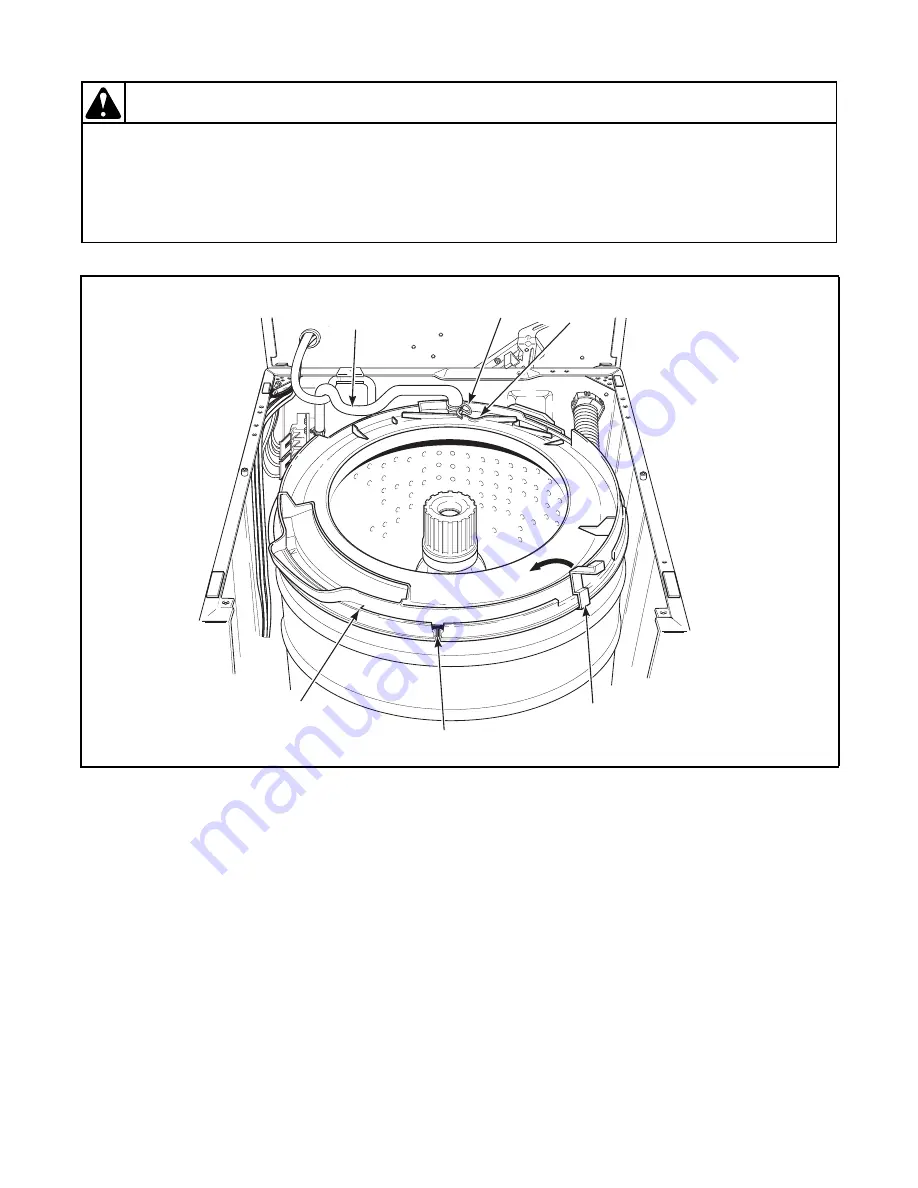
37987
39
Section 5 Service Procedures
To reduce the risk of electric shock, fire, explosion, serious injury or death:
• Disconnect electric power to the washer before servicing.
• Never start the washer with any guards/panels removed.
• Whenever ground wires are removed during servicing, these ground wires must be
reconnected to ensure that the washer is properly grounded.
W003
WARNING
© Copyright, Alliance Laundry Systems LLC – DO NOT COPY or TRANSMIT
37. WASHTUB AND CLOTHES GUARD
a. Open loading door.
b. Remove agitator by placing two agitator hooks,
No. 254P4P, under bottom edge of agitator.
Refer to Figure 12.
IMPORTANT: Hooks should be positioned 180
degrees of each other, and must be placed under
agitator vane for greater stability. If hooks are
placed between vane area, agitator damage may
occur.
c. Using a rocking motion (back and forth)
carefully lift agitator off drive bell.
d. Hinge cabinet top or remove. Refer to
e. Loosen hose clamp and remove filler hose from
outer tub cover. Refer to Figure 32.
NOTE: When installing filler hose, white line on
hose must be aligned with line located on top side of
outer tub cover. Refer to Figure 32.
f. There are eight tub cover hold-down tabs which
snap over outer tub flange. Using special tub
cover tool, Part No. 273P4, insert two prongs of
tool underneath each side of tandem tabs. Refer
to Figure 32. Tilt tool toward center of tub
cover and at same time lift upward on cover to
unsnap hold-down tabs from outer tub flange.
One by one, disengage each of the eight hold-
down tabs from outer tub flange and remove
cover.
Figure 32
W
3
51
S
E
3
A
Line On
Cover
Ho
s
e
Clamp
Filler
Ho
s
e
Hold-Down
Tab
s
Outer
Tub Cover
27
3
P4
Tub Cover
Tool