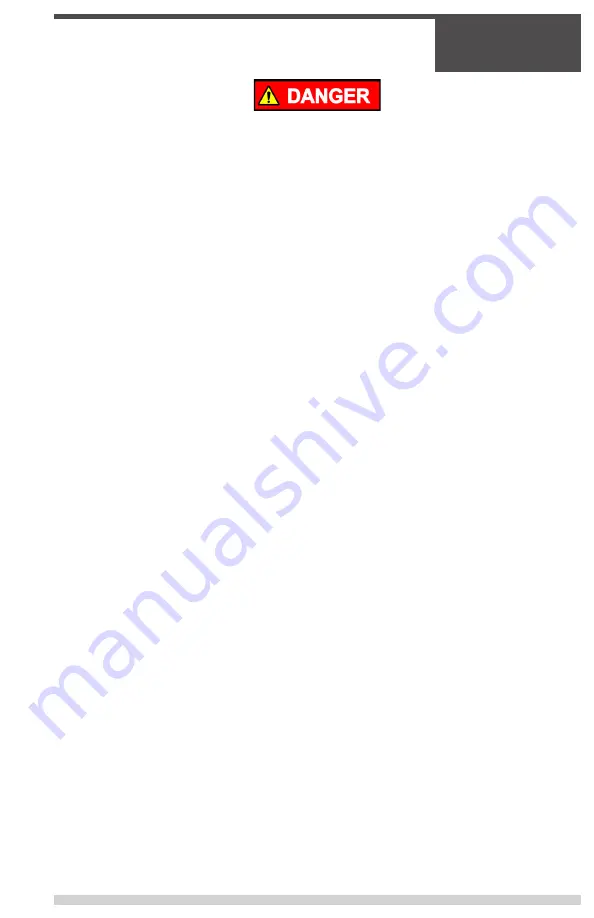
068521
Page 15
SECTION 1
SAFETY
Engine Safety
Internal combustion engines present special hazards during operation and fueling.
Read and follow the warning instructions in the engine owner’s manual and the safe-
ty guidelines below. Failure to follow the warnings and safety guidelines could result
in severe injury or death.
• DO NOT
run the machine indoors or in an enclosed area such as a deep trench unless
adequate ventilation, through such items as exhaust fans or hoses, is provided. Exhaust
gas from the engine contains poisonous carbon monoxide gas; exposure to carbon mon-
oxide can cause loss of consciousness and may lead to death.
• DO NOT
smoke while operating the machine.
• DO NOT
smoke when refueling the engine.
• DO NOT
use fuel that is more than 90 days old. Use of unmixed, improperly mixed,
or fuel older than 90 days, (stale fuel), may cause hard starting, poor performance, or
severe engine damage and void the product warranty.
• DO NOT
refuel a hot or running engine.
• DO NOT
refuel the engine near an open flame.
• DO NOT
spill fuel when refueling the engine.
• DO NOT
run the engine near open flames.
• ALWAYS
refill the fuel tank in a well-ventilated area.
• ALWAYS
replace the fuel tank cap after refueling.
• ALWAYS
keep the area around the muffler free of debris such as leaves, paper, cartons,
etc. A hot muffler could ignite the debris and start a fire.
Summary of Contents for WB1224
Page 10: ...SECTION 1 SAFETY 068521 Page 10 SECTION 1 SAFETY ...
Page 20: ...SECTION 2 ASSEMBLY 068521 Page 20 SECTION 2 ASSEMBLY ...
Page 24: ...SECTION 3 PARTS 068521 Page 24 SECTION 3 PARTS ...
Page 38: ......
Page 39: ......