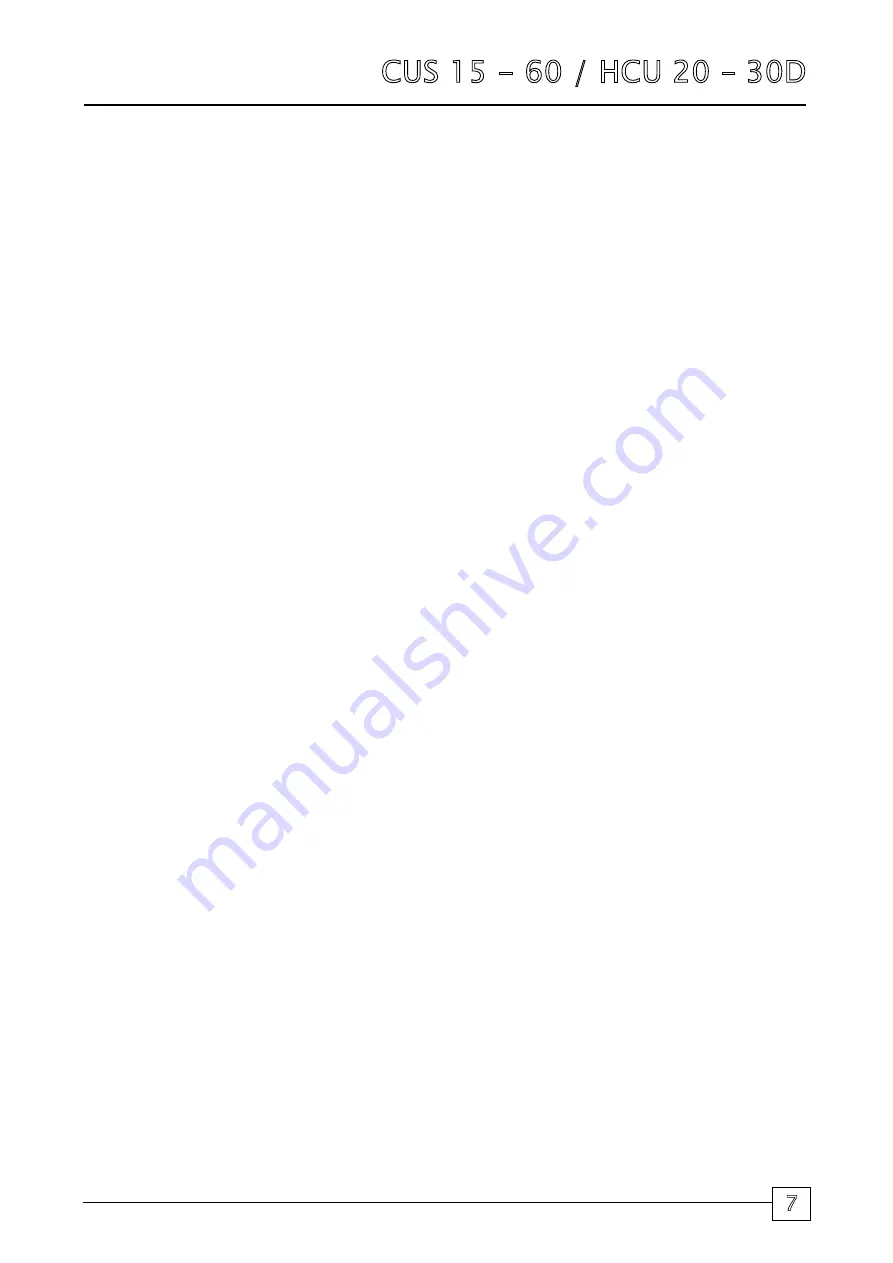
Condensing Units
CUS 15 - 60 / HCU 20
²
30D
Chillers & Condensing Units
Installation & Maintenance:Part No: 6259592 IM 07/14
7
Warranty
PROCEDURE
When warranty is allowed, a credit against the "G" number invoice will be raised.
Should warranty be refused the "G" number invoice becomes payable on normal
terms.
Warranty may be refused for the following reasons:
x
Misapplication of product or components.
x
Replaced part being returned damaged without explanation.
x
Unnecessary delays incurred in return of defective component.
RETURNS ANALYSIS
All faulty components returned under warranty are analysed on a monthly basis as a
means of verifying component and product reliability as well as supplier performance.
It is important that all component failures are reported correctly.
Loose Items List
FILTER DRIER
A suitably sized liquid line filter drier is shipped loose in the refrigeration compartment
of the condensing unit. This has been chosen to match the required refrigeration duty
of the compressor. To access this item, remove the service cover at the electrical
panel end by undoing the catches and lifting off.