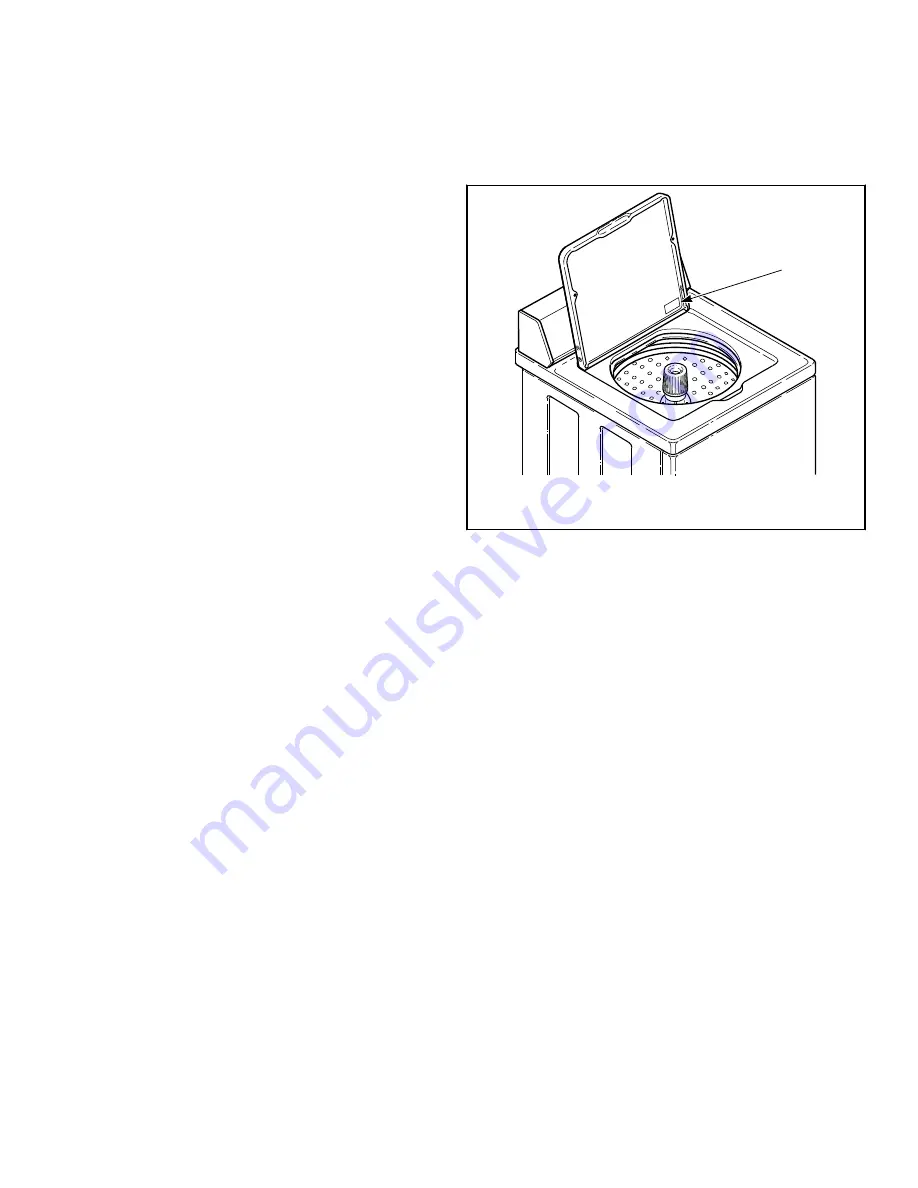
with water until the air pressure hose reaches a level determined
by the selected water level (load size switch setting) and the se-
lected cycle. The water will stop filling at the minimum level for
the selected cycle when Auto Fill is selected. In either case, the
washer will begin load sensing to determine if more water is re-
quired for the actual load in the washer and the cycle selected.
The wash agitation segment of the cycle begins at this time and
the lid must be closed and locked for any further washer opera-
tion. On non-Eco cycles, after approximately two minutes of
wash, the washer repeats the load sensing process to confirm that
the water level is still correct for the load and cycle selected.
The washer uses a reversing type of inverter drive motor and a
special stretch drive belt.
During agitation, the motor alternates between the clockwise and
counterclockwise direction. The rapid reversal from one direction
to the other creates the wash action. The stretch belt needs no ad-
justment for belt tension. Proper belt tension is provided by the
pulley spacing and use of the proper size stretch belt. This elimi-
nates belt slippage and ensures an efficient wash action.
After the wash agitation is complete and a short pause occurs, the
control advances into the wash spin. During spin, the washtub
will first rotate at 20 RPM while the electric pump runs to drain
the water from the tub. Once the pressure sensor recognizes that
the tub has been drained, the RPM will increase to extract water
from the load and the pump will continue running to remove the
water.
Water is introduced during the wash spin to spray the garments
and remove suds from them. The wash spin is followed by a rinse
step to rinse away any detergent residue.
During the rinse step in the Normal Eco cycle there will be two
more spray rinses. Water is sprayed into the washtub while it is
spinning. In all other cycles, the washer fills and then agitates
like the wash portion of the cycle.
Following the rinse step a final spin extracts the rinse water from
the clothes preparing them for the dryer. This will also start at 20
RPM with the pump running. After draining the spin will then in-
crease to a higher speed that varies depending on what cycle has
been selected. After the machine has been in spin long enough to
ensure that most of the water has been removed from the load,
the pump will run intermittently for the rest of the spin in order to
improve drain performance and reduce noise.
Refer to Cycle Sequence Charts section for a detailed breakdown
of each cycle.
Customer Service
If literature or replacement parts are required, contact the source
from whom the machine was purchased or contact Alliance
Laundry Systems at (920) 748-3950 for the name and address of
the nearest authorized parts distributor.
For technical assistance, call (920) 748-3121.
Serial Plate Location
When calling or writing about your product, be sure to mention
model and serial numbers. Model and serial numbers are located
on Serial Plate as shown.
TLW1851P_SVG
1
1.
Serial Plate
Figure 2
Introduction
©
Copyright, Alliance Laundry Systems LLC -
DO NOT COPY or TRANSMIT
9
Part No. 204560ENR1
Summary of Contents for ZWNE8RSN115FW01
Page 2: ......