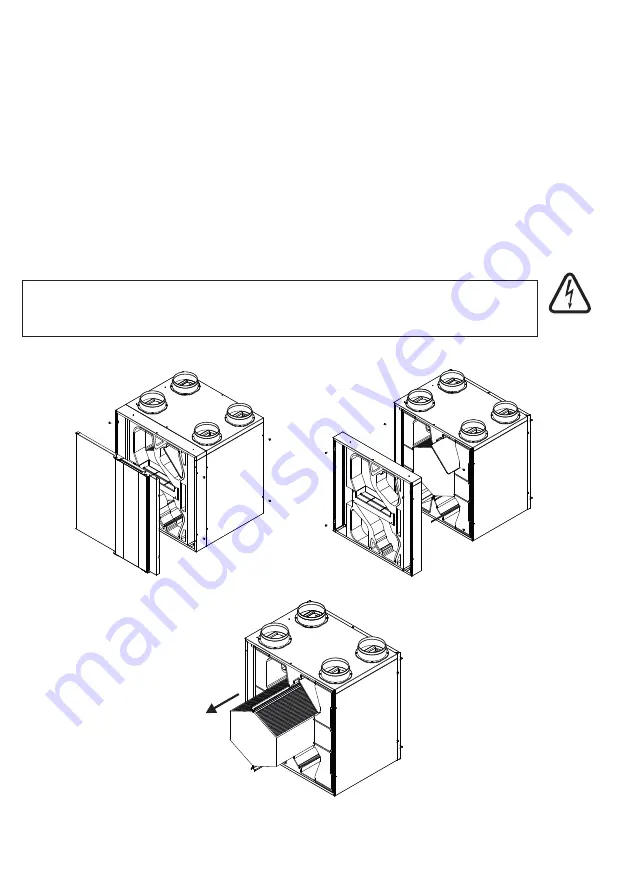
Note:
The G4 filters should be replaced once every six months or after a maximum of two
cleaning cycles. If an optional F7 filter is used please replace these filters after every
maintenance cycle (replacement filters are available on www.airflow.com, see page 15 for part
numbers).
Step 3:
Place the filters in the filter slots, close the service cover and slide it to the right to secure.
Approximately every two years it is recommended that the heat exchanger is checked for
contamination. This time scale may vary depending on the surroundings of the property.
Inspection should be carried out when checking the filters.
10.2 Heat Exchanger Maintenance
Page
26
of
32
Step 1:
Remove the front cover plate and the bypass module by unscrewing the screws.
Step 2:
Remove the filters and pull the heat exchanger out gently using the green strap.
Caution:
The fins of the heat exchanger are very thin and can easily be damaged.
WARNING
THE FAN AND ANCILLARY CONTROL EQUIPMENT MUST BE ISOLATED
FROM THE POWER SUPPLY DURING MAINTENANCE.
Danger
Electric Shock
risk
Summary of Contents for 90000660
Page 2: ...Page 2 of 32 ...
Page 30: ...Page 30 of 32 13 Declaration Of Conformity ...
Page 31: ...Page 31 of 32 ...