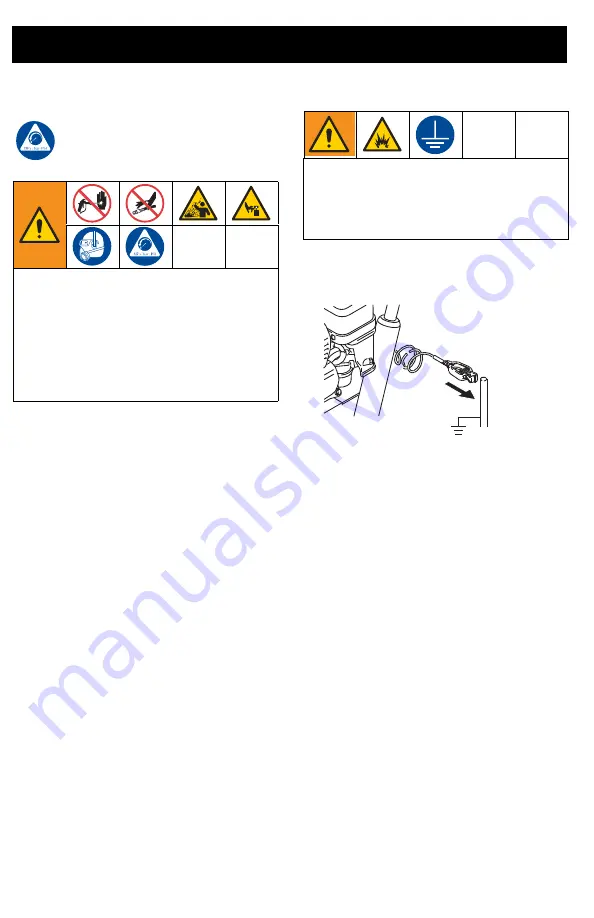
Pressure Relief Procedure
8
3A4108F
Pressure Relief Procedure
Follow the
Pressure Relief
Procedure
whenever you see this
symbol.
1.
Engage trigger lock.
2.
Turn engine ON/OFF switch to OFF.
3.
Move pump switch to OFF and turn
pressure control knob fully
counterclockwise.
4.
Disengage trigger lock. Hold metal part
of gun firmly to side of grounded metal
pail, and trigger gun to relieve pressure.
5.
Engage gun trigger lock.
6.
Turn prime valve down to DRAIN
position. Leave prime valve down until
ready to spray again.
7.
If you suspect the spray tip or hose is
clogged or that pressure has not been
fully relieved:
a.
VERY SLOWLY loosen the tip
guard retaining nut or the hose end
coupling to relieve pressure
gradually.
b.
Loosen the nut or coupling
completely.
c.
Clear the obstruction in the hose or
tip.
Grounding
To ground sprayer:
Attach sprayer
grounding clamp to earth ground.
Air and fluid hoses:
Use only electrically
conductive hoses with a maximum of 500 ft.
(150 m) combined hose length to ensure
grounding continuity. Check electrical
resistance of hoses. If total resistance to
ground exceeds 29 megohms, replace hose
immediately.
Spray gun:
Ground through connection to a
properly grounded fluid hose and pump.
Solvent pails used when flushing:
Follow
local code. Use only conductive metal pails,
placed on a grounded surface. Do not place
the pail on a non-conductive surface, such as
paper or cardboard, which interrupts
grounding continuity.
To maintain grounding continuity when
flushing or relieving pressure:
Hold metal
part of the spray gun firmly to the side of a
grounded metal pail, then trigger the gun.
This equipment stays pressurized until
pressure is manually relieved. To help
prevent serious injury from pressurized
fluid, such as skin injection, splashing fluid
and moving parts, follow the
Pressure
Relief Procedure
when you stop
spraying and before cleaning, checking,
or servicing the equipment.
This equipment must be grounded to
reduce the risk of static sparking. Static
sparking can cause fumes to ignite or
explode. Grounding provides an escape
wire for the electric current.
ti5787a
Summary of Contents for GS950
Page 34: ...Notes 34 3A4108F Notes...