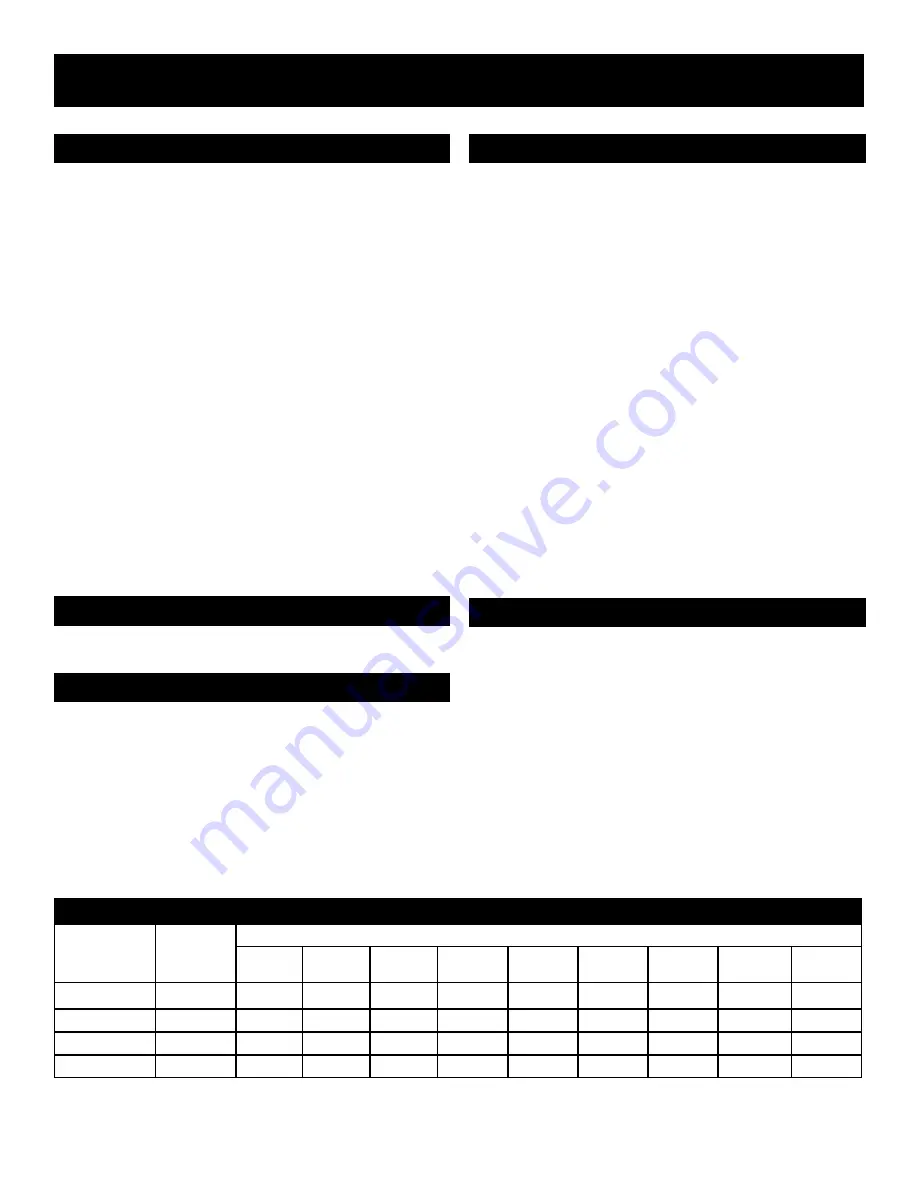
2
3
WARNINGS - CONTINUED
Hazardous fluid or toxic fumes can cause serious injury or
death if splashed in eyes or on skin, inhaled or swallowed.
Know the hazards of the fluid you are using. Store &
dispose of hazardous fluids according to manufacturer,
local, state & national guidelines.
ALWAYS
wear protective eyewear, gloves, clothing
and respirator as recommended by fluid manufacturer.
Keep all labels on the unit clean and readable.
Replacement labels are available from manufacturer.
Tighten all fluid connections securely before each use. High
pressure fluid can dislodge a loose coupling or allow high
pressure spray to be emitted from the coupling and result in
an injection injury or serious bodily injury.
Use only hose that has a spring guard. The spring guard
helps protect the hose from kinks or other damage which
could result in hose rupture and cause an injection injury.
NEVER
use a damaged hose, which can result in hose
failure or rupture and cause in injection injury or other
serious bodily injury or bodily damage. Before each use,
check entire hose for cuts, leaks, abrasion or bulging of
cover, or damage or movement of couplings. If any of
these conditions exist, replace the hose immediately.
Never use tape or any device to try to mend the hose as it
cannot contain the high pressure fluid.
NEVER ATTEMPT
TO RECOUPLE THE HOSE.
High pressure hose is not
recoupleable.
Help prevent damage to the hose by handling and routing
it carefully. Do not move the sprayer by pulling it with the
hose.
Ground the sprayer and other components in the system
to reduce the risk of static sparking, fire or explosion which
can result in serious bodily injury and property damage.
ALWAYS GROUND ALL OF THESE COMPONENTS:
1. Sprayer: Connect a ground wire and clamp (supplied) to
a true earth ground.
2. Fluid Hose: use only grounded hoses.
3. Spray gun or dispensing valve: grounding is obtained
through connection to a properly grounded fluid hose
and pump.
4. Object being sprayed: according to your local code.
5. All solvent pails used when flushing should only be
metal pails which are conductive.
Once each week, check electrical resistance of hose (when
using multiple hose assemblies, check overall resistance of
unpressurized hose must not exceed 29 megohms (max)
for any coupled length or combination of hose lengths. If
hose exceeds these limits, replace it immediately.
Never exceed 500 Ft. (150 m.) overall combined hose
length to assure electrical continuity.
Keep clear of moving parts when starting or operating
the sprayer. Do not put your fingers into any openings
to avoid amputation by moving parts or burns on hot
parts.Precaution is the best insurance against an
accident.
When starting the engine, maintain a safe distance
from moving parts of the equipment.
Before adjusting or servicing any mechanical part
of the sprayer, follow the
PRESSURE RELIEF
PROCEDURE
on page 8, and remove the ignition
cable from the spark plug to prevent accidental
starting of sprayer.
TOXIC FLUID HAZARD
WARNINGS CONTINUED ON NEXT PAGE.........
LABELING
HOSES
ALWAYS INSPECT SPRAYING AREA
GROUNDING
UL RECOMENDATION FOR MINIMUM GAUGE EXTENSION CORD
AMPERAGE
RATING
RANGE
VOLTAGE
LENGTH OF CORD IN FEET
25
50
100
150
200
250
300
400
500
5-6
120
18
16
12
12
10
10
8
8
6
6-8
120
18
16
12
10
10
8
6
6
6
8-10
120
18
14
12
10
8
8
6
6
4
10-12
120
16
14
10
8
8
6
6
4
4