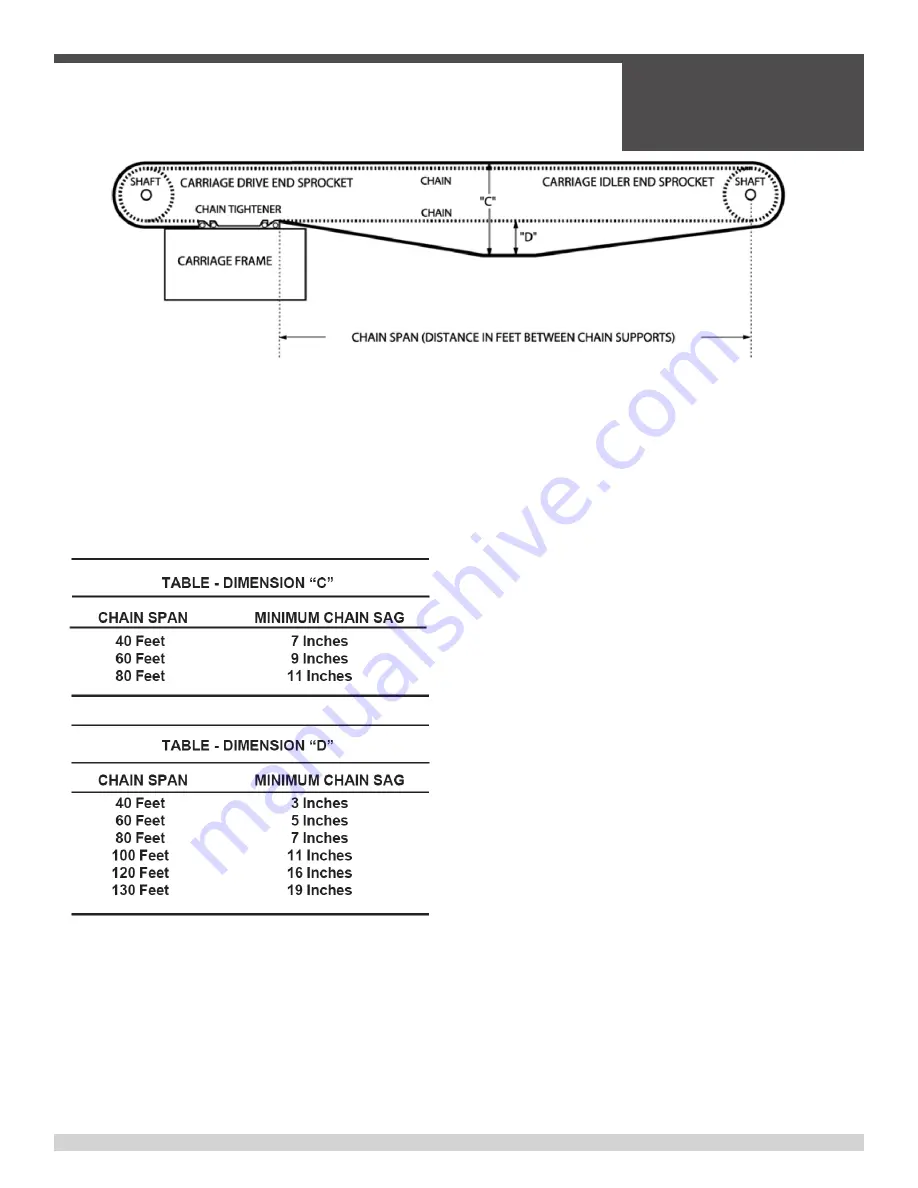
To determine the amount of chain sag needed, move the carriage to
one end of the machine and measure the distance between the top
and the bottom of the chain in the center of the machine. It is rec-
ommended that the chain sag should not be less than the distances
for dimensions “C” and/or “D” shown in the representative tables
below. If the chain tension is too great, excessive chain wear may
result. If the chain tension is too slack, excessive sprocket wear and/
or improper carriage reversal may result. NOTE: These dimensions
are for a straight machine. Readjust for machines with a crown.
15. MACHINE GRADE
- To set the machine to grade, move the
carriage to a place where the front end of the paving rollers are
over the top of a bulkhead, expansion joint or end dam that is on
grade. Using the leg cranks lower the paving rollers so that they
are just touching or are slightly above the bulkhead joint or end
dam. Move the carriage along the graded area from one side to
the other. When satisfied that the grade of the paving rollers is
correct, measure each leg, front and rear, from the screed pipe to
the carriage rail. The measurement should be the same, front and
rear, on each end of the machine. Use the leg cranks to correct
any discrepancies.
16. DRY RUN
- The machine is now ready for a “Dry Run” of
the entire deck or slab. The checking of bulkheads, end dams,
expansion joints and depth checks can be done by inspecting
personnel. This time allows the operator to become familiar with
the controls and the operation of the machine. If any corrections
or adjustments need to be made it is usually done by adjustments
in the screed pipe.
17. PRE-POUR INSPECTION
- Thoroughly inspect the machine
before pouring concrete. For best performance, lubricate all mov-
ing parts. Be sure to coat any part that might be exposed to wet
concrete with oil. Make sure that all engines have been serviced
properly. Avoid getting any dirt or other contaminates into the
hydraulic system. Use clean containers to add hydraulic fluid to
the hydraulic tanks. Thoroughly clean all hydraulic components
before loosening or disassembling. Wipe clean all hydraulic hose
disconnects before reassembling.
PAVING PROCEDURE
1. ADJUST ROLLERS AND DRAG PAN
- After the pour has
started and the machine has moved out from the end bulkhead
or has passed over the bulkhead the full length of the paving
roller, raise the back of the machine 1/8 of an inch by turning
the leg cranks 1/2 turn counter clockwise. This will keep the rear
of the paving rollers from digging in and leaving a small ridge of
concrete. It may be necessary to readjust the augers, up or down,
to obtain or reduce the roll of concrete. Optimum is golf ball size
in diameter at the front of the paving roller. As the machine pro-
gresses into the pour and clears the bulkhead or end dam, attach
the burlap or astrograss drag to the drag pan.
NOTE: The burlap drag should be wet. If new burlap is being
used the burlap should soak in water for at least 24 hours. This
will remove all oils in the burlap and make it more absorbent.
SECTION 2
OPERATIONS
050362
Page 39
2.5 - Machine Setup, continued
Summary of Contents for BDF4836B
Page 5: ...050362 Page 5 Table of Contents continued ...
Page 14: ...050362 Page 14 Notes ...
Page 15: ...SECTION 1 SAFETY 050362 Page 15 SECTION 1 SAFETY ...
Page 21: ...SECTION 1 SAFETY 050362 Page 21 PAGE LEFT BLANK INTENTIONALLY ...
Page 22: ...Notes SECTION 1 SAFETY 050362 Page 22 ...
Page 23: ...SECTION 2 OPERATIONS 050362 Page 23 SECTION 2 OPERATIONS ...
Page 40: ...Power Crown Lever Nut A SECTION 2 OPERATIONS 050362 Page 40 2 6 Power Crown Option ...
Page 46: ...Skew Clamp Skew Cylinder SECTION 2 OPERATIONS 050362 Page 46 2 7 Paving Operations continued ...
Page 49: ...SECTION 2 OPERATIONS 050362 Page 49 PAGE LEFT BLANK INTENTIONALLY ...
Page 50: ...SECTION 2 OPERATIONS 050362 Page 50 Notes ...
Page 51: ...SECTION 3 SERVICE 050362 Page 51 SECTION 3 SERVICE ...