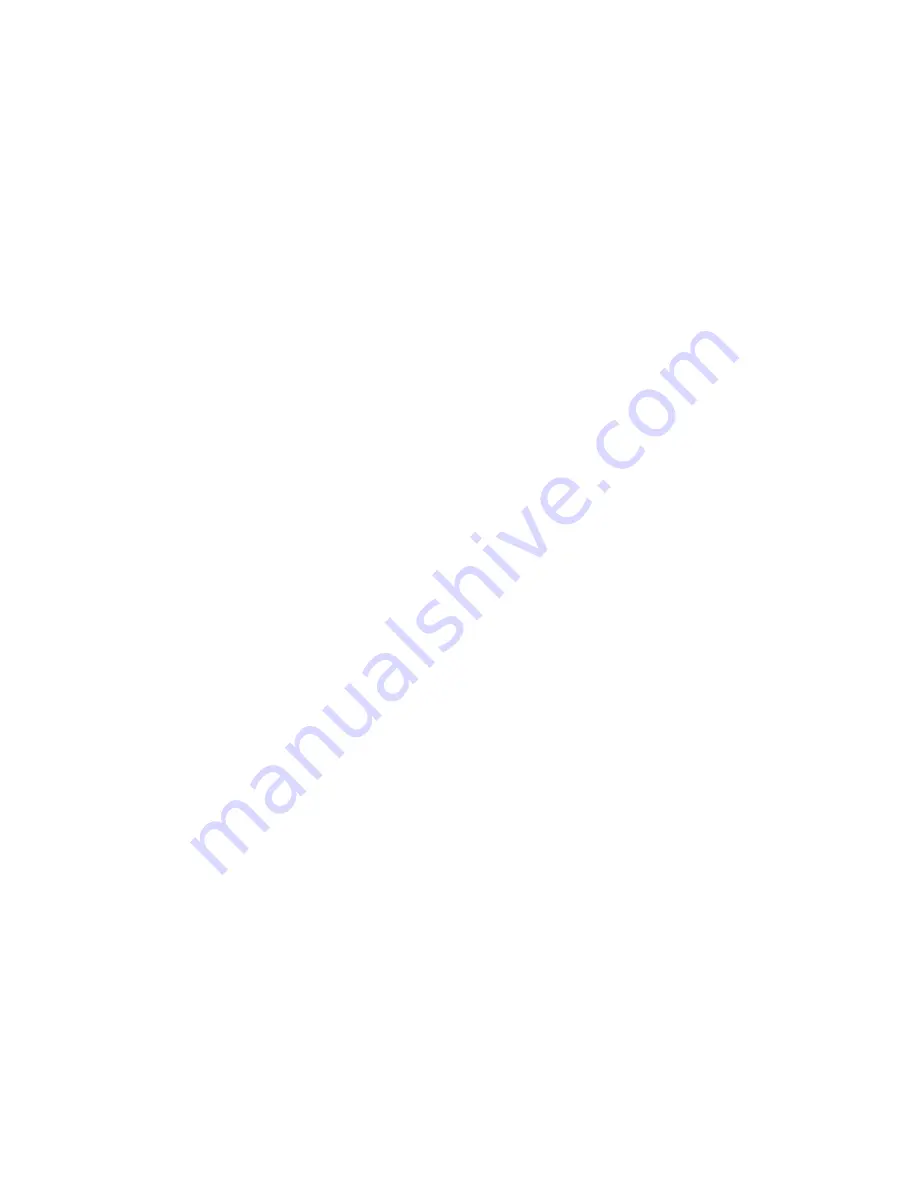
Page 8
MAINTENANCE INSTRUCTIONS
Your StreamMaster monitor and nozzle should be inspected prior to and after each use to ensure it is in
good operating condition. Periodically, an unanticipated incident occurs where the unit is misused in a
manner that is inconsistent with standard operating practices. A partial list of potential misuses includes:
• Operating above the maximum rated pressure or flow.
• Prolonged exposure to temperatures above 130°F, or below -25°F.
• Operating in a corrosive environment.
• Having the StreamMaster nozzle hit a fixed object during operation or transportation.
• Any other misuse that might be unique to your specific environment.
Also, there are many “tell tale” signs that indicate repair is in order, such as:
• Controls that are either inoperable or difficult to operate.
• Excessive wear
• Poor discharge performance
• Water leaks.
If any of the above situations are encountered, the StreamMaster monitor should be taken out of service,
repaired, and tested by a qualified technician before placing back in service.
MOTOR REPLACEMENT
To replace either the horizontal or vertical rotational motors:
1. Disconnect Power from the unit.
2. Loosen and remove the four socket screws (Item 4 on the Parts List) from the gearbox housing (52).
3. Slowly remove the motor assembly (59) and gearbox housing (52) from the unit.
IMPORTANT: Make sure the internal gear, (Item 47 on the Parts List), remains in place, (hold
with a screwdriver), to avoid gear alignment problems.
4. Loosen and remove the four socket head capscrews (51) from the inside of the gearbox housing that
hold the housing and the motor assembly together.
5. Remove gearbox housing (52) from the motor assembly (59).
6. Replace both o-ring seals (50 & 53) on the gearbox housing (52).
7. Attach the new motor assembly (59) to the gearbox housing (52) making sure all four screws (51) are tight.
8. Install the motor and gearbox housing assembly to the unit making sure all four socket screws are
tight. It may be necessary to rotate the motor slightly to get the motor gear to line up with the gears
inside the gearbox.
9. Restore power to the unit.
10. Test the operation of the unit.
Call Akron Brass Customer Service Department if any problems are encountered.