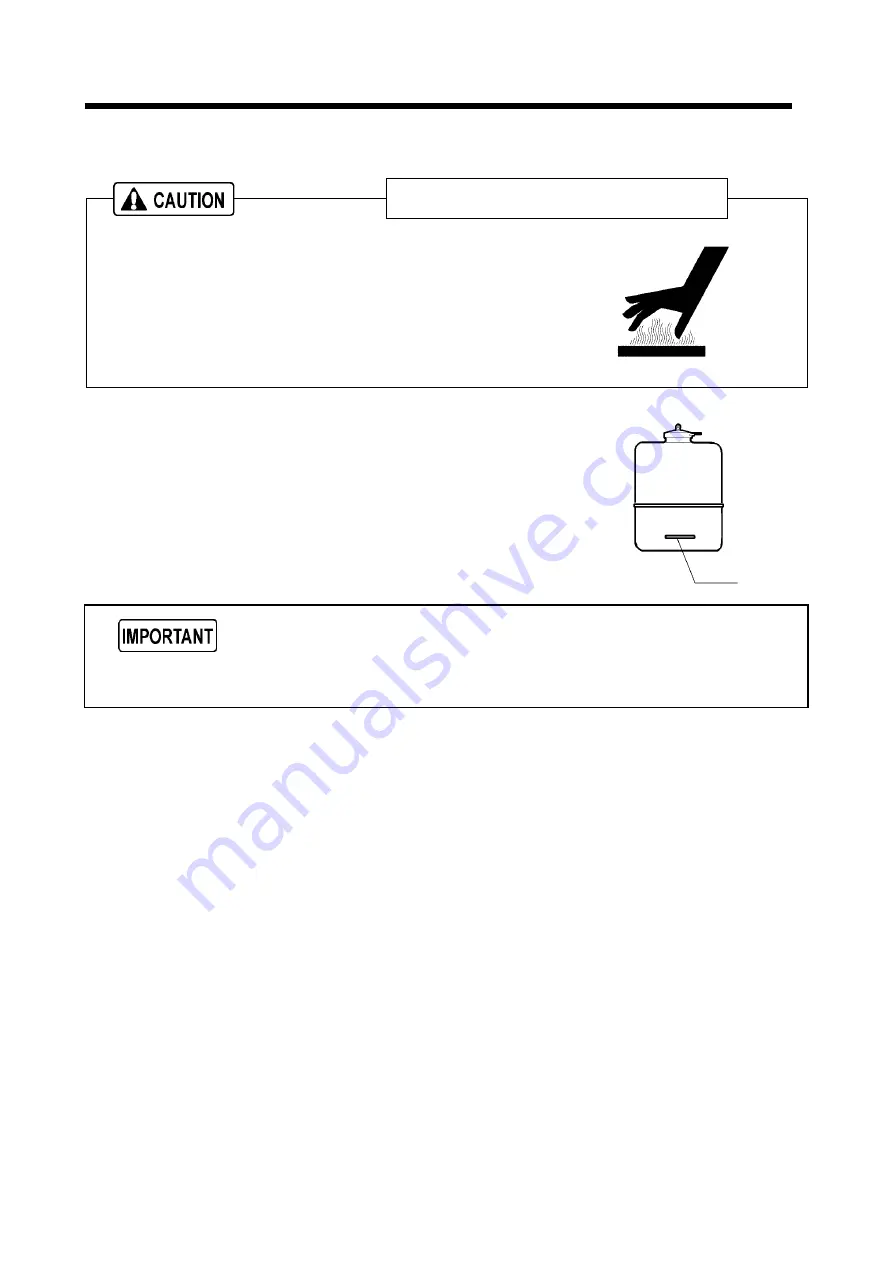
4. Operation
4
-
3
4.3.2 Check Coolant Level
Taking off the Header tank radiator cap
Be sure to stop the machine and allow time to cool. Then loosen
the radiator cap one notch. After the coolant water is sufficiently
cooled and the inner pressure is released, take the cap off.
If this procedure is neglected, the inner pressure can blow off
the cap. Steam jetting out of the radiator could result in causing
scalding. Follow this procedure under all circumstances.
W005
Check the coolant level in the reserve tank. If it is lower than
the limit, open the cap and replenish the coolant. (Level must
be kept above LOW mark.)
If little coolant is left in the reserve tank, replenish the
radiator with cooling water. (See 5.6.12)
Do not continue operation at low coolant level. Air bubble is mixed into radiator, and it causes
damage to the radiator.
A030173
LOW
Discount-Equipment.com
Summary of Contents for PDS400S-6B1
Page 14: ...D i s c o u n t E q u i p m e n t c o m...
Page 28: ...D i s c o u n t E q u i p m e n t c o m...
Page 37: ...D i s c o u n t E q u i p m e n t c o m...
Page 40: ...D i s c o u n t E q u i p m e n t c o m...
Page 43: ...D i s c o u n t E q u i p m e n t c o m...
Page 45: ...D i s c o u n t E q u i p m e n t c o m...
Page 50: ...D i s c o u n t E q u i p m e n t c o m...
Page 51: ...10 Piping Diagram 10 1 A040051 D i s c o u n t E q u i p m e n t c o m...
Page 52: ...www discount equipment com D i s c o u n t E q u i p m e n t c o m...