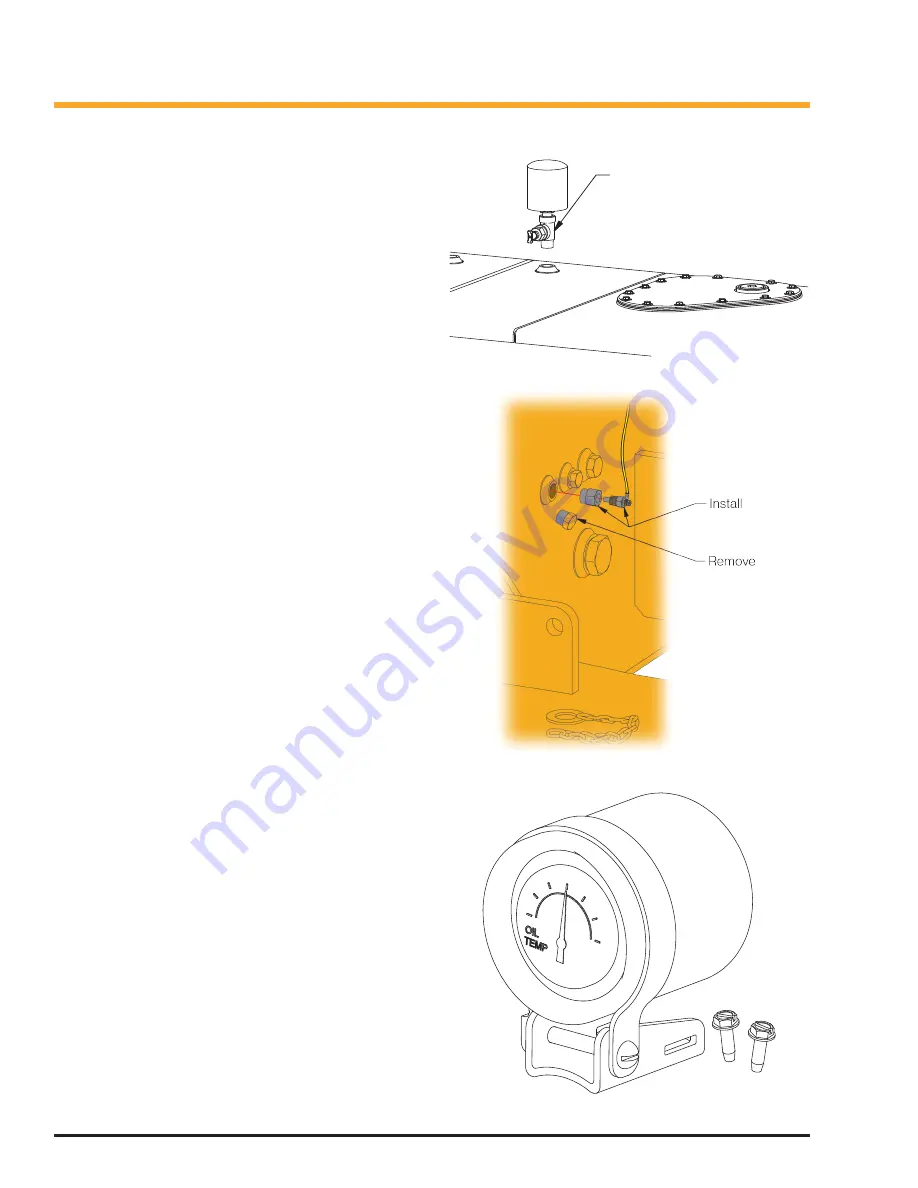
6
80-1056
Rev: 8-2014
Remove and use
vacuum to create
negative pressure
in tank.
DO NOT plug the wire harnesses to the
monitor yet.
17. To install the temperature sensor, an unused drain
plug in the hydraulic tank must be removed.
18. Either drain the hydraulic tank prior to removing
the plug in step 20, or use a vacuum to create
negative pressure in the tank as described in step
19.
19. To create negative pressure in the tank:
a. Relieve pressure in the hydraulic tank by
opening the petcock
b. Remove the petcock/air breather assembly.
See
Figure 6
.
c. Attach a vacuum to the open port to create
negative pressure in the tank. The negative
pressure will allow the drain plug to be re-
moved without spilling oil.
20. Remove a 3/4” drain plug from the side of hydrau-
lic tank integral to the chassis. See
Figure 7
.
21. Install the bushing and temperature sensor as
shown in
Figure 7
.
22. The temperature sensor has NPTF threads, and
does not require pipe sealant. Use a light ap-
plication of pipe sealant to the external bushing
threads. Metal to metal contact is required at the
threads for proper sensor grounding.
23. With the temperature sensor securely installed,
turn off the vacuum, and reinstall the petcock/air
breather assembly.
24. Route the yellow wire from the temperature sen-
sor to the terminal block labeled “A” in
Figure 2
.
Secure the wire so that it will not be damaged or
snagged during normal operation or maintenance.
Strip 5/16” of the insulation from the wire, and
install at the terminal as shown in
Figure 2
.
25. Mount the hydraulic temperature gauge in the cab,
in a location visible to the operator, where it does
not obscure any other gauge or control. Use the
self-tapping screws included in the kit to mount
the gauge. Use a 11/64” drill for pilot holes.
26. Route the temperature gauge wire harness back
to the console or terminal panel assembly. The
wire harness may be cut to length to simplify
installation and wire routing. Make sure not to cut
the wire harness too short.
27. Strip 5/16” of the insulation from the wire, and
install at terminals “A”, “B”, “C”, and “D” as shown
in
Figure 2
.
28. At this time, reconnect the wires that were previ-
ously disconnected from the 2-position terminal
Figure 6
Hydraulic Tank Breather
Figure 7
Sensor Installation
Figure 8
Hyd Oil Temp Gauge