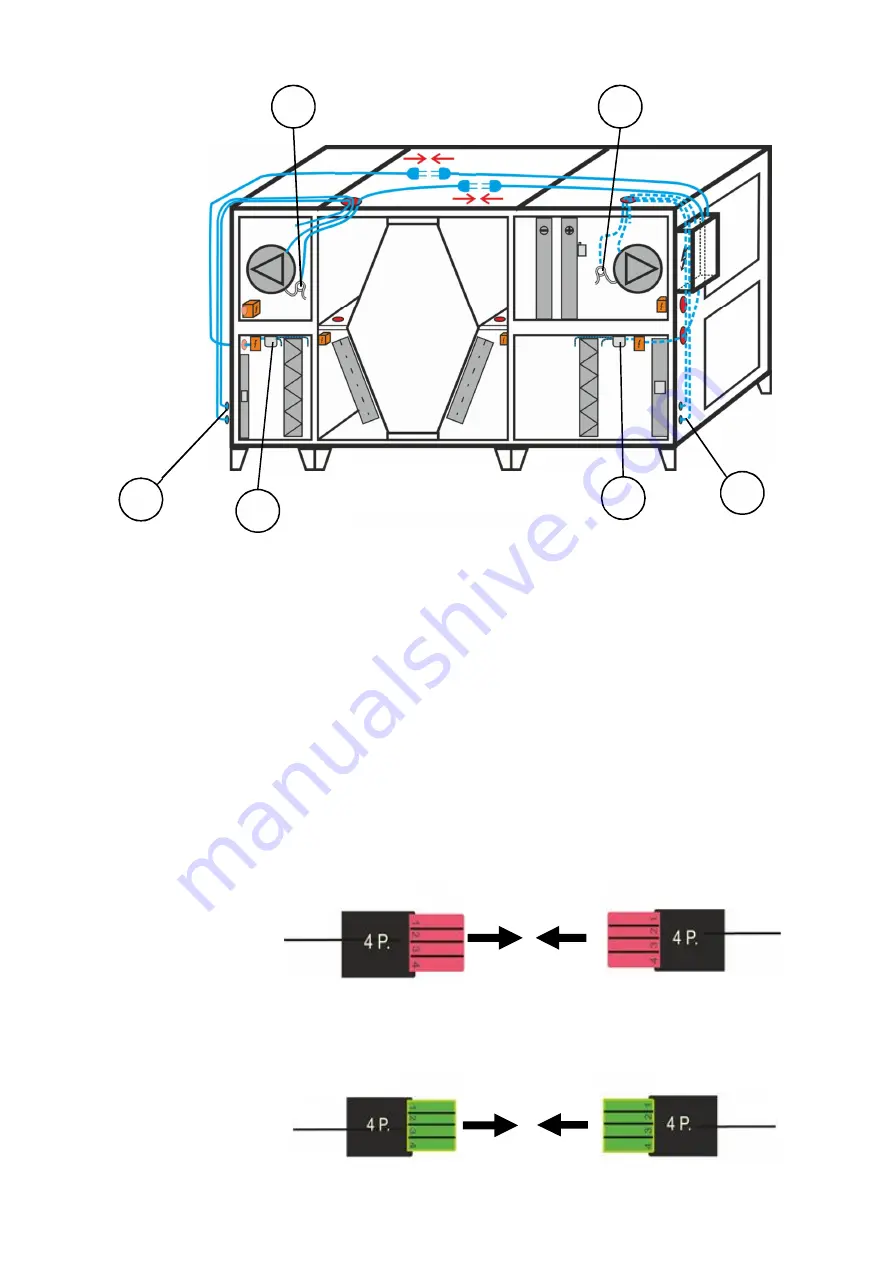
36
7.4.
Connecting servo motors
Connected:
●
Cable powering the by-pass flap (
SB
) is connected to the connector.
Connected, optional equipment
●
Circulation damper (
SC
) servo motor is connected to the connector.
●
The circuit of cooler
CHW
is connected to the hydraulic kit.
●
The circuit of heater
TPO
is connected to the hydraulic kit.
●
Hydraulic kit
LS
controlling the chiller or heater is located on the back side of the unit. The kit is
completely connected up to the junction box;
●
Water pump
LP
in the heating circuit is located on the back side of the unit. The kit is completely
connected up to the junction box;
●
Shut-off flap
Si
is connected up to the junction box;
●
Shut-off flap
Se
is connected to the connector.
Connect
●
Plug in connector powering the by-pass flap (
SB
).
Connect, optional equipment:
●
Plug in connector powering the circulation flap (
SC
). Available only for units equipped by RD5
control system or for units without control system.
Connection of pressure sensors
PMi
PMe
PFe
PFi
PDe
PDi
1
2
3
red
red
green
green