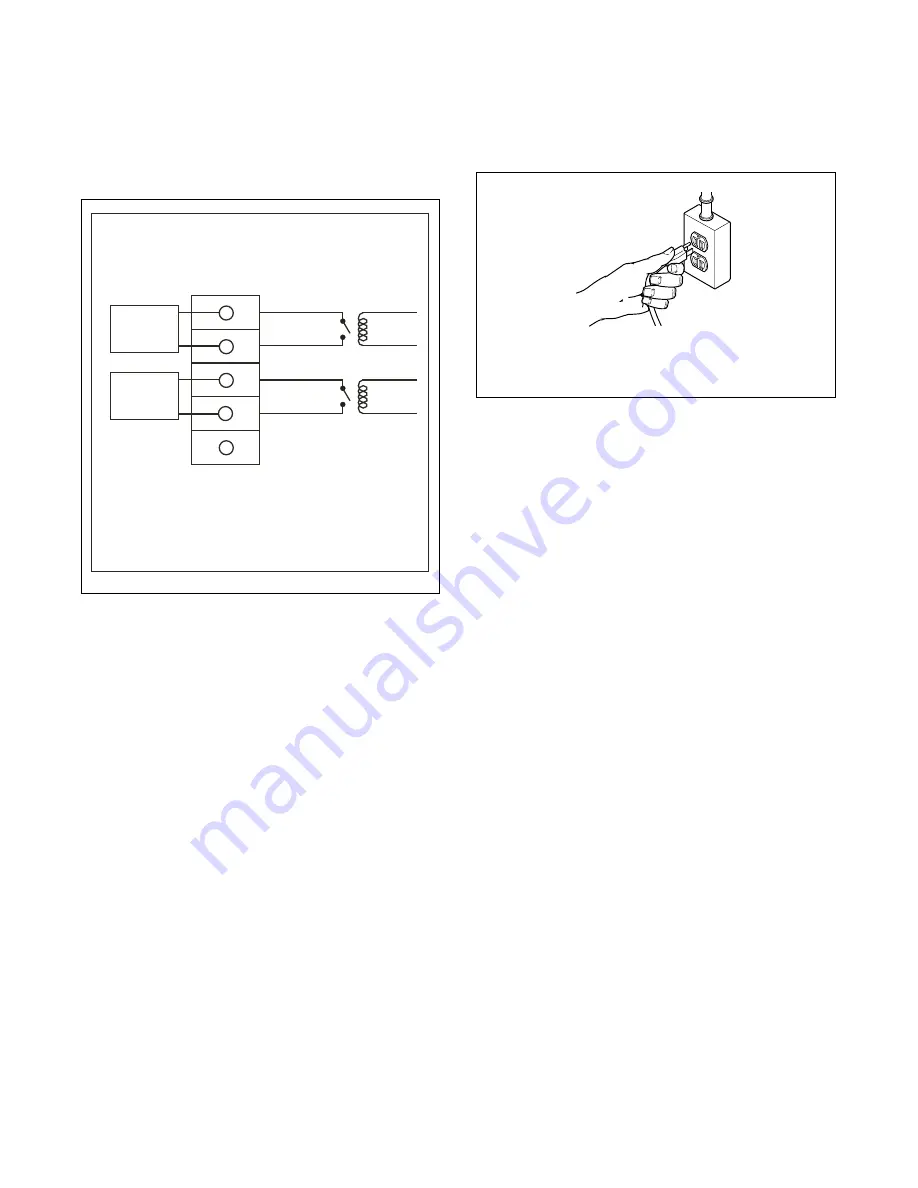
Installation
11
801455
© Copyright, Alliance Laundry Systems LLC – DO NOT COPY or TRANSMIT
A junction box on the rear panel houses a terminal
strip which furnishes supply output signals for the
supply injection pumps.These are dry contacts.
Voltage needs to be supplied. Refer to
Figure 14
for
the injection interface label.
These terminals may be used to provide signals to the
supply injection system but must not be used to
provide power to the actual pump.
Any injection system pump which requires
110 VAC must be powered by a separate external
power source.
Control Function Test
The washer should be cleaned after the installation is
complete. A function test should then be executed on
the unloaded machine:
1. Check the power supply for such characteristics
as correct voltage, phase, and cycles to be certain
they are correct for the washer.
2. Open manual shut-off valves to the washer.
3. Apply power to the washer.
Step 8: Plug In the Washer
Refer to section on
Electrical Requirements
and connect
the washer to an electrical power source.
Step 9: Check Installation
Refer to
Installer Checklist
on the back cover and
make sure that unit is installed correctly.
Moving Unit to a New Location
To prevent damage while moving the unit, the
shipping materials MUST BE reinstalled.
Reinstallation of Shipping Materials
Disconnect washer from electrical supply.
Remove front access panel by removing two screws.
Place the shock sleeves on all four shock absorbers.
Refer to
Figure 16
.
Insert hooked end of shipping brace into the open slot
of the motor mount. Attach with bolts and lockwashers.
Refer to
Figure 16
.
Reinstall front access panel.
FLW2028N
Figure 14
DETERGENT
DISPENSER
CONNECTION
SOFTENER
DISPENSER
CONNECTION
SOFTENER
RELAY
DETERGENT
RELAY
CHEMICAL INJECTION
ELECTRICAL INTERFACE
NO CONNECTION
TERMINAL
BLOCK
YELLOW
YELLOW/BLACK
RED
RED/BLACK
801653R1
NOTE: Normally Open Contacts.
Contacts Close to Start Chemical Injection.
Maximum Load Connection per Contact:
1A @ 120VAC/240VAC
D254I
Figure 15
D254I
Plug cord into separately fused 15 Amp circuit.