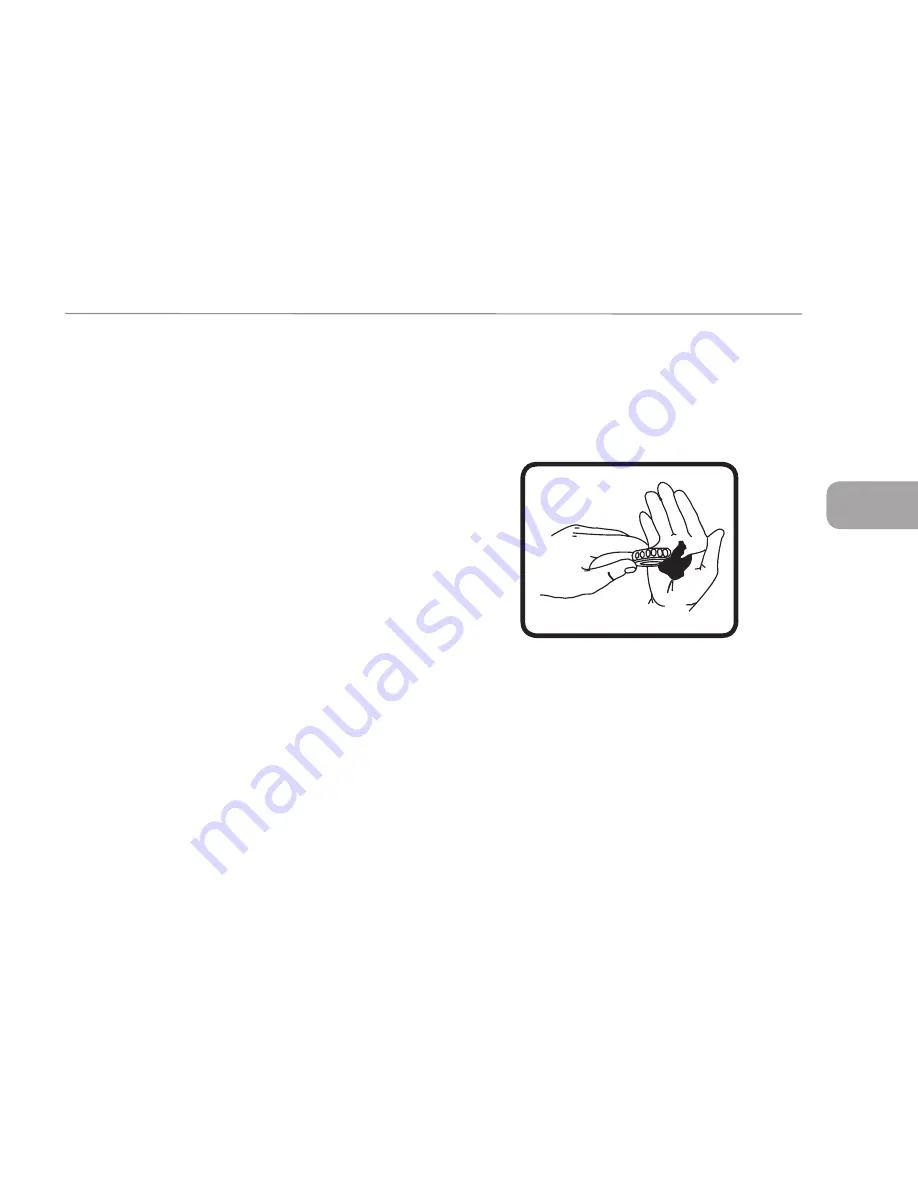
D
D - 4
EXTERIOR
Wheel Bearing Maintenance
1. Jack trailer at marked jack location pad behind axle on mainframe.
2. Remove hubcap or spindle cover, wheel and tire.
3. Remove cotter pin.
4. Remove dust cap.
5. Remove spindle nut and washer.
6. Remove bearings, hub and rotor.
7. Lay down hub and rotor with inside grease seal down. Knock out inner bearing and
grease seal using wood or plastic dowel and hammer.
8. Clean all parts thoroughly with kerosene.
9. Check all bearings and races for chips or roughness of any kind. Any damaged
component must be replaced.
10. Pack bearing with a good grease (No 2 grade-265 ASTM penetration or equiva-
lent).
11. Install inner bearing.
12. Install new grease seal in hub or rotor using wooden or rawhide mallet.
13. Install hub and drum on spindle.
14. Install outer bearing.
15 Install washer and spindle nut
16. While rotating the wheel, tighten the spindle nut with a 12” wrench until there is a
slight tension. Then back off one notch and install cotter pin. There should now be
from .001” to .010” endplay in hub. If not, back off one notch.
17. Check the lug nuts at 10, 25, and again at 50 miles of travel after replacing a wheel.
Torque wheels to 100 ft. lbs.
When greasing bearings by hand, place a glob of grease in the palm of one hand and
push the large end of the bearing down into the grease (see illustration). Keep turning
the bearing around and forcing it down through the grease until the grease is extruded
up through the opposite end. Wipe the extra grease in your hand around the outside of
the bearing. It’s not necessary to fill the hub and dust cap with grease.