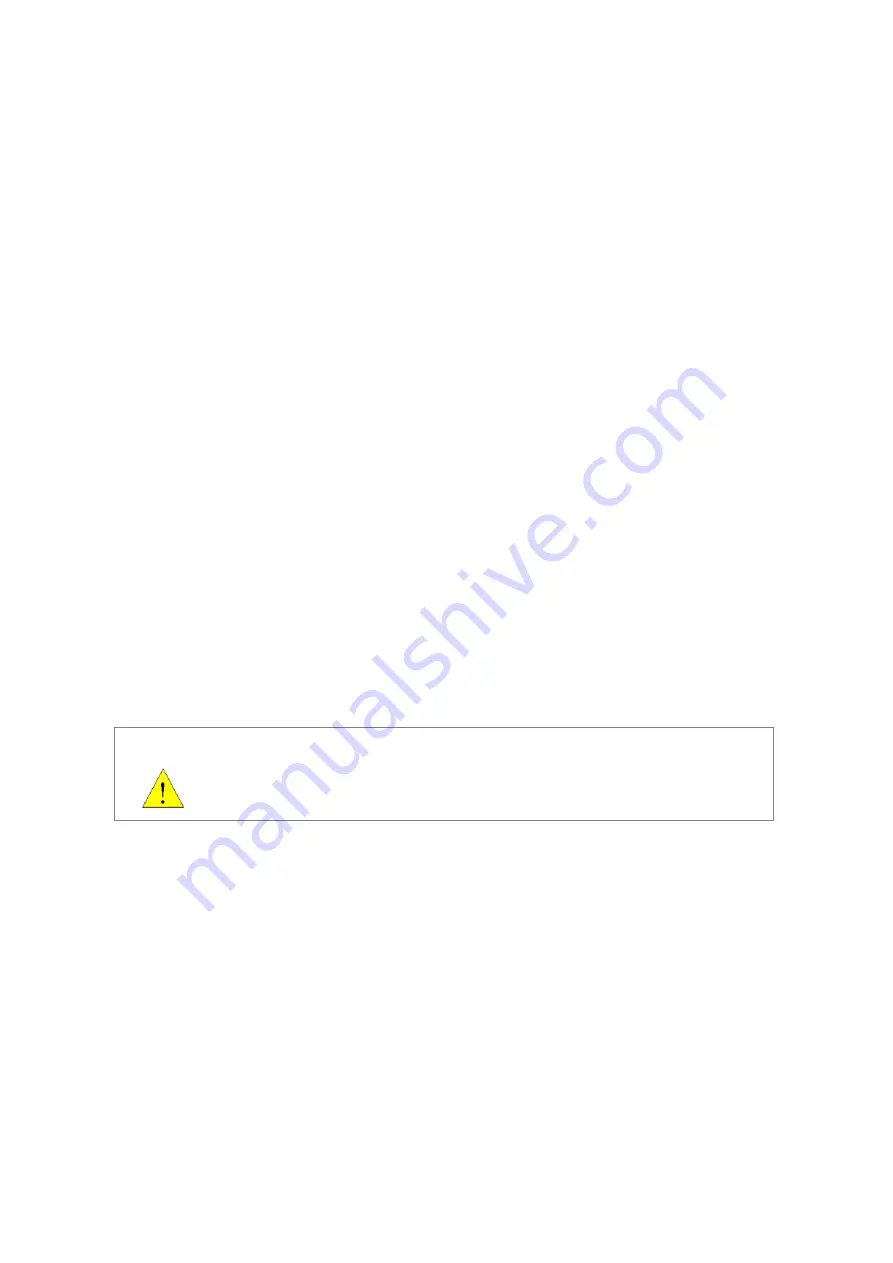
Page 40
Instruction Manual, Gunclean Toftejorg T-82
Standard machines and machines delivered with ATEX certification
in accordance with Directive 94/9/EC
IM-TE91A052-EN4
Maintenance and repair
(continued)
Replacement of Main Collars
Although normally exposed to very limited wear, it is possible to replace Main collars (pos. 36 and 34)
in Body. The procedure to do this is described below.
Main collar upper
1.
Place Body (pos. 28) in a vice in upright position. Do not clamp on machined faces. Insert Tool
(see page 43) into Main collar upper (pos. 36). Unscrew Main collar.
2.
Carefully clean thread and recess in Body. Do not damage special thread in Body. Recess must
be absolutely clean.
3.
Make sure that new Main collar is clean and free from impurities.
4.
Screw in new Main collar. Attention should be given to make sure that thread is in correct
engagement before screwing in Main collar.
5.
Tighten Main collar fully home, and tighten up.
6.
Check that main collar is fully home: Install Stem, Ball retainer with balls and Gear wheel (see
page 32). Check that there is sufficient axial clearance to allow for free rotation of Stem.
Main Collar Lower
Place Body in a vice in upside down position, and repeat procedure described above.
Warning
:
Thread on Main collar lower is left-handed.