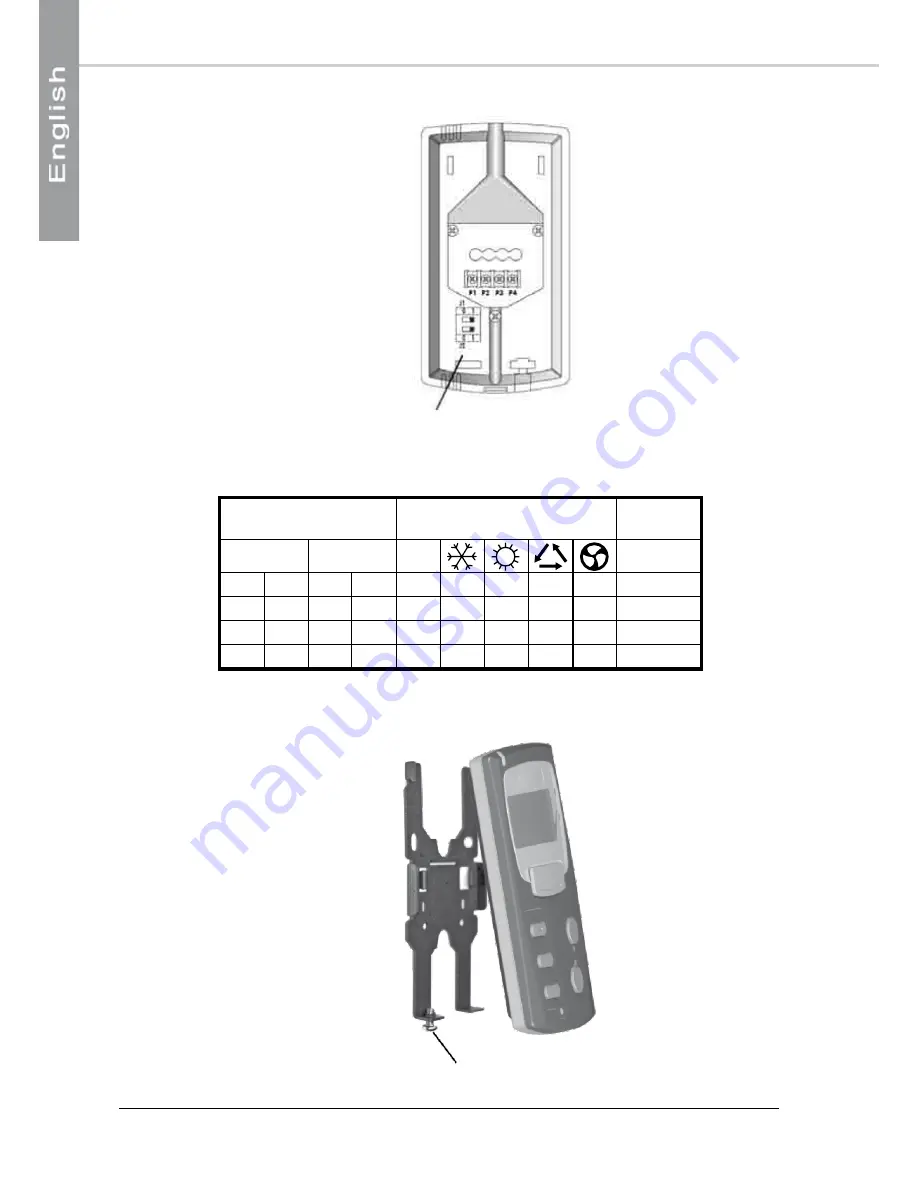
16
Set the DIP switches marked J1 and J2 in accordance with your configuration nd the modes that are accessible.
Clip the RCL control onto the support bracket.
Replace the lower screw in such a way that the RCL control is held firmly in place on the support bracket
RCL control recommended
setting
Accessible modes
PLUG
Dip J1
Dip J2
0
1
0
1
Off
Cool Heat Auto
Fan
X
X
X
X
X
ST
X
X
X
X
X
RC - RH - SH
X
X
X
X
X
X
X
RC - RH - SH
Dips switches J1 and J2 for
parameterisation
Lower screw