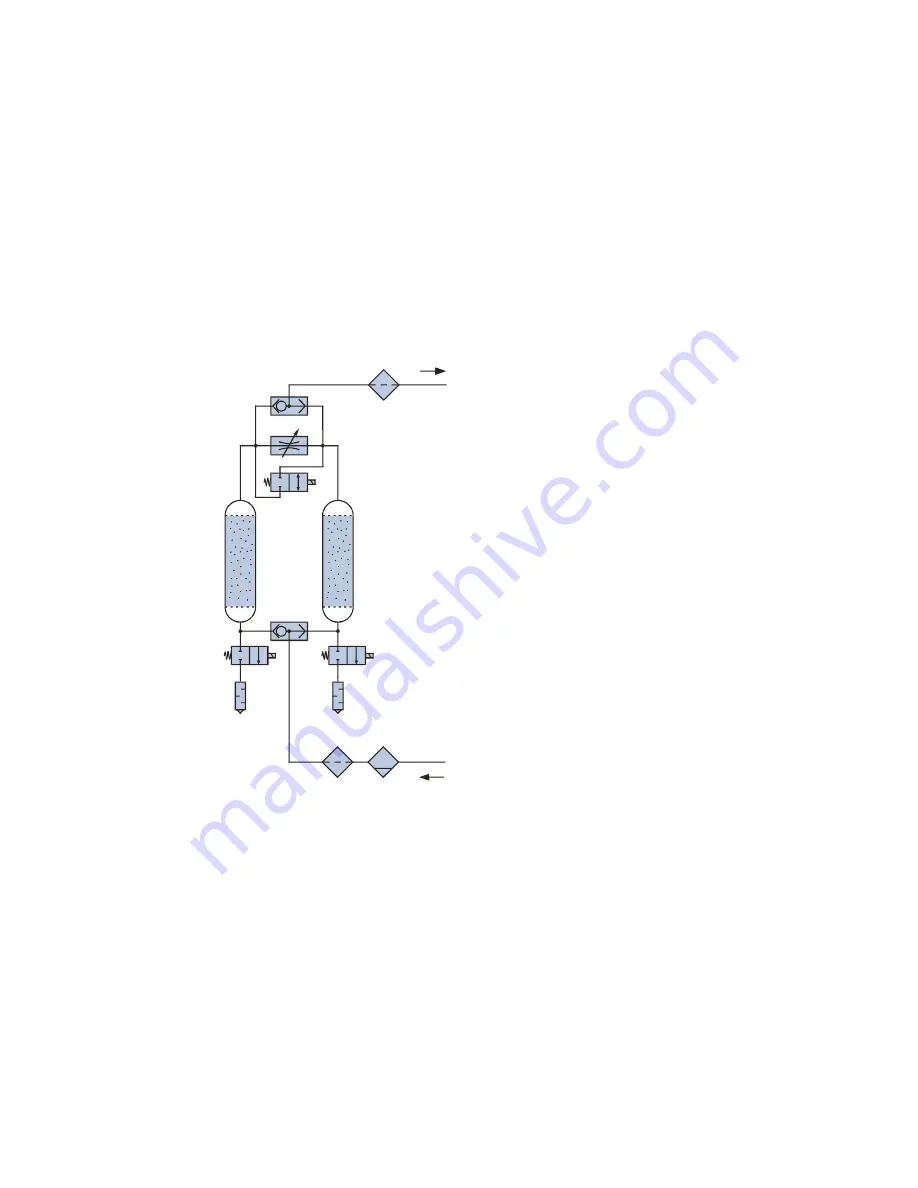
16
Working of an adsorption compressed air dryer
The additional measurement of achieved dew point value in compressed air enables
reduction of operating cost by optimisation of the regeneration and drying intervals, so that
the amount of compressed air required for the drying process (regeneration) with respect to
the air consumption is minimized. Through a regulation mechanism, the system automatically
adapts itself to the changing operating conditions.
At inlet of dryer, the compressed air with a dew point of about +30 ° tpd is supplied from the
air chamber. At outlet of the dryer, the dried compressed air with a dew point value of about.-
40... -80 °C tpd is supplied for use.
The dryer consists of two drying columns
(Q1 and Q2), which alternatively goes
into operation or regeneration mode. The
cartridge, through which the compressed
air passes, dries it and absorbs the water
contained in the air. Meanwhile, the
second cartridge is flown through in re-
verse direction by expanded dry air and
hence dried out. After some time the two
columns are interchanged and the drying
process is continued with the column re-
generated earlier.
The three solenoid valves (Y1, Y2, Y3)
and two OR gates (D1, D2) are used to
control the compressed air path through
the drying columns. The flushing air for
regeneration of drying capsule is created
with the flow control valve (D3).
The so called "Molecular mesh" is used
as the drying agent in the columns. It is
extremely porous material, called as
Zeolithe, which contains capillary like
pores. The water contained in the com-
pressed air gets stored in these pores.
During flushing through with dry air,
which is created by expansion of dried
compressed air, the pores again deliver the contained water. Thus the drying agent is
regenerated and can be again used in the next cycle for the drying process of compressed
air.
Therefore, the energy for drying is exclusively prepared by the energy of the compressed air.
Basically, the triggering of valves can take place with a simple timer, however, which must be
certainly designed for the most unfavourable operating condition (i.e. max. drying capacity at
maximum ambient temperature and maximum air flow). However, the energy consumption
will be unreasonably high at partial or no load conditions but it will survive the danger of
over-saturated dryers during full load condition.
Q 1
Q 2
Y 1
Y 2
D 1
D 2
Y 3
D 3