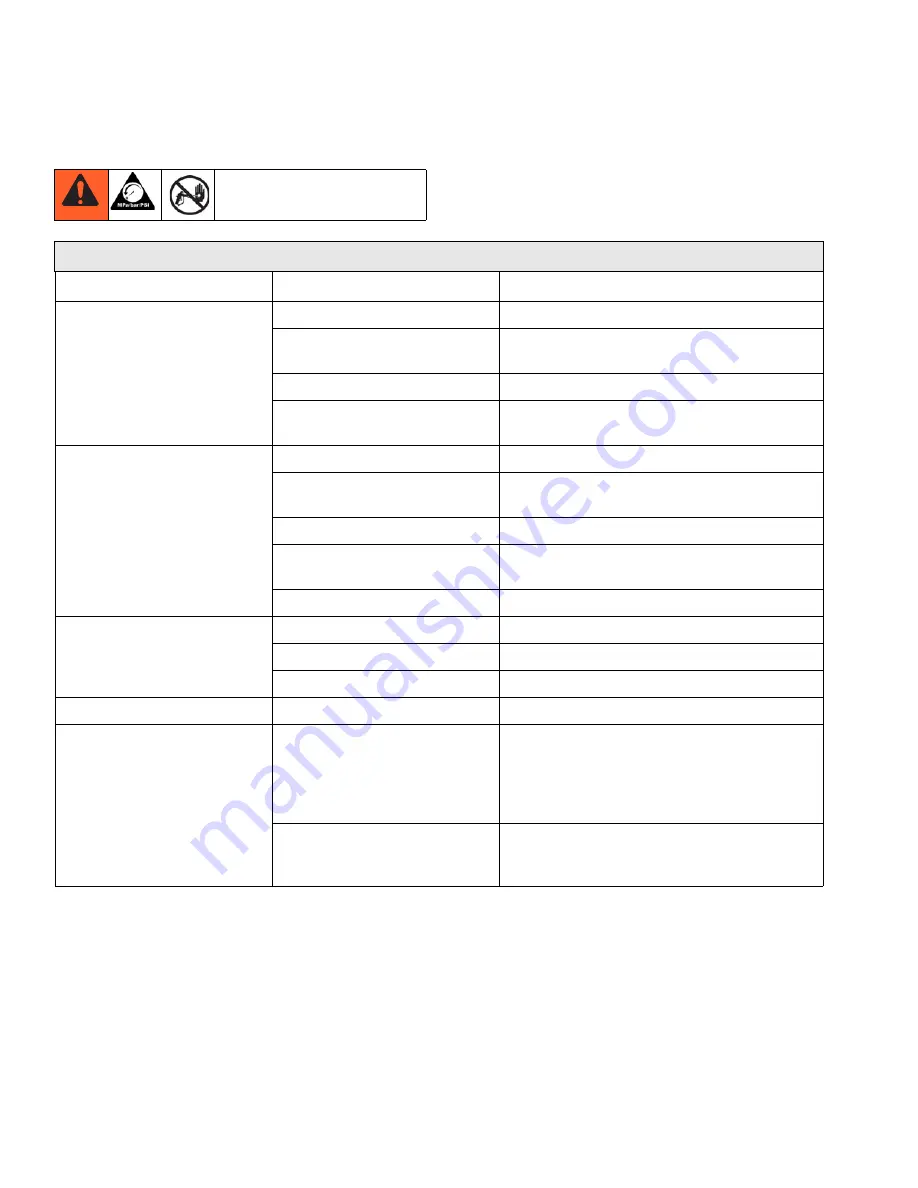
Troubleshooting
20
3A1184A
Troubleshooting
General
Problem
Cause
Solution
Unit doesn’t prime
Airleak due to loose suction nut
Tighten suction nut.
Airleak due to worn o-rings
Replace o-ring (110636) on suction seat and
o-ring (867390) below suction seat.
Stuck or fouled balls
Service inlet and outlet valves.
Prime/Pressure Relief valve not
opening
Clean or replace Prime Valve (866428)
Unit primes but has poor or no
pressure
Pressure set too low
Turn up pressure.
Filter(s) are clogged
Clean or replace gun filter, inlet filter, and/or
manifold filter.
Outlet valve fouled/worn.
Service outlet valve.
Prime/pressure relief valve
bypassing
Clean or replace prime valve (866428).
Packings and/or piston worn
Tighten packing nut, repack unit.
Unit does not maintain good
spraying pressure
Blown spray tip
Replace spray tip.
Packings and/or pistons worn
Repack unit.
Upper seat worn
Replace upper seat.
Unit does not run
See
Machine Does Not Start
Machine does not start
Control Settings
Make sure machine is plugged into the wall.
Verify the on-off switch is in the ON position
and the pressure control knob is turned all the
way to the right (clockwise for maximum pres-
sure).
Circuit Breaker
Use multi-meter to test the breaker for continu-
ity or replace with a new breaker. If breaker
reads good, see
Power Source
.
Summary of Contents for 24F572
Page 35: ...Notes 3A1184A 35 Notes...