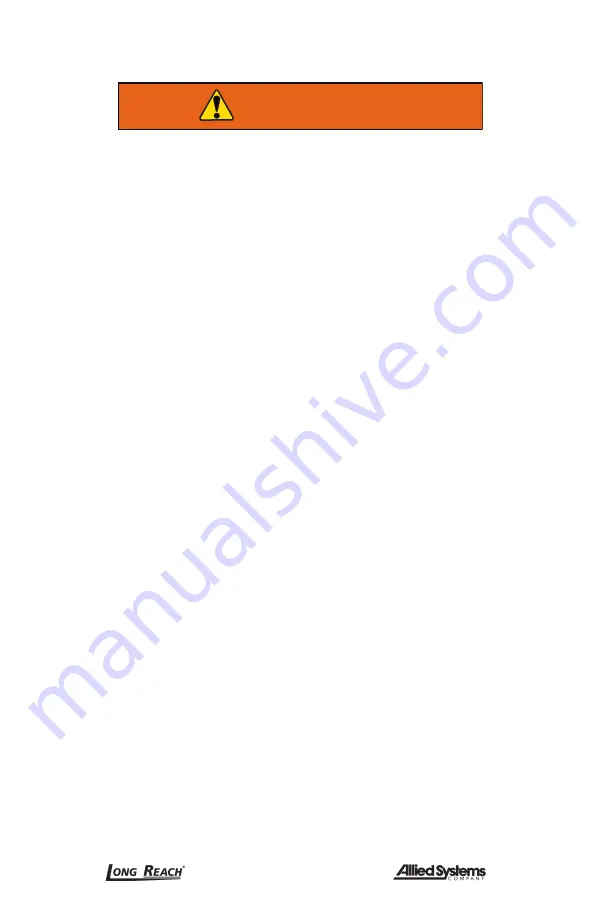
45-031 REV. 11/19
18
10. If quick hooks are installed, simply raise the slide plate until the button clicks into
place.
WARNING
Equipment failure hazard.
The attachment could fall off the truck if the quick hook
is not properly installed.
Slide plate must click into place. If the slide plate does
not click into place because the truck carriage prevents
the slide plate from being raised up high enough, install
shims between the attachment and the body of the quick
hooks.
11. To ensure proper locking of the slide plate, use a screwdriver to try to pry down the
slide plate. If the slide plate is not locked in place, inspect and correct any cause
that might restrict the slide plate from going up enough to allow the button to become
fully engaged.
12. Check all fittings, connections and bolts for any interference.
4.3 Hydraulic Connections
1. Install the lines from the truck’s hydraulics to the hydraulics of the attachment.
2. Inspect installation to ensure hoses are not kinked or pinched between the truck
carriage and attachment.
3. Operate the attachment continuously for several minutes to determine that all
hydraulic connections are secure with no leaks.
4. With the mast in the vertical position, rotate the attachment fully 360°. After this
procedure, check that the truck’s hydraulic reservoir oil level is at the recommended
level.
5. Before placing the attachment in operation inspect all hoses and fittings for leaks
and routing clearance. Be sure to include clearance of jumper hoses to the mast.
6. After completing the installation, operate the attachment without a load for several
cycles to remove any air in the hydraulic system. Test the attachment with a load
to make sure the attachment operates correctly.