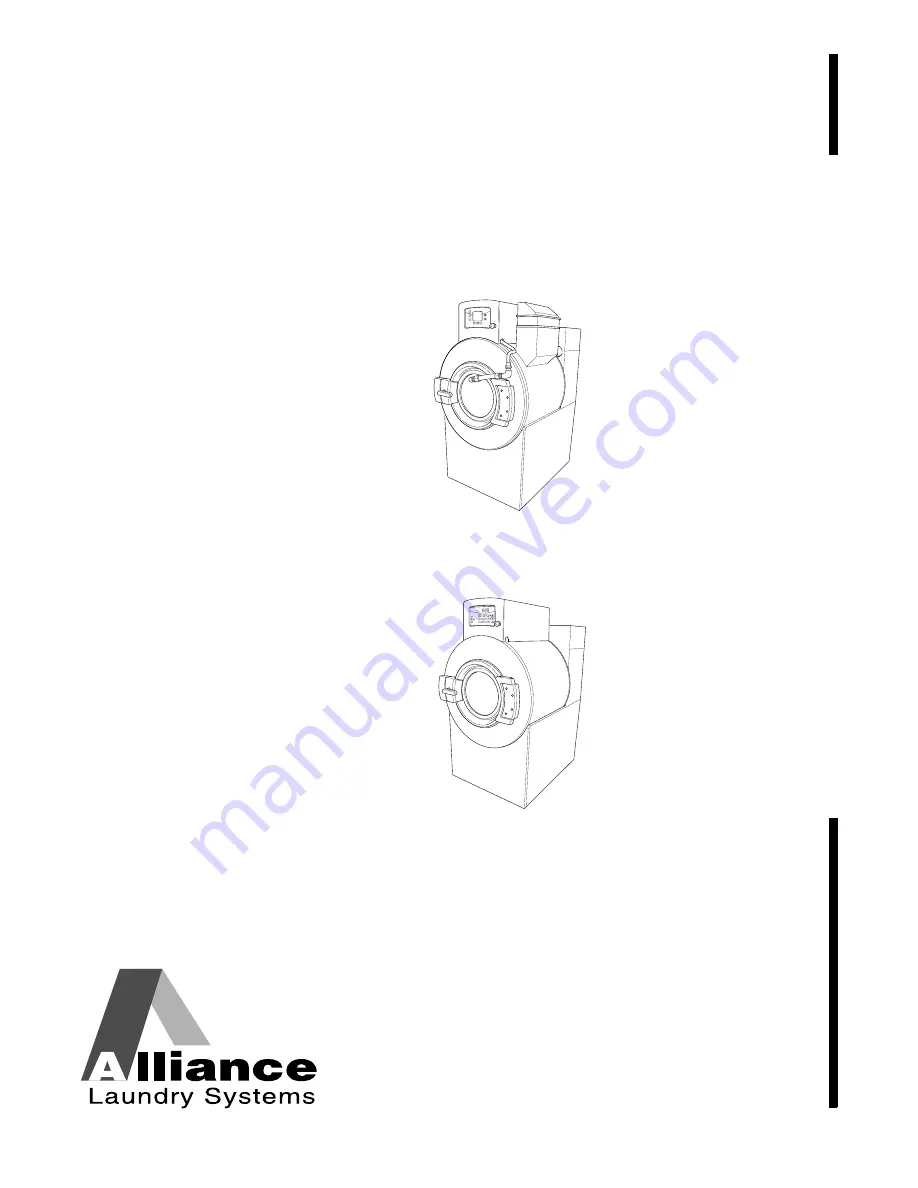
Installation/Operation/Maintenance
www.alliancelaundry.com
Washer-Extractors
Pocket Hardmount
UniLinc and M30 Control
Refer to Page 6 for Model Numbers
PHM848N
PHM847N
UniLinc
45 AND 65 MODELS
M30
45 AND 65 MODELS
PHM847N
PHM848N
Part No. F8410701ENR3
November 2012
Keep These Instructions for Future Reference.
(If this machine changes ownership, this manual must accompany machine.)