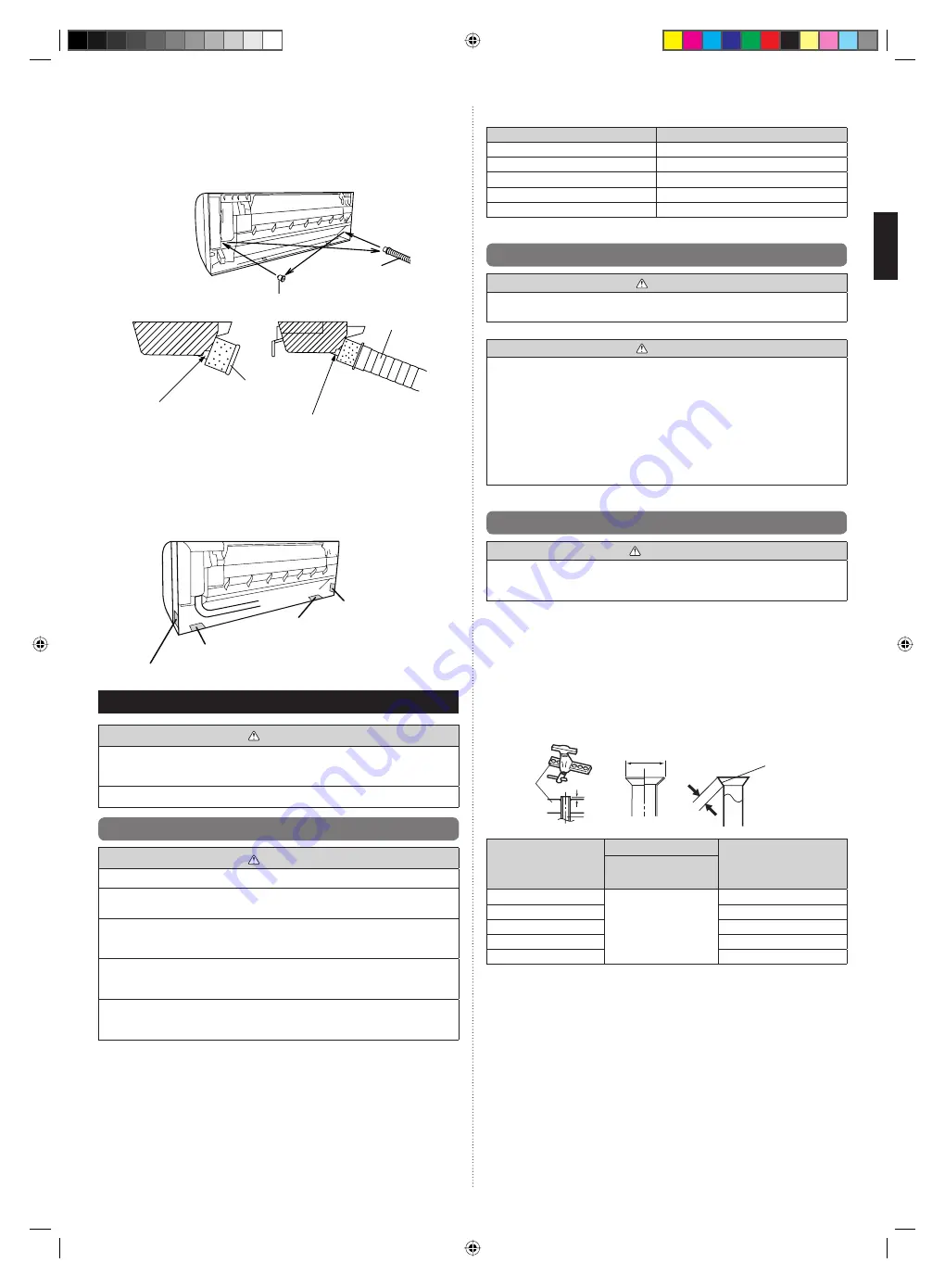
En-4
Thicknesses of Annealed Copper Pipes (R410A)
Pipe outside diameter [mm (in.)]
Thickness [mm]
6.35 (1/4)
0.80
9.52 (3/8)
0.80
12.70 (1/2)
0.80
15.88 (5/8)
1.00
19.05 (3/4)
1.20
1
4.2. Pipe requirement
CAUTION
Refer to the installation manual for the outdoor unit for description of allowable pipe
length and height difference.
Use pipe with water-resistant heat insulation.
CAUTION
Install heat insulation around both the gas and liquid pipes. Failure to do so may
cause water leaks.
Use heat insulation with heat resistance above 120 °C. (Reverse cycle model only)
In addition, if the humidity level at the installation location of the refrigerant piping is
expected to exceed 70 %, install heat insulation around the refrigerant piping.
If the expected humidity level is 70 to 80 %, use heat insulation that is 15 mm or
thicker and if the expected humidity exceeds 80 %, use heat insulation that is 20 mm
or thicker. If heat insulation is used that is not as thick as speci
fi
ed, condensation may
form on the surface of the insulation.
In addition, use heat insulation with heat conductivity of 0.045 W/(m·K) or less
(at 20 °C).
1
4.3. Flare connection (pipe connection)
WARNING
Tighten the
fl
are nuts with a torque wrench using the speci
fi
ed tightening method.
Otherwise, the
fl
are nuts could break after a prolonged period, causing refrigerant to
leak and generate hazardous gas if the refrigerant comes into contact with a
fl
ame.
4.3.1. Flaring
Use special
fl
are tool exclusive for R410A.
(1) Cut the connection pipe to the necessary length with a pipe cutter.
(2) Hold the pipe downward so that cuttings will not enter the pipe and remove any burrs.
(3) Insert the
fl
are nut (always use the
fl
are nut attached to the indoor and outdoor units (or
RB unit) respectively) onto the pipe and perform the
fl
are processing with a
fl
are tool.
Use the special R410A
fl
are tool. Leakage of refrigerant may result if other
fl
are nuts
are used.
(4) Protect the pipes by pinching them or with tape to prevent dust, dirt, or water from
entering the pipes.
Check if [L] is
fl
ared uniformly and
is not cracked or scratched.
Die
Pipe
A
B
L
Pipe outside
diameter [mm (in.)]
Dimension A [mm]
Dimension B
-
0
0.4
[mm]
Flare tool for R410A,
clutch type
6.35 (1/4)
0 to 0.5
9.1
9.52 (3/8)
13.2
12.70 (1/2)
16.6
15.88 (5/8)
19.7
19.05 (3/4)
24.0
When using conventional (R22)
fl
are tools to
fl
are R410A pipes, the dimension A should
be approximately 0.5 mm more than indicated in the table (for
fl
aring with R410A
fl
are
tools) to achieve the speci
fi
ed
fl
aring. Use a thickness gauge to measure the dimension A.
It is recommended that a R410A
fl
aring tool is used.
[For
1
Rear piping,
2
Right piping and
3
Bottom piping]
• The drain hose and drain cap are used as they are.
[For
4
Left bottom piping,
5
Left piping and
6
Center piping,
7
Left
rear piping]
• Remove the drain cap and drain hose. Mount the drain cap and drain hose to the drain
port on its opposite side.
Left side
Right side
Drain cap
Drain hose
Drain cap
Drain hose
Insert the drain hose until it butts
against the drain port.
Insert the drain cap until it butts
against the drain port.
3.3.4. Cut-out for piping on front cover
[For
2
Right piping,
3
Bottom piping,
4
Left bottom piping and
5
Left piping]
• Use a metal shears or other cutting tool to cut along the groove in the plastic for the
piping that will coming out of the front cover.
For
2
Right piping
For
5
Left piping
For
4
Left bottom piping
For
3
Bottom piping
4. PIPE INSTALLATION
]
CAUTION
Be more careful that foreign matter (oil, water, etc.) does not enter the piping than with
refrigerant R410A models. Also, when storing the piping, securely seal the openings
by pinching, taping, etc.
While welding the pipes, be sure to blow dry nitrogen gas through them.
]1
4.1. Selecting the pipe material
CAUTION
Do not use existing pipes from another refrigeration system or refrigerant.
Use pipes that have clean external and internal sides without any contamination which
may cause trouble during use, such as sulfur, oxide, dust, cutting waste, oil, or water.
It is necessary to use seamless copper pipes.
Material : Phosphor deoxidized seamless copper pipes
It is desirable that the amount of residual oil is less than 40 mg/10 m.
Do not use copper pipes that have a collapsed, deformed, or discolored portion
(especially on the interior surface). Otherwise, the expansion valve or capillary tube
may become blocked with contaminants.
Improper pipe selection will degrade performance. As an air conditioner using R410A
incurs pressure higher than when using conventional (R22) refrigerant, it is necessary
to choose adequate materials.
• Thicknesses of copper pipes used with R410A are as shown in the table.
• Never use copper pipes thinner than those indicated in the table even if they are
available on the market.
9373370147-02_IM.indb 4
9373370147-02_IM.indb 4
1/21/2013 4:10:12 PM
1/21/2013 4:10:12 PM