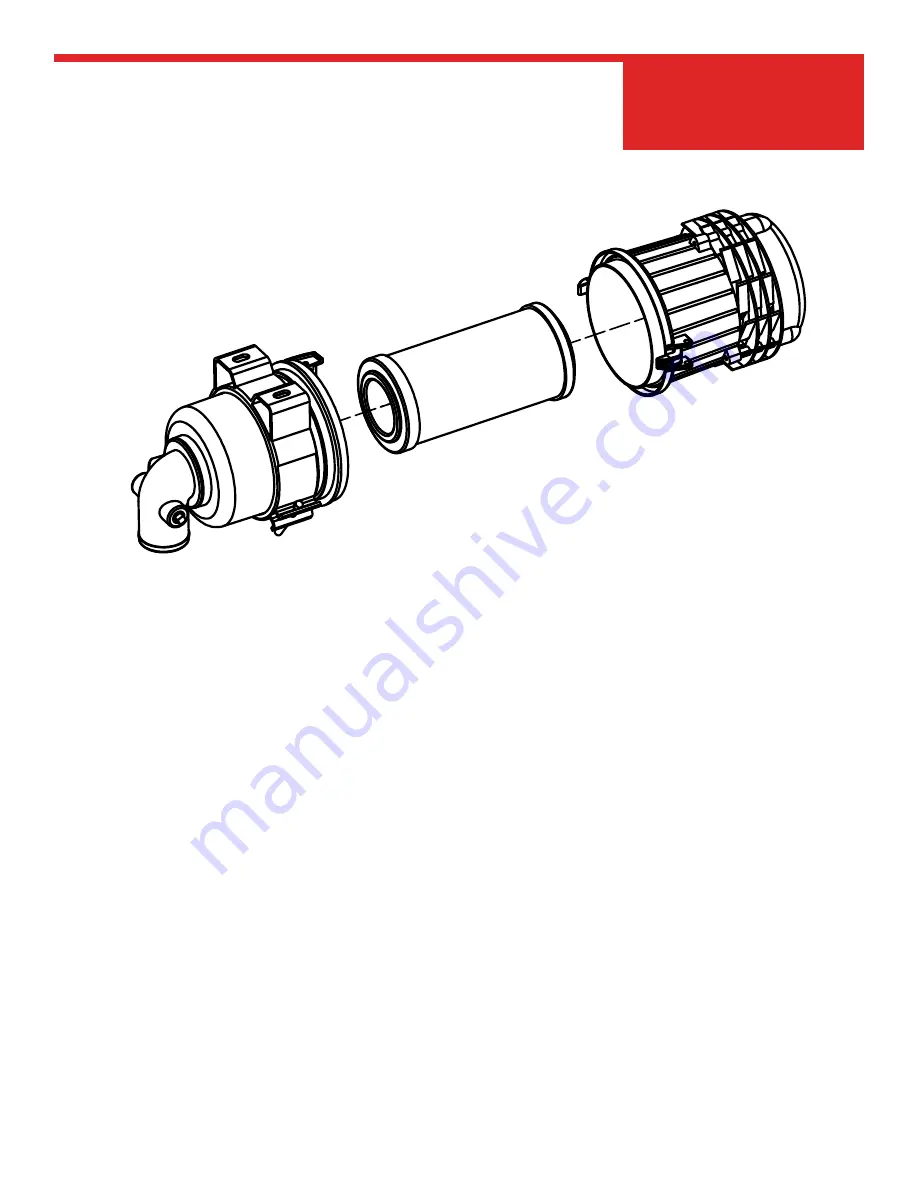
053257 - 01/2014
SECTION 3
SERVICE
Page 3-3
Pre-Cleaner Maintenance Procedure
This machine is equipped with a large capacity, dual element air
fi
lter.
When should you change an air
fi
lter? Many people believe that if a
fi
lter looks dirty it is no longer
working and should be changed. As stated above,
fi
lters need dirt to work properly. The key is knowing
when the
fi
lter is so dirty that to much energy is required by the engine to draw in air that it no longer
functions at it’s designed performance level.
Should you remove a
fi
lter to examine it? NO, never remove a
fi
lter until you are sure it needs to be
replaced. Most dust and dirt that enters your engine comes from over servicing the air
fi
lter. When an
air
fi
lter is removed, it’s seal is broken and dust and dirt that is in the air
fi
lter canister, now has a clear
path into your engine.
Use a Dust Load Indicator (DLI) to tell you when to change the
fi
lter. Dust Load Indicators take the
guess work out of air
fi
lter changes. The DLI is a vacuum sensitive device that “pops” of and shows you
red when it is time to change
fi
lters. If it is not red, don’t open the
fi
lter and allow more dirt to enter into
the engine. If it is red, carefully remove the
fi
lter cover and immediately vacuum the canister to remove
loose dirt. Then slowly remove the
fi
lter being careful not to disturb the dirt that may have become
caked around the seal of the
fi
lter. Again vacuum the canister, and then wipe the sealing area with a
damp cloth to insure no dirt can get into your engine. Replace the
fi
lter immediately with either a new
one or one that has been properly cleaned.
How do you clean an air
fi
lter?
NEVER use high powered air or “bang” it against something hard!
By doing so you can tear the paper or damage the sealing area and thus render the
fi
lter worse than
useless. Paper
fi
lters can be cleaned by carefully vacuuming their surface with a soft brush and thus
remove loose dust.
Air Filter Maintenance
Summary of Contents for MSP470A
Page 1: ...OPERATIONS PARTS MANUAL 053257 01 2014 Riding Trowel...
Page 14: ...053257 01 2014 Page xii Dimensional Speci cations...
Page 16: ...053257 01 2014 INTENTIONALLY BLANK Page xiv...
Page 17: ...053257 01 2014 SECTION 1 SAFETY Page 1 1 Section 1 SAFETY...
Page 18: ...053257 01 2014 SECTION 1 SAFETY Page 1 2 State Regulations Proposition 65 Warning...
Page 19: ...053257 01 2014 SECTION 1 SAFETY Page 1 3 Federal Regulations Respiratory Hazards...
Page 33: ...053257 01 2014 SECTION 2 OPERATIONS Page 2 1 Section 2 OPERATIONS...
Page 41: ...053257 01 2014 SECTION 3 SERVICE Page 3 1 Section 3 SERVICE...
Page 53: ...053257 01 2014 SECTION 3 SERVICE Page 3 13...
Page 59: ...053257 01 2014 SECTION 4 PARTS Page 4 1 Section 4 PARTS...
Page 104: ...053257 01 2014 SECTION 4 PARTS Page 4 46 Electrical Schematic Illustration...
Page 105: ...053257 01 2014 SECTION 4 PARTS Page 4 47 Electrical Schematic Illustration...
Page 106: ...053257 01 2014 SECTION 4 PARTS Page 4 48 Hydraulic Schematic Illustration...
Page 119: ...053257 01 2014 INTENTIONALLY BLANK...