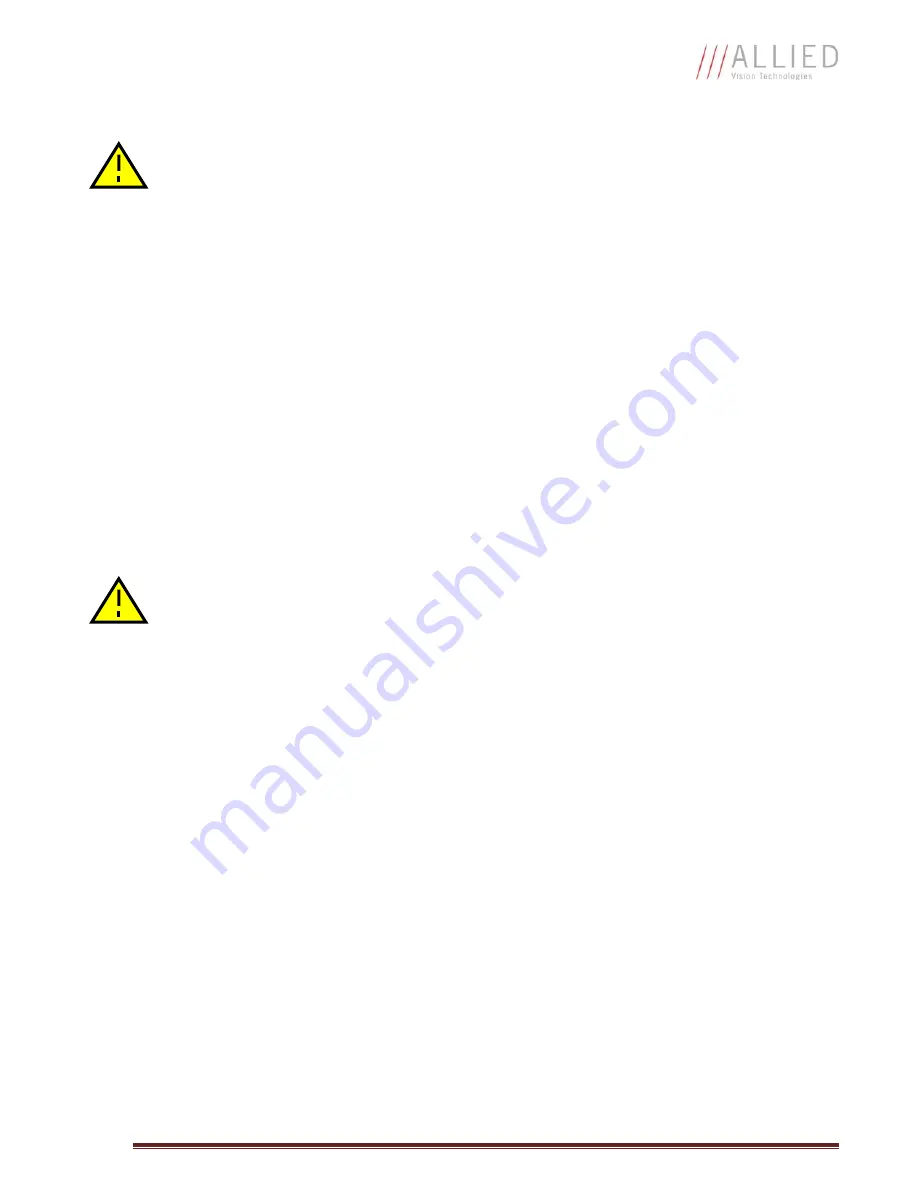
GC1020 Technical Manual
Page 9
Cleaning the Sensor
DO NOT CONTACT CLEAN SENSOR UNLESS ABSOLUTELY NECESSARY.
Identifying Debris
Debris on the image sensor or optical components will appear as a darkened area or smudge on the
image that does not move as the camera is moved. Do not confuse this with a pixel defect which
will appear as a distinct point.
Locating Debris
Before attempting to clean the image sensor, it is important to first determine that the problem is
due to debris on the sensor window. To do this you should be viewing a uniform image, such as a
piece of paper, with the camera. Debris will appear as a dark spot or dark region that does not
move as the camera is moved. To determine that the debris is not on the camera lens, rotate the
lens independent of the camera. If the spot moves as the lens moves, then the object is on the
lens -not on the image sensor- and therefore cleaning is not required. If the camera has an IR
filter, then rotate the IR filter. If the object moves then the particle is on the IR filter not the
sensor. If this is the case remove the IR filter carefully using a small flat head screw driver. Clean
both sides of the IR filter using the same techniques as explained below for the sensor window.
DO NOT TOUCH ANY OPTICS WITH FINGERS. OIL FROM FINGERS CAN DAMAGE FRAGILE
OPTICAL COATINGS.
Cleaning with Air
If it is determined that debris is on the sensor window, then remove the camera lens, and blow the
sensor window directly with clean compressed air. If canned air is used, do not shake or tilt the
can prior to blowing the sensor. View a live image with the camera after blowing. If the debris is
still there, repeat this process. Repeat the process a number of times with increased intensity until
it is determined that the particulate cannot be dislodged. If this is the case then proceed to the
contact cleaning technique.
Contact Cleaning
Only use this method as a last resort. Use 99% laboratory quality isopropyl alcohol and clean
cotton swabs. Dampen the swab in the alcohol and gently wipe the sensor in a single stroke. Do
not reuse the same swab. Do not wipe the sensor if the sensor and swab are both dry. You must
wipe the sensor quickly after immersion in the alcohol, or glue from the swab will contaminate the
sensor window. Repeat this process until the debris is gone. If this process fails to remove the
debris, then contact AVT.