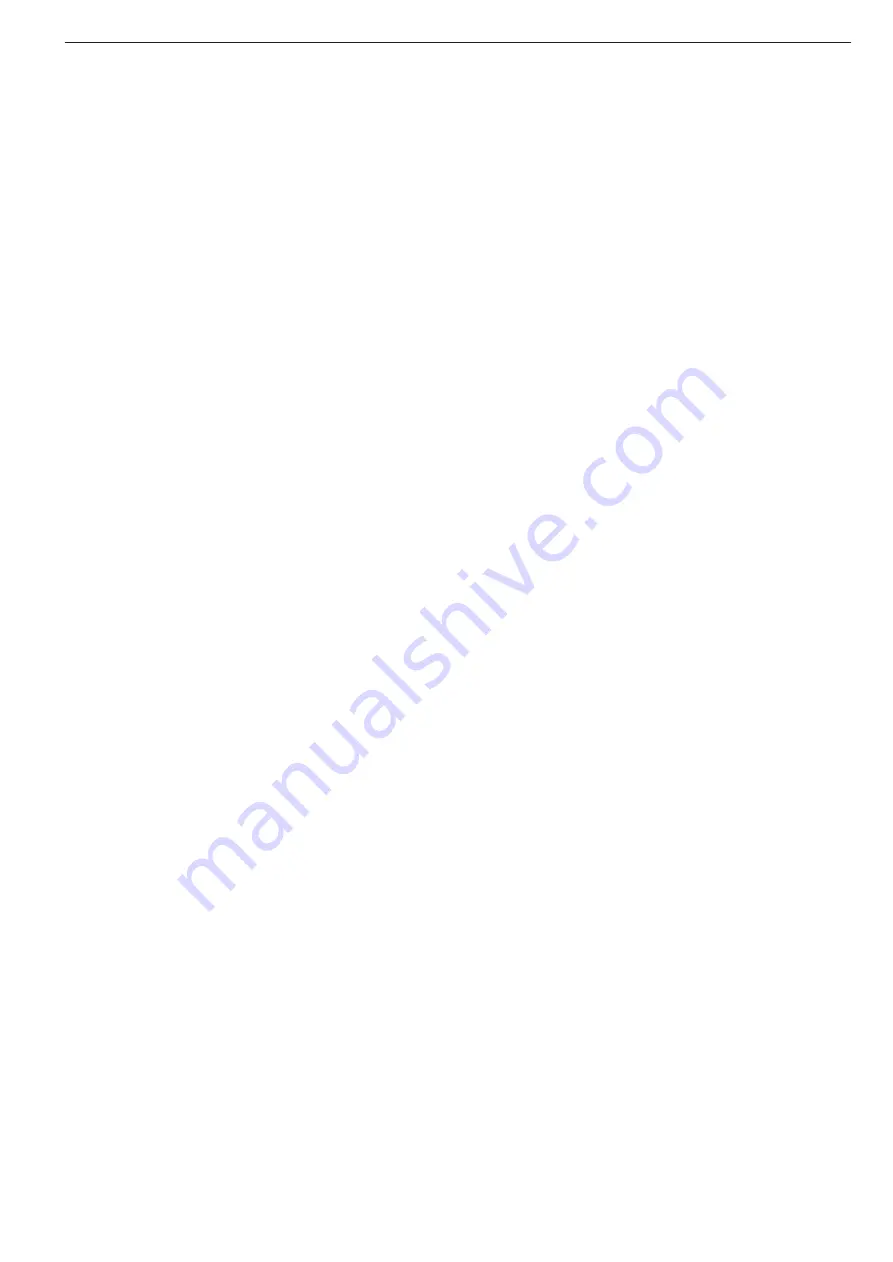
eng
eng
drilling crown may overheat and suffer damage. There is also a dan-
ger of the compressed drilling dust in the drilling gap causing the dia-
mond core drilling crown to become blocked. If you need to work with-
out the dust-extraction system when handling fine-pored materials,
pull the diamond core drilling crown out at regular intervals and push it
back in with a slight turn, so that the drilling dust is expelled from the
drilling gap.
3.2. Manually-controlled wet drilling
Important:
Never carry out manually-controlled drilling without first
fitting the holder-up. DANGER OF ACCIDENTS!
Screw the selected diamond core drilling crown onto the drive spindle
(11) of the drive unit, and lightly hand-tighten. There is no need to
tighten it with a wrench. Connect the water supply (see 2.5.). Using
the tapping tool (see 2.4.1.). Secure the drive unit to the motor handle
(20) and holder-up (12), and locate the tapping tool at the centre of
the desired core-drilling point. Activate the drive unit at the switch
(21).
Important:
Avoid accidents: NEVER block the drive unit switch during
manually-controlled boring! If the drive unit is knocked out of your
hands as a result of a blocked diamond core drilling crown, a blocked
switch can no longer be released. The drive unit will then run out of
control, and the unit must be shut down by unplugging it from the
mains supply.
To make a tapping hole, drill until the diamond core drilling crown has
bored to a depth of about 5 mm. Remove the tapping tool, using a
SW 19 wrench if required. Adjust the pressure in the water supply
system (15) to a point where there is a moderate, but constant, flow
for water from the bore hole. Insufficient water pressure (where the
waste material flows out of the bore hole as thick sludge rather than
liquid) is as bad for the working efficiency and service life of the
diamond core drilling crown as is excessive water pressure, which
causes completely clear water to flow out. Continue boring until the
core-drilling operation is complete. PREVENT ACCIDENTS: The
drive unit should be held firmly throughout in order to prevent torque-
related jarring. Check to ensure correct stability. Carry out larger core-
drilling operations with the drill upright. Ensure that no water is
allowed to get into the drive unit motor during operation. DANGER OF
FATAL ACCIDENT!
3.3. Ways of securing the drill upright
You are recommended to secure the drill upright without the drive unit
and diamond core drilling crown. The drill upright becomes top-heavy
when the drive unit is attached. This makes the task of securing it
more difficult.
3.3.1. Securing with plugs in concrete with knock-in anchor (Fig. 5)
For core-drilling operations in concrete, the drill upright should be
secured with a knock-in anchor (steel plug). Proceed as follows:
Mark the plug hole at a distance of about 220 mm to the centre of the
core-drilling hole. Make the Ø 15 mm plug hole, with a drilling depth of
about 55 mm. Clean the bore hole, hit the knock-in anchor (23) in with
a hammer and spread with the flattener (24). Use only knock-in an-
chors of approved type (art. no. 079005). Screw the knurled threaded
rod (25) into the knock-in anchor and tighten it by holding a tool such
as a screwdriver in the transverse hole of the knurled threaded rod.
Turn the four adjustment screws (5) on the drill upright until they no
longer protrude from the sole plate. Position the drill upright with slot
(7) on the knurled threaded rod, while observing the desired position
of the core-drilling operation. Fit the washer (26) to the knurled threa-
ded rod and use an SW 19 wrench to secure the fast-tightening nut
(27). Turn all four adjustment screws (5) with the SW 19 wrench to
compensate for irregularities in the ground surface. Take care to
ensure that the locknuts do not prevent movement of the adjustment
screws. Tighten the locknuts as required.
3.3.2. Securing with plugs in masonry, with expansion anchor
(anchor sleeve, fig. 6)
For core-drilling operations in masonry, the drill upright should be
secured with an expansion anchor (anchor sleeve). Proceed as
follows:
Mark the plug hole at a distance of about 220 mm to the centre of the
core-drilling hole. Make the Ø 20 mm plug hole, with a drilling depth of
about 85 mm. Clean the bore hole, and push the expansion anchor
(28) with knurled threaded rod (25) into the hole. Screw the knurled
threaded rod (25) fully home and tighten it by holding a tool such as a
screwdriver in the transverse hole of the rod. Turn the four adjustment
screws (5) on the drill upright until they no longer protrude from the
sole plate. Position the drill upright with slot (7) on the knurled threa-
ded rod, while observing the desired position of the core-drilling ope-
ration. Fit the washer (26) to the knurled threaded rod and use an SW
19 wrench to secure the fast-tightening nut (27). Turn all four adjust-
ment screws (5) with the SW 19 wrench to compensate for irregulari-
ties in the ground surface. Take care to ensure that the locknuts do
not prevent movement of the adjustment screws. Tighten the locknuts
as required.
The expansion anchor can be removed after completion of the core-
drilling operation for reuse elsewhere. To do so, turn the knurled
threaded rod back by about 10 mm. A light tap on the knurled threa-
ded rod will release the pin of the expansion anchor, allowing it to be
removed.
3.3.3. Securing to masonry with a threaded rod
When drilling in porous masonry, note that it is not sufficient to secure
the drill upright with plugs. It is recommendable in these cases to drill
right through the masonry and secure the drill upright with a threaded
rod (e.g. M12), secured from the other side by a washer and nut.
3.3.4. Securing with vacuum suction
When carrying out core-drilling operations on items with shiny surfa-
ces (e.g. tiles or marble) that do not permit securing with plugs, the
drill upright can be secured by vacuum suction. Check the suitability
of the surface for vacuum suction. This method of securing is suitable
for the ROLLER’S drill upright D. The required drill-upright compo-
nents are supplied with the unit. Proceed as follows:
Place the sealing ring (43) into the channel on the underside of the
sole plate (6). Close off the slot (7) in the sole plate (6) with the cover
plate with hose connection (42). Attach a conventional vacuum pump
to the hose connection (41), and secure the underside of the drill
upright by suction. Regularly check the negative pressure throughout
the drilling operation. Observe the operating instructions supplied with
the vacuum pump. Operate the drill at low feed pressure.
3.3.5. Securing with a quick-action upright
The ROLLER’S drill upright D also offers the possibility of securing
the drill upright between the floor and ceiling, or between two walls.
This is done, for example, by placing a conventional quick-action
upright or a 1
1
/
4
” steel pipe between the grip head (29) of the drill
upright and the ceiling/wall, and tightening it by holding a tool such as
a screwdriver in the transverse hole. Tighten the locknut (30).
Note that the quick-action upright or steel pipe must be aligned with
the boring trestle, and that the threaded spindle (33) should be
screwed by at least 20 mm into the thread of the boring trestle, and
into the thread of the grip head, in order to guarantee a stable sup-
port. Use a piece of wood or metal to distribute the pressure force of
the quick-action upright evenly on the ceiling or wall.
3.4. Dry-boring with drill upright
Secure the drill upright using one of the methods described in 3.3.
Insert the drill collar (13) of the drive unit into the mounting in the
clamping angle (10), and tighten the fillister head screw(s) (8) with an
SW 6 hexagon socket head wrench. Screw the selected diamond
core drilling crown onto the drive spindle (11) of the drive unit, and
lightly hand-tighten. There is no need to tighten it with a wrench.
Using the dust-extraction system (see 2.4.2.). If the dust produced by
dry boring is not removed, the diamond core drilling crown may
overheat and suffer damage. There is also a danger of the compres-
sed drilling dust in the gap causing the diamond core drilling crown to
become blocked.
Activate the drive unit at the switch (21). Push in the switch and press
the orange button forward to lock it. Slowly advance the diamond core
drilling crown with the feed lever (4), and carefully tap the drill hole.
Once the annular bit has engaged all-round, the feed rate can be in-