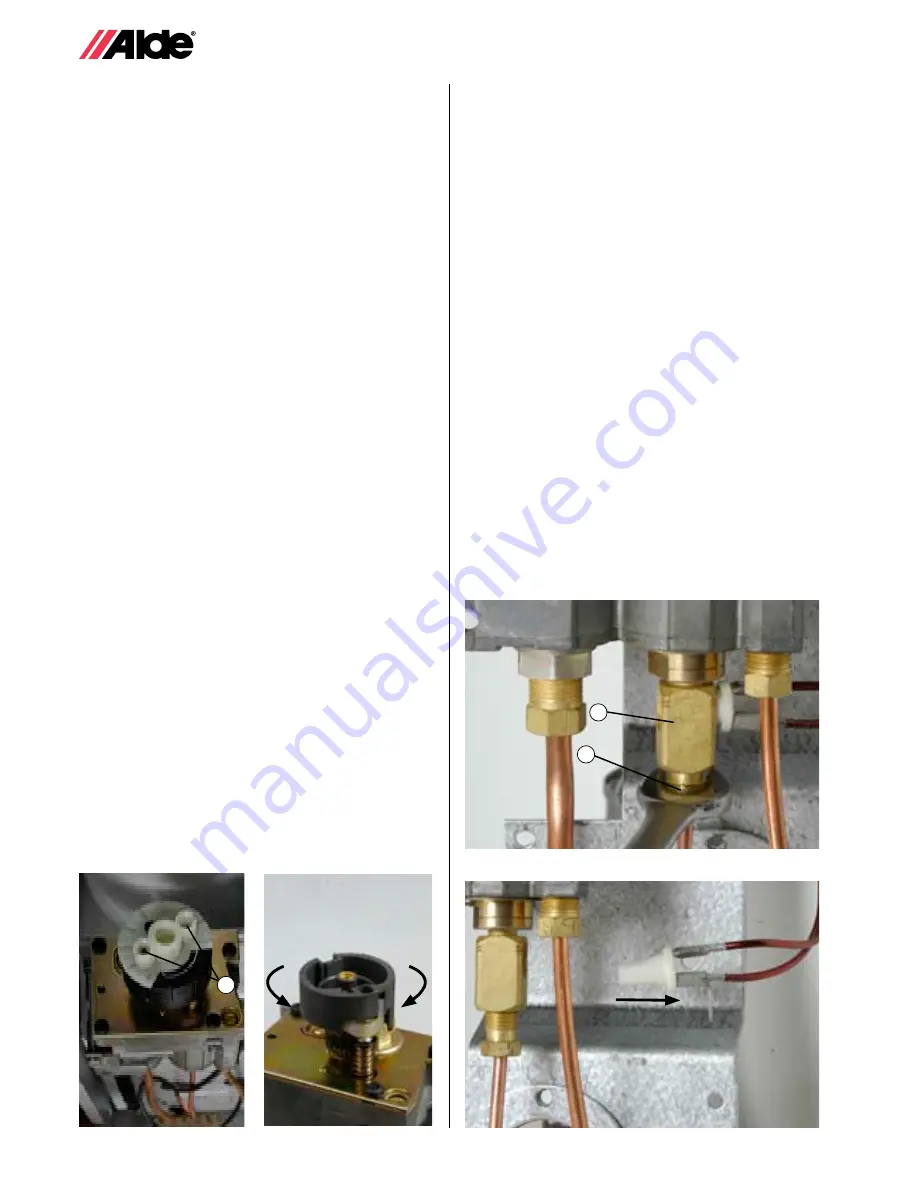
1
1
1
1
Fig 17
Fig 18
+
_
A
Fig 0
Fig 19
A
B
: ADjuStIng thE BOIlER tEmPERAtuRE
1.
Remove the hatch on the control panel by opening it
straight out and carefully bending it in the middle so that
the pegs are released (se Chapter 6:12).
.
Remove the lower front plate (see fig 12).
.
Switch off the main power switch, set the thermostat
knob in position 2, so that the hole with the figure 5
on the automatic unit knob is straight ahead. Unfasten
the screws (fig 17 A) on both sides of the plastic con
-
ductor on the rod. Push the rod and knob to the side.
Remove the white plastic plug, press down the nozzle
and remove the screw with a 7 mm spanner, (with serial
numbers from 21425, a special tool is required for remo
-
ving the screw.) Remove knob and spring (see fig 17).
.
temperature adjustment:
Note the scale on the edge
of the plastic wheel (corresponds to the scale on the
knob) and the index on the cover. Lift the plastic wheel
approximately 10 mm (see fig 18). Turn anti-clockwise
to reduce the temperature and clockwise to increase it.
Carefully push the plastic wheel down so that the teeth
engage, every tooth movement is equivalent to approx.
3°C change in temperature.
.
Fit the spring, knob and screw. Turn the knob to the stop
position, switch on the main switch/insert fuse. Start and
test-run the boiler at max temp (knob in position 7) with
the circulation pump switched off. Check that the boiler
switches off (main burner goes out) at the correctly set
system temperature. If necessary, make further adjust
-
ments.
Basic setting of temperature:
With the sensor in a water
bath, temperature 70°C, turn the thermostat knob from
position 7 towards 1, switching, ”ticking” occurs between
positions 6½ - 4½. On burner unit with serial numbers >
28798, the water bath must be at 65°C.
.
Press in the plastic plug, fit the rod with the plastic adap
-
ted, (NOTE! The figure 5 must be visible in the hole).
Turn to the stop position, check that the spark shuts off
and that the lamp stops flashing.
7.
Fit the lower front plate (see fig 12). Install and close the
hatch.
6:3 RePLACING tHe oveRHeAtING
PROtECtIOn
1.
Remove the lower front plate (see fig 12).
.
Unfasten the springs (fig 13 A) which hold the sensor (fig
13 B) and overheating protection (fig 13 C) to the boiler
casing.
.
Unwind the sensor from the overheating protection.
.
Slacken the nuts on the thermo-element (fig 19 A) a
couple of turns in the joint nipple (fig 19 B) below the
automatic unit and then pull the overheating protection
straight out of the joint nipple (see fig 20). Check that
the joint metal is free from oxidation, if necessary clean
or replace it.
.
Fit the new overheating protection into the joint nipple.
Tighten the nuts from the thermo element, but not too
much. Check that the cables for the overheating protec
-
tion are not lying against the gas pipe.
.
Wind the sensor wire round the new overheating protec-
tion and attach the sensor with spring in the recess in
the boiler casing. Check that there is heat - conducting
paste on the sensor.
7.
Tilt the overheating protection at the top and push it
down into the holder. Attach it with the spring.
8.
Start the boiler in accordance with instructions. Check
that the boiler continues to burn when the thermostat
knob is released. Fit the lower front plate (see fig 12)
Summary of Contents for Comfort 2923
Page 1: ...SE GB Servicemanual Comfort 2923 2928 ...
Page 27: ...27 27 ...