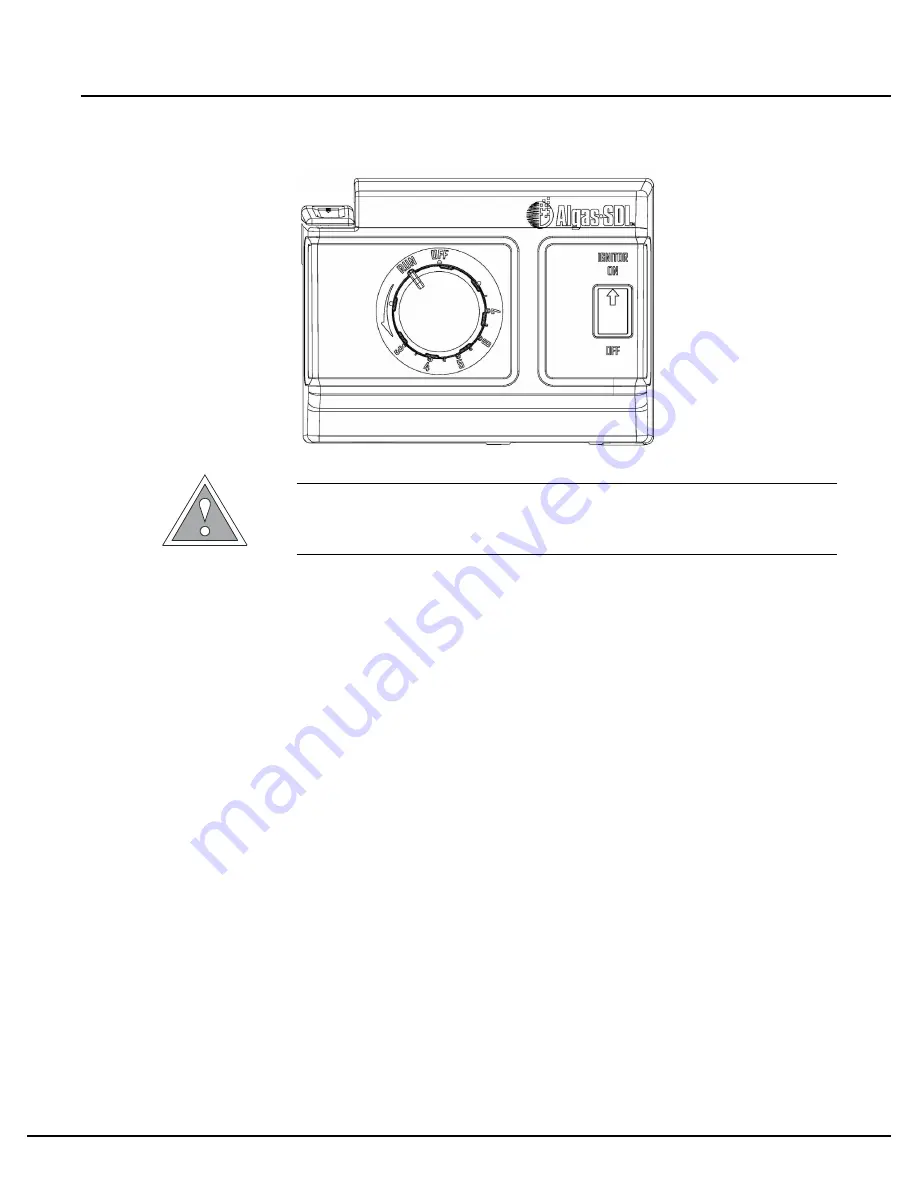
Operation
Algas-SDI Operation and Maintenance Manual – P/N – 54000
3-13
Figure 6
–
Pilot button pressed down and ignitor switch ON
WARNING
If pilot light goes off after releasing the pilot button, turn control dial
to "
OFF"
, wait 5 minutes and repeat step 4.
6. Turn temperature control dial counter clockwise until burner(s) cycle on.
7. Allow burner(s) to heat the vaporizer until they cycle off.
8. Make sure all the valves on consuming equipment are closed and slowly
open the valve in the vapor distribution line. Open all consuming
equipment valves.
Direct Fired Vaporizer setpoint adjustment
On initial startup, set the temperature control dial to a setpoint between 5 and
7. If there is a drop in downstream pressure, it means that the capacity
control valve is beginning to close due to the actual heat input not being able
to satisfy system capacity. Rotate the dial to a higher setpoint to increase
heat input until pressure at the outlet has stabilized.
Summary of Contents for 160H
Page 4: ...This page left intentionally blank...
Page 6: ...This page left intentionally blank...
Page 9: ...This page left intentionally blank...
Page 42: ...Algas SDI Operation and Maintenance Manual P N 54000 5 32 APPENDIX A TECHNICAL INFORMATION...
Page 43: ...Figure 11 160H Vaporizer Replacement Parts 3 11 13 5 6 1 2 7 4 14 10 12 8 9...
Page 57: ......