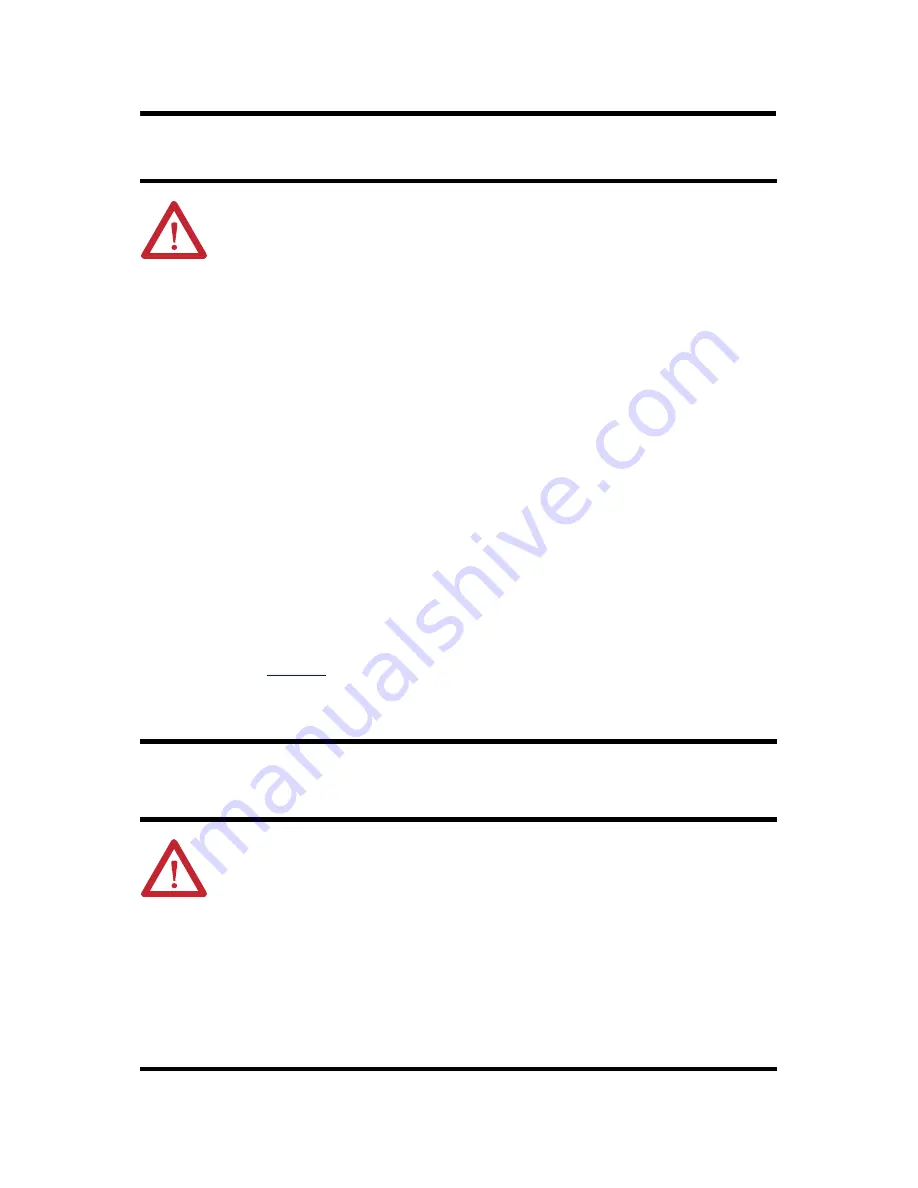
POINT I/O 2 and 4 Relay Output Modules
3
Publication 1734-IN055H-EN-E - August 2016
Environment and Enclosure
Preventing Electrostatic Discharge
ATTENTION:
This equipment is intended for use in a Pollution Degree 2
industrial environment, in overvoltage Category II applications (as defined in IEC
60664-1), at altitudes up to 2000 m (6562 ft) without derating.
This equipment is considered Group 1, Class A industrial equipment according
to IEC/CISPR 11. Without appropriate precautions, there may be difficulties
with electromagnetic compatibility in residential and other environments due to
conducted and radiated disturbances.
This equipment is supplied as open-type equipment. It must be mounted within
an enclosure that is suitably designed for those specific environmental
conditions that will be present and appropriately designed to prevent personal
injury resulting from accessibility to live parts. The enclosure must have
suitable flame-retardant properties to prevent or minimize the spread of flame,
complying with a flame spread rating of 5VA or be approved for the application
if nonmetallic. The interior of the enclosure must be accessible only by the use
of a tool. Subsequent sections of this publication may contain additional
information regarding specific enclosure type ratings that are required to
comply with certain product safety certifications.
In addition to this publication, see the following:
•
Industrial Automation Wiring and Grounding Guidelines, publication
1770-4.1
, for additional installation requirements.
•
NEMA Standard 250 and IEC 60529, as applicable, for explanations of the
degrees of protection provided by enclosures.
ATTENTION:
This equipment is sensitive to electrostatic discharge, which can
cause internal damage and affect normal operation. Follow these guidelines
when you handle this equipment:
•
Touch a grounded object to discharge potential static.
•
Wear an approved grounding wrist strap.
•
Do not touch connectors or pins on component boards.
•
Do not touch circuit components inside the equipment.
•
Use a static-safe workstation, if available.
•
Store the equipment in appropriate static-safe packaging when not in use.