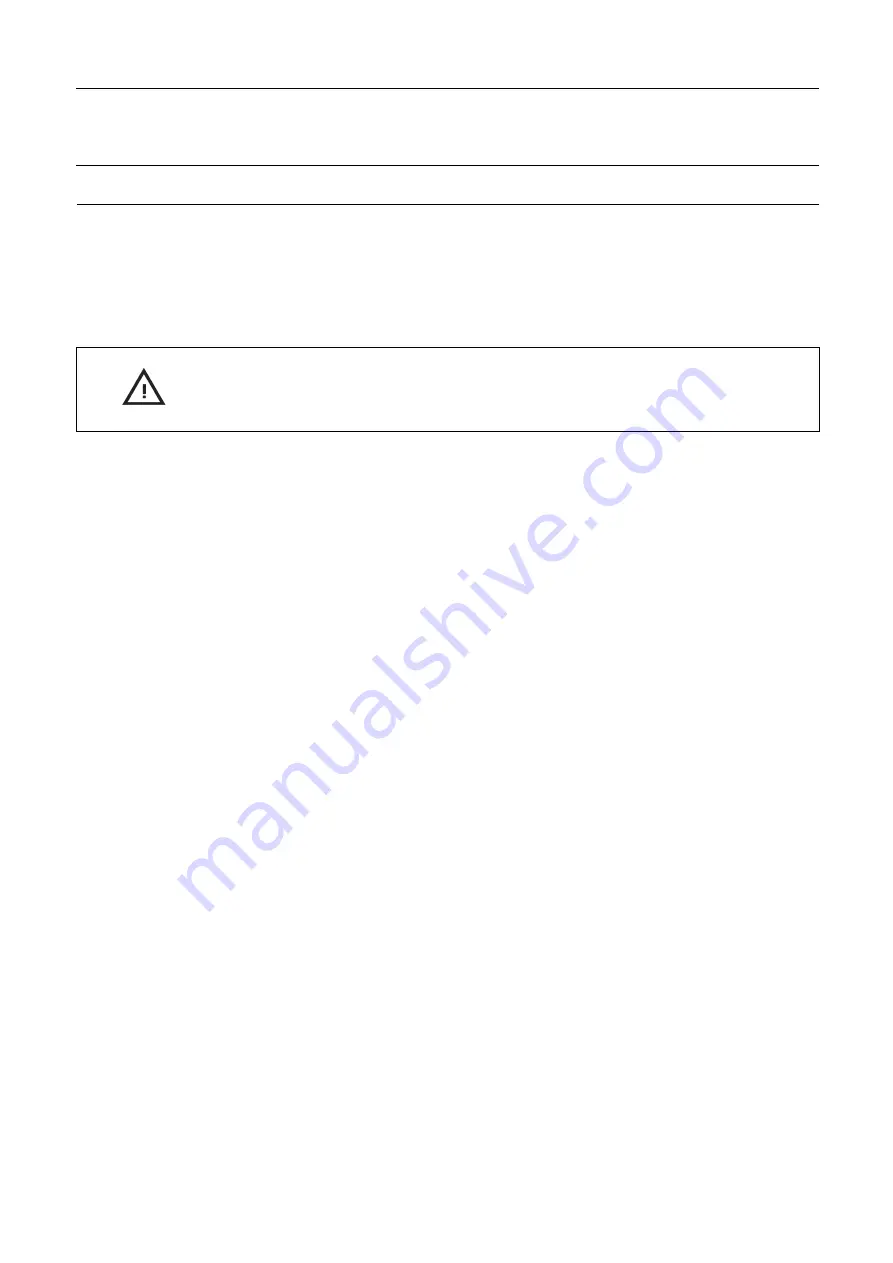
4 Installation
TZ-67
4.3
General safety and installation instructions
The tank cleaning machine should be installed in a vertical position (upright or upside down). It is recommended to install a filter
with mesh size of max. 3 mm in the supply line in order to avoid large particles to clog inside the machine. Before connecting the
machine into the system, all supply lines and valves should be flushed to remove foreign matter.
NOTE
The machine shall be installed in accordance with national regulations for safety and other relevant regulations and standards. In
EU-countries the complete system must fulfil the EU-machine Directive and depending of application, the EU-Pressure Equipment
Directive, the EU-ATEX/IECEx Directive and other relevant Directives and shall be CE-marked before it is set into operation.
Warning:
Precautions shall be made to prevent starting of the cleaning operation, while personnel are inside the
tank or otherwise can be hit by jets from the nozzles.
For information on use in potential explosive atmospheres see paragraph 4.4 Specific conditions for safe use in accordance with
ATEX/IECEx certification page 13.
To protect your tank coating it is recommended to mount bumpers on the tank cleaning machine.
The machine as delivered has been tested at the factory before shipping. For transportation reasons, the nozzles have been
screwed off after the test. In order to secure the nozzles against falling off due to vibrations and other external strains it is
important that the nozzles are tightened properly after mounting. If not, the nozzles may be blown off during tank cleaning and
cause severe damage on tank, valves and pump. This is especially important if machines are fixed installed in tanks and vessels
within the transportation sector in trucks, railcars and onboard ships.
Normally, it is sufficient to tighten the nozzles with the specified torque. However, depending on the application and local
policies an extra securing may be preferred.
Subject to the intended use, environment and any inhouse user requirements or policies, a liquid threadlocker such as Loctite
No. 243 or equivalent could be used. Other methods could be acceptable and subject to customer preference. For detailed
instruction on pre-cleaning and application of the product carefully follow the instruction on the used locking system.
11