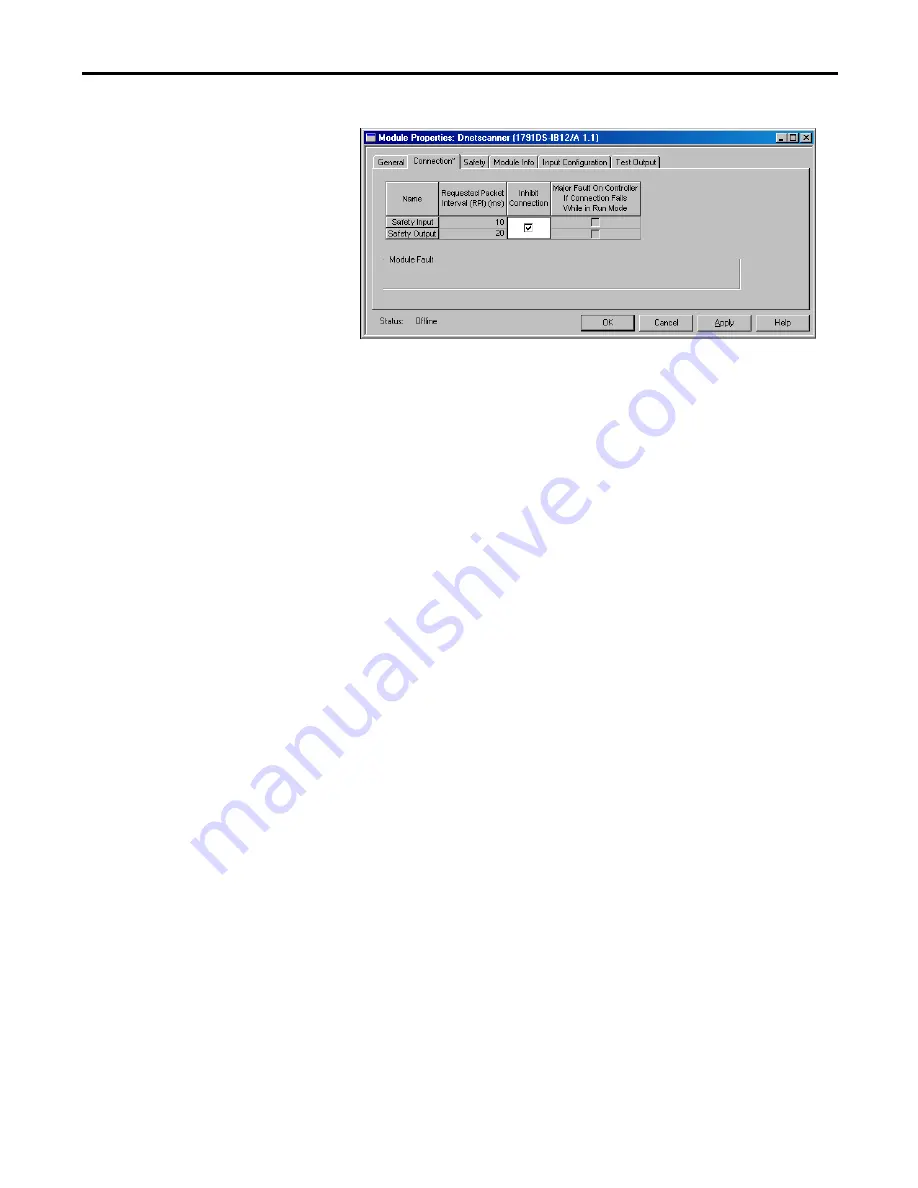
Rockwell Automation Publication 1756-RM093J-EN-P - April 2018
61
Safety Application Development
Chapter 6
3.
Check Inhibit Connection and click Apply.
The module is inhibited whenever the checkbox is checked. If a
communication module is inhibited, all downstream modules are also
inhibited.
Editing Your Safety
Application
The following rules apply to changing your safety application in RSLogix 5000
software:
•
Only authorized, specially-trained personnel can make program edits.
These personnel should use all supervisory methods available, for example,
using the controller keyswitch and software password protections.
•
When authorized, specially-trained personnel make program edits, they
assume the central safety responsibility while the changes are in progress.
These personnel must also maintain safe application operation.
•
When editing online, you must use an alternate protection mechanism to
maintain the safety of the system.
•
You must sufficiently document all program edits, including:
–
authorization.
–
impact analysis.
–
execution.
–
test information.
–
revision information.
•
If online edits exist only in the standard routines, those edits are not
required to be validated before returning to normal operation.
•
You must make sure that changes to the standard routine, with respect to
timing and tag mapping, are acceptable to your safety application.
•
You
can
edit the logic portion of your program while offline or online, as
described in the following sections.