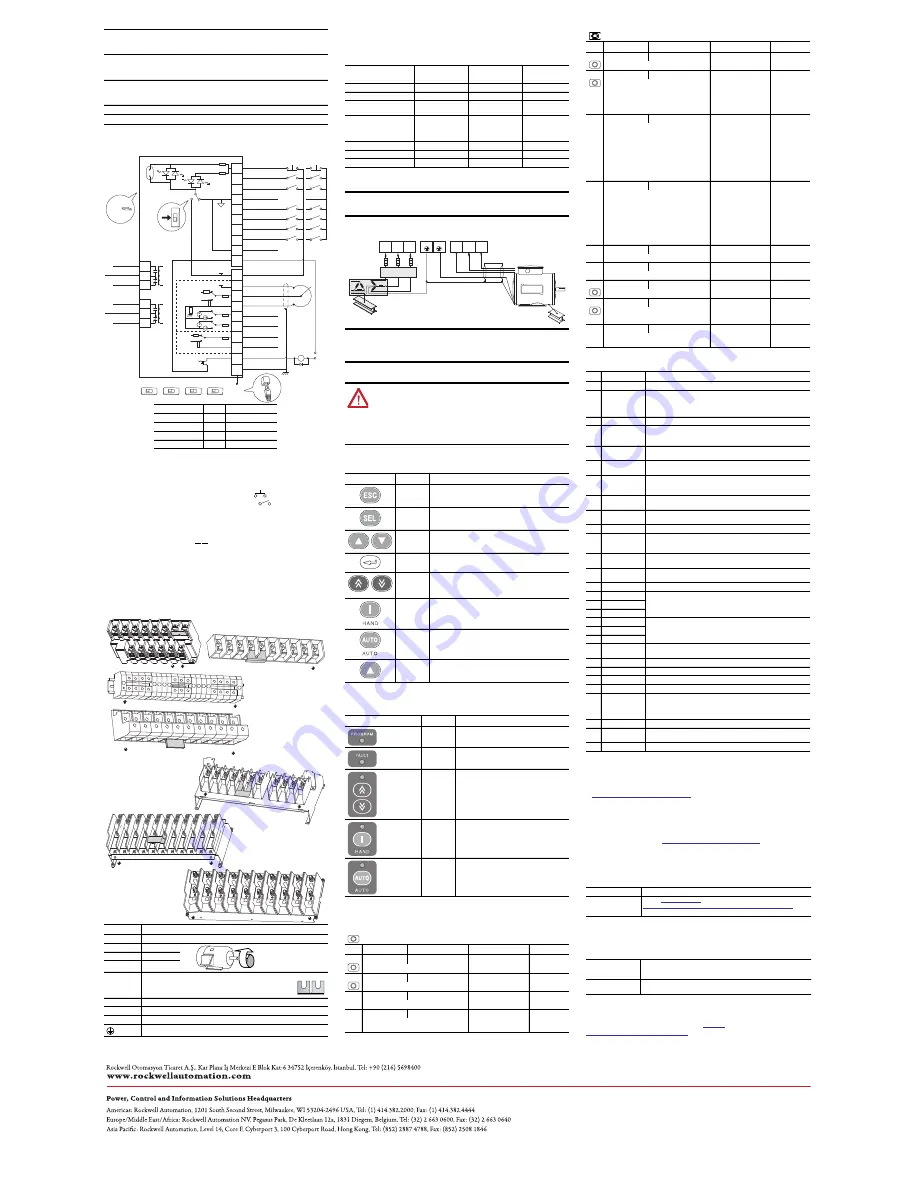
Publication 22C-PC001D-EN-P – January 2017
Supersedes Publication 22C-PC001C-EN-P – October 2014
Copyright © 2017 Rockwell Automation, Inc. All rights reserved.
Allen-Bradley, Rockwell Software, Rockwell Automation , PowerFlex, and TechConnect are trademarks of Rockwell Automation, Inc.
Trademarks not belonging to Rockwell Automation are property of their respective companies.
Control Terminal Block
Power Wiring
Power Terminal Blocks
Power Terminal Block Specifications
General Grounding Requirements
Prepare For Drive Start-Up
Integral Keypad
Operator Keys
LED Status Indicators
Smart Start-Up with Basic Program Group Parameters
The PowerFlex 400 is designed so that start up is simple and efficient. The Program Group contains the most
commonly used parameters.
Fault Codes
To clear a fault, press the Stop key, cycle power or set A100 [Fault Clear] to 1 or 2.
Rockwell Automation Support
Rockwell Automation provides technical information on the Web to assist you in using its products.
At
http://www.rockwellautomation.com/support/
, you can find technical manuals, a knowledge base of
FAQs, technical and application notes, sample code and links to software service packs, and a MySupport
feature that you can customize to make the best use of these tools.
For an additional level of technical phone support for installation, configuration, and troubleshooting, we
offer TechConnect support programs. For more information, contact your local distributor or Rockwell
Automation representative, or visit
http://www.rockwellautomation.com/support/
.
Installation Assistance
If you experience a problem within the first 24 hours of installation, review the information that is contained
in this manual.
You can contact Customer Support for initial help in getting your product up and running.
New Product Satisfaction Return
Rockwell Automation tests all of its products to ensure that they are fully operational when shipped from the
manufacturing facility.
However, if your product is not functioning and needs to be returned, follow these procedures.
Documentation Feedback
Your comments will help us serve your documentation needs better. If you have any suggestions on how to
improve this document, complete this form, publication
RA-DU002
, available at
http://www.rockwellautomation.com/literature/
.
Over Voltage:
200...240V AC Input – Trip occurs @ 405V DC bus voltage (equivalent to 290V AC incoming line)
380...460V AC Input – Trip occurs @ 810V DC bus voltage (equivalent to 575V AC incoming line)
Under Voltage:
200...240V AC Input – Trip occurs @ 210V DC bus voltage (equivalent to 150V AC incoming line)
380...480V AC Input – Trip occurs @ 390V DC bus voltage (equivalent to 275V AC incoming line)
Trip:
Ground fault: Phase-to-ground on drive output
Short circuit: Phase-to-phase on drive output
Control Ride Through: Minimum ride through is 0.5 s - typical value 2 s
Faultless Power Ride Through: 100 ms
Terminal
(1)
Description
R/L1, S/L2, T/L3 3-Phase Input
U/T1
To Motor U/T1
Switch any two motor leads to
change forward direction.
V/T2
To Motor V/T2
=
W/T3
To Motor W/T3
P2, P1
DC Bus Inductor Connection
Drives are shipped with a jumper between Terminals P2 and P1.
Remove this jumper only when a DC Bus Inductor will be connected.
Drive will not power up without a jumper or inductor connected.
DC+, DC-
DC Bus Connection (Frame C Drives)
P2, DC-
DC Bus Connection (Frame D, E and F Drives)
BR+, BR-
Not Used
Safety Ground – PE
04
05
06
07
01
02
0
3
0
8
09
10
12
1
3
14
15
16
17
1
8
19
20
11
Digital Common
Digital Common
Digital Input 1
Digital Input 2
Digital Input
3
Stop/
Function Loss
(1)(4)
Start/Run FWD
(2)
Direction/Run REV
Digital Input 4
Opto Common
R1
R2
R
3
#1 Relay N.O.
#1 Relay Common
#1 Relay N.C.
+24V DC Source
+10V DC Source
Analog Input 1 (AI1)
Analog Common 1
Analog Output 2 (AO2)
Analog Output 1 (AO1)
Analog Input 2 (AI2)
Analog Common 2
(6)
Opto Output
RS4
8
5 Shield
+24V
+10V
R4
R5
R6
#2 Relay N.O.
#2 Relay Common
#2 Relay N.C.
Typical
SNK Wiring
Typical
SRC Wiring
RS4
8
5
(DSI)
Enable
(4)
Jumper
3
0V DC
50 mA
Non-inductive
Common
24V
ENBL
(3)
Pot must be
1...10k ohm
2 W min.
SRC
SNK
SNK
SRC
Earth Referenced
Frames D & E
(5)
0...10V
0...20 mA
0...10V
0...20 mA
0...10V
0...20 mA
1 of 7 Digital Input Circuits
10V 20 mA
AO1
10V 20 mA
AO2
10V 20 mA
AI1
10V 20 mA
AI2
Isolated
Control Wiring Block Diagram
P036 [Start Source] Stop
I/O Terminal 01 Stop
Keypad
Per P037 Coast
3-Wire
Per P037 Per P037
(4)
2-Wire
Per P037 Coast
RS485 Port
Per P037 Coast
(1)
Important:
I/O Terminal 01 is always a coast to stop input except when P036 [Start Source] is set to
option 1 “3-Wire”or 6 “2-W Lvl/Enbl”. In three wire control, I/O Terminal 01 is controlled by
P037 [Stop Mode]. All other stop sources are controlled by P037 [Stop Mode].
Important:
The drive is shipped with a jumper installed between I/O Terminals 01 and 11. Remove this
jumper when using I/O Terminal 01 as a stop or enable input.
(2)
Two wire control show. For three wire control use a momentary input
on I/O Terminal 02 to
command a start. If reverse is enabled by A166, use a maintained input
for I/O Terminal 03 to
change direction.
(3)
When using an opto output with an inductive load such as a relay, install a recovery diode parallel to the
relay as shown, to prevent damage to the output.
(4)
When the ENBL jumper is removed, I/O Terminal 01 will always act as a hardware enable, causing a coast
to stop without software interpretation.
(5)
Most I/O terminals labeled “Common” are not referenced to the safety ground (PE) terminal and are
designed to greatly reduce common mode interference. On Frame D and E drives, Analog Common 1 is
referenced to ground.
(6)
Common for Analog Input 2 (AI2). Electronically isolated from digital I/O and opto output. Not to be used
with Analog Input 1 (AI1), Analog Output 1 (AO1) or Analog Output 2 (AO2). With Analog Input 2, provides
one fully isolated analog input channel.
R/L1
S
/L2 T/L3 P1
P2
DC– U/T1 V/T2 W/T3
R/L1
S
/L2 T/L3 P1
P2 DC– U/T1 V/T2 W/T3
R/L1
S
/L2 T/L3 U/T1 V/T2 W/T3 P2
P1
BR–
BR+
DC+
DC–
R/L1
S
/L2T/L3
P1 P2 DC–
U/T1V/T2W/T3
R/L1
S
/L2 T/L3 P1 P2
DC–
U/T1V/T2W/T3
Frame C
Frame D
Frame F
Frame G
Frame H
Frame E:
480V
37...45 kW
(50...60 HP)
Frame E:
240V 480V
30...37 kW
55...75 kW
(40...50 HP)
(75...100 HP)
R/L1
S
/L2 T/L3 P1
P2 DC– U/T1 V/T2 W/T3
R/L1
S
/L2 T/L3
DC–
DC+
U/T1
V/T2 W/T3
(1)
Important:
Terminal screws may become loose during shipment. Ensure that all terminal screws are tightened
to the recommended torque before applying power to the drive.
Frame
Maximum
Wire Size
(1)
(1)
Maximum/minimum sizes that the terminal block will accept – these are not recommendations. If national or
local codes require sizes outside this range, lugs may be used.
Minimum
Wire Size
(1)
Recommended
Torque
C
8.4 mm
2
(8 AWG)
1.3 mm
2
(16 AWG)
2.9 Nm (26 lb-in.)
D
33.6 mm
2
(2 AWG)
8.4 mm
2
(8 AWG)
5.1 Nm (45 lb-in.)
E
480V
37...45 kW (50...60 HP)
33.6 mm
2
(2 AWG)
3.5 mm
2
(12 AWG)
5.6 Nm (49.5 lb-in.)
E
240V
30...37 kW (40...50 HP)
480V
55...75 kW (75...100 kW)
107.2 mm
2
(4/0 AWG)
53.5 mm
2
(1/0 AWG)
19.5 Nm (173 lb-in.)
F
152.5 mm
2
(300 MCM)
85.0 mm
2
(3/0 AWG)
19.5 Nm (173 lb-in.)
G
152.5 mm
2
(300 MCM)
107.2 mm
2
(4/0 AWG)
29.4 Nm (260 lb-in.)
H
253.0 mm
2
(500 MCM)
152.0 mm
2
(300 MCM)
40.0 Nm (354 lb-in.)
IMPORTANT
Frame C, D, F, G and H drives utilize a finger guard over the power wiring
terminals. Replace the finger guard when wiring is complete.
IMPORTANT
The MOV to ground jumper must be removed if the drive is installed on an
ungrounded or resistive grounded distribution system.
Tighten screw after jumper removal.
ATTENTION:
Power must be applied to the drive to perform the following start-up procedures.
Some of the voltages present are at incoming line potential. To avoid electric shock hazard or
damage to equipment, only qualified service personnel should perform the following
procedure. Thoroughly read and understand the procedure before beginning. If an event does
not occur while performing this procedure,
Do Not Proceed. Remove All Power
including
user supplied control voltages. User supplied voltages may exist even when main AC power is
not applied to the drive. Correct the malfunction before continuing.
Key
Name
Description
Escape
Back one step in programming menu.
Cancel a change to a parameter value and exit Program Mode.
Select
Advance one step in programming menu.
Select a digit when viewing parameter value.
Up Arrow
Down Arrow
Scroll through groups and parameters.
Increase/decrease the value of a flashing digit.
Enter
Advance one step in programming menu.
Save a change to a parameter value.
Digital Speed
Increment and
Decrement
Arrows
Used to control speed of drive. Default is active.
Control is activated by parameter P038 [Speed Reference] or
P042 [Auto Mode].
Run/Start &
Hand
(1)
(1)
Important:
Certain digital input settings can override drive operation. Refer to the PowerFlex 400 User Manual
for details.
Used to start the drive. Default is Hand mode as controlled by
parameter P042 [Auto Mode].
Control is activated by parameter P036 [Start Source] or P042
[Auto Mode].
Auto
(1)
Used to select Auto control mode.
Controlled by parameter P042 [Auto Mode].
Stop/Off
Used to stop the drive or clear a fault.
This key is always active.
Controlled by parameter P037 [Stop Mode].
LED
LED State
Description
Program status
Steady red
Indicates parameter value can be changed.
Selected digit will flash.
Fault status
Flashing red
Indicates that the drive is faulted.
Speed status
Steady green
Indicates that the digital speed control keys are
enabled.
Hand status
Steady green
Indicates that the Run/Start key is enabled.
Auto status
Steady yellow Indicates that the drive is in Auto mode.
= Stop drive before changing this parameter.
No.
Parameter
Min/Max
Display/Options
Default
P031
[Motor NP Volts]
20/Drive Rated Volts
1V AC
Based on
Drive Rating
Set to the motor nameplate rated volts.
P032
[Motor NP Hertz]
15/320 Hz
1 Hz
60 Hz
Set to the motor nameplate rated frequency.
P033
[Motor OL Current]
0.0/(Drive Rated Amps × 2) 0.1 A
Based on
Drive Rating
Set to the maximum allowable motor current.
P034
[Minimum Freq]
0.0/320.0 Hz
0.1 Hz
0.0 Hz
Sets the lowest frequency the drive will output
continuously.
PE
L1
R
L2
S
L3
T
T1
U
T2
V
T3
W
PE
Required
Input Fusing
Required Branch
Circuit Disconnect
P035
[Maximum Freq]
0.0/320.0 Hz
0.1 Hz
60.0 Hz
Sets the highest frequency the drive will output.
P036
[Start Source]
0/6
0 = “Keypad”
1 = “3-Wire”
2 = “2-Wire”
3 = “2-W Lvl Sens”
4 = “2-W Hi Speed”
5 = “Comm Port”
6 = “2-Wire Lvl/Enbl”
3
Sets the control scheme used to start the drive
when in Auto/Remote mode.
P037
[Stop Mode]
0/7
0 = “Ramp, CF”
(1)
1 = “Coast, CF”
(1)
2 = “DC Brake, CF”
(1)
3 = “DCBrkAuto,CF”
(1)
4 = “Ramp”
5 = “Coast”
6 = “DC Brake”
7 = “DC BrakeAuto”
(1)
Stop input also clears
active fault.
0
Active stop mode for all stop sources [e.g.
keypad, run forward (I/O Terminal 02), run
reverse (I/O Terminal 03), RS485 port] except as
noted below.
Important:
I/O Terminal 01 is always a coast to
stop input except when P036 [Start Source] is set
for “3-Wire” control. When in three wire control,
I/O Terminal 01 is controlled by P037 [Stop
Mode].
P038
[Speed Reference]
0/5
0 = “Drive Keypad”
1 = “InternalFreq”
2 = “Analog In 1”
3 = “Analog In 2”
4 = “Preset Freq”
5 = “Comm Port”
2
Sets the source of the speed reference to the
drive.
Important:
When T051...T054 [Digital Inx Sel] is
set to option 1, 2, 3, 4, 5, 8, 14, 15, 16 or 17 and
the digital input is active, or if A152 [PID Ref Sel]
is not set to option 0, the speed reference
commanded by this parameter will be overriden.
Refer to Chapter 1 of the PowerFlex 400 User
Manual for details.
P039
[Accel Time 1]
0.00/600.00 s
0.01 s
20.00 s
Sets the rate of accel for all speed increases.
P040
[Decel Time 1]
0.0/600.00 s
0.01 s
20.00 s
Sets the rate of decel for all speed decreases.
P041
[Reset To Defalts]
0/1
0 = “Ready/Idle”
1 = “Factory Rset”
0
Resets all parameter values to factory defaults.
P042
[Auto Mode]
0/3
0 = “No Function”
1 = “Hnd-Off-Auto”
2 = “Local/Remote”
3 = “Auto/Manual”
1
Determines the operation of the “Auto” key on
the integral keypad.
P043
[Motor OL Ret]
0/1
0 = “Disabled”
1 = “Enabled”
0
Enables/disables the Motor Overload Retention
function.
No. Fault
Description
F2
Auxiliary Input
(1)
(1)
Auto-Reset/Run type fault. Configure with parameters A092 and A093.
Check remote wiring.
F3
Power Loss
FRN 5.03 and earlier only: The DC bus voltage fell below undervoltage level
within 200 ms of a start command, DC bus ripple voltage is excessive, or an
input phase loss has been detected. Monitor the incoming AC line for low
voltage or line power interruption.
F4
UnderVoltage
(1)
Monitor the incoming AC line for low voltage or line power interruption.
F5
OverVoltage
(1)
Monitor the AC line for high line voltage or transient conditions. Bus
overvoltage can also be caused by motor regeneration. Extend the decel time
or install a dynamic brake chopper.
F6
Motor Stalled
(1)
Increase [Accel Time x] or reduce load so drive output current does not
exceed the current set by parameter A089 [Current Limit].
F7
Motor Overload
(1)
An excessive motor load exists. Reduce load so drive output current does not
exceed the current set by parameter P033 [Motor OL Current].
F8
Heatsink OvrTmp
(1)
Check for blocked or dirty heat sink fins. Verify that ambient temperature has
not exceeded 40 °C (104 °F) for IP 30/NEMA 1/UL Type 1 installations or
50 °C (122 ° F) for Open type installations. Check fan.
F12
HW OverCurrent
Check programming. Check for excess load, improper DC boost setting, DC
brake volts set too high or other causes of excess current.
F13
Ground Fault
Check the motor and external wiring to the drive output terminals for a
grounded condition.
F15
Load Loss
Check for load loss (i.e., a broken belt).
F17
Input Phase Loss
FRN 6.xx and later. Check incoming power for a missing phase or blown fuse.
If drive is used intentionally with single phase input, apply output derating to
35% actual drive rating.
F29
Analog Input
Loss
(1)
An analog input is configured to fault on signal loss. A signal loss has
occurred.
F32
Fan Fdbck Loss
FRN 6.xx and later. Make sure cooling fans are clear of debris and spinning
freely. Replace fan if necessary.
F33
Auto Rstrt Tries
Correct the cause of the fault and manually clear.
F38
Phase U to Gnd
Check the wiring between the drive and motor.
Check motor for grounded phase.
Replace drive if fault cannot be cleared.
F39
Phase V to Gnd
F40
Phase W to Gnd
F41
Phase UV Short
Check the motor and drive output terminal wiring for a shorted condition.
Replace drive if fault cannot be cleared.
F42
Phase UW Short
F43
Phase VW Short
F48
Params Defaulted
The drive was commanded to write default values to EEPROM. Clear the fault
or cycle power to the drive. Program the drive parameters as needed.
F63
SW OverCurrent
(1)
Check load requirements and A098 [SW Current Trip] setting.
F64
Drive Overload
Reduce load or extend Accel Time.
F70
Power Unit
Cycle power. Replace drive if fault cannot be cleared.
F71
Net Loss
The communication network has faulted.
F81
Comm Loss
If adapter was not intentionally disconnected, check wiring to the port.
Replace wiring, port expander, adapters or complete drive as required. Check
connection. An adapter was intentionally disconnected. Turn off using C105
[Comm Loss Action].
F94
Function Loss
Close input to terminal 01 and re-start the drive.
F100 Parameter
Checksum
Restore factory defaults.
F122 I/O Board Fail
Cycle power. Replace drive if fault cannot be cleared.
United States or Canada 1.440.646.3434
Outside United States
or Canada
Use the
Worldwide Locator
at
http://www.rockwellautomation.com/support/americas/phone_en.html
, or
contact your local Rockwell Automation representative.
United States
Contact your distributor. You must provide a Customer Support case number (call
the phone number above to obtain one) to your distributor to complete the
return process.
Outside United States
Please contact your local Rockwell Automation representative for the return
procedure.
= Stop drive before changing this parameter.
No.
Parameter
Min/Max
Display/Options
Default
All manuals and user guides at all-guides.com