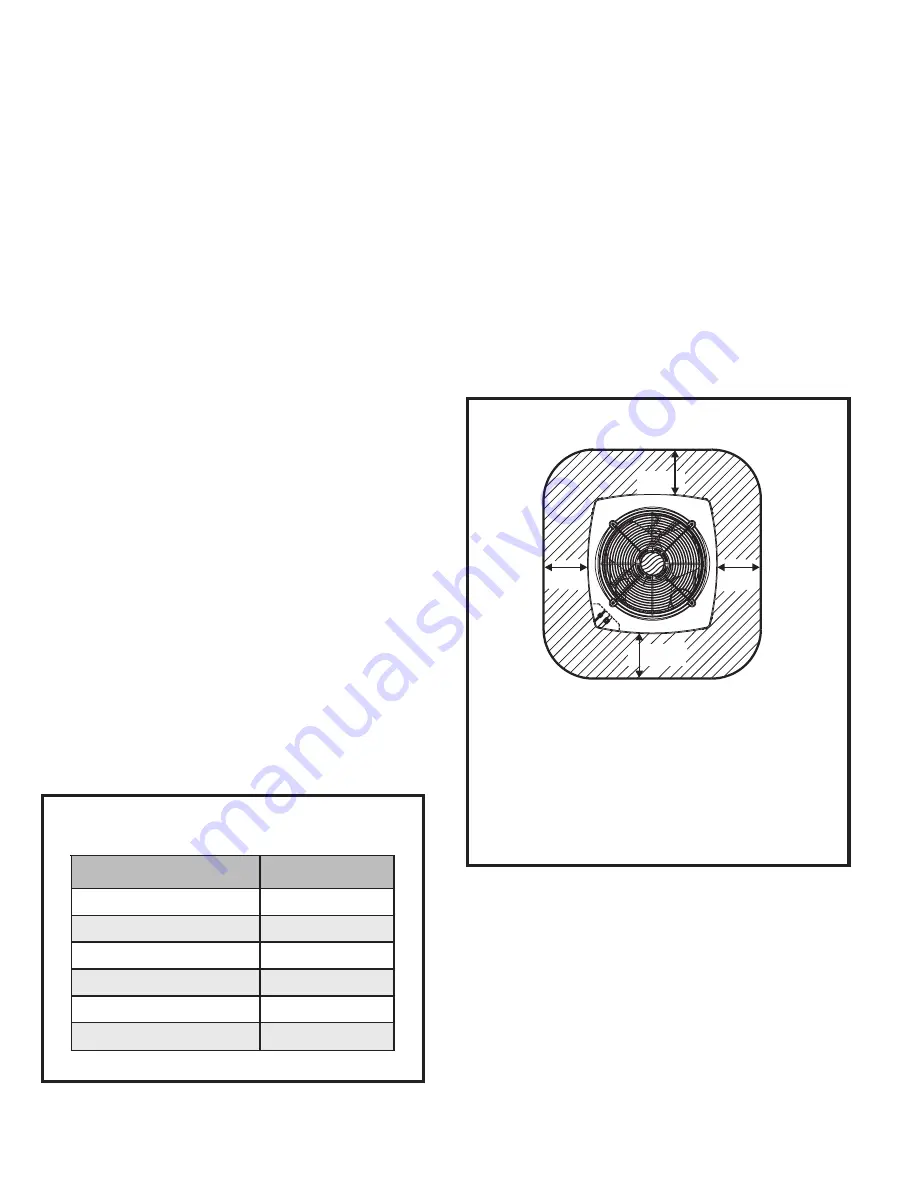
Page 2
Issue 0912 506253-01
INSTALLATION
Inspection of Shipment
Upon receipt of equipment, carefully inspect it for possible
shipping damage. If damage is found, it should be noted
on the carrier’s freight bill. Take special care to examine
the unit inside the carton if the carton is damaged. Any
concealed damage discovered should be reported to the
last carrier immediately, preferably in writing, and should
include a request for inspection by the carrier’s agent.
If any damages are discovered and reported to the carrier
DO NOT INSTALL THE UNIT
, as claim may be denied.
Check the unit rating plate to confirm specifications
are as ordered.
Location of Unit
Refer to Figure 1 for installation clearances.
General
Read this entire instruction manual, as well as the
instructions supplied in separate equipment, before
starting the installation. Observe and follow all warn-
ings, cautions, instructional labels, and tags. Failure
to comply with these instructions could result in an
unsafe condition and/or premature component failure.
These instructions are intended as a general guide only
for use by qualified personnel and do not supersede any
national or local codes in any way. The installation must
comply with all provincial, state, and local codes as well as
the National Electrical Code (U.S.) or Canadian Electrical
Code (Canada). Compliance should be determined prior
to installation.
4SCU16LT condensing units use R410A which is an
ozone-friendly HFC refrigerant. The unit must be installed
with a matching indoor coil and line set. 4SCU16LT units
are designed for use in expansion valve (TXV) systems
only. The TXV expansion valve must be ordered sepa-
rately from the manufacturer. A filter drier approved for
use with 410A is installed in the unit.
IMPORTANT: This product has been designed and manu-
factured to meet ENERGY STAR criteria for energy effi-
ciency when matched with appropriate coil components.
However, proper refrigerant charge and proper air flow are
critical to achieve rated capacity and efficiency. Installation
of this product should follow the manufacturer’s refrigerant
charging and air flow instructions.
Failure to confirm
proper charge and airflow may reduce energy effi-
ciency and shorten equipment life.
When servicing or repairing HVAC components, ensure
the fasteners are appropriately tightened. Table 1 shows
torque values for fasteners.
Slab Mounting
When installing unit at grade level, install on level slab
high enough so that water from higher ground will not
collect around unit (see Figure 2).
Roof Mounting
Install unit at a minimum of 4" above surface of the roof.
Care must be taken to ensure weight of unit is properly
distributed over roof joists and rafters. Either redwood or
steel supports are recommended.
Torque Table
Table 1
r
e
n
e
t
s
a
F
e
u
q
r
o
T
s
p
a
C
m
e
t
S
.
s
b
l
.
t
f
8
s
p
a
C
t
r
o
P
e
c
i
v
r
e
S
.
s
b
l
.
t
f
8
s
w
e
r
c
S
l
a
t
e
M
t
e
e
h
S
.
s
b
l
.
n
i
6
1
s
w
e
r
c
S
e
n
i
h
c
a
M
8
#
.
s
b
l
.
n
i
6
1
s
w
e
r
c
S
e
n
i
h
c
a
M
0
1
#
.
s
b
l
.
n
i
8
2
s
t
l
o
B
r
o
s
s
e
r
p
m
o
C
.
s
b
l
.
n
i
0
9
Figure 1
Installation Clearances
* A service clearance of 30" must be maintained on
one of the sides adjacent to the control box.
Clearance to one of the other three sides must be
36". Clearance to one of the remaining two sides
may be 12" and the final side may be 6".
A clearance of 24" must be maintained between units.
48" clearance required on top of unit. Maximum soffit
overhang is 36".
36 *
"
36
"
36
"
36 *
"