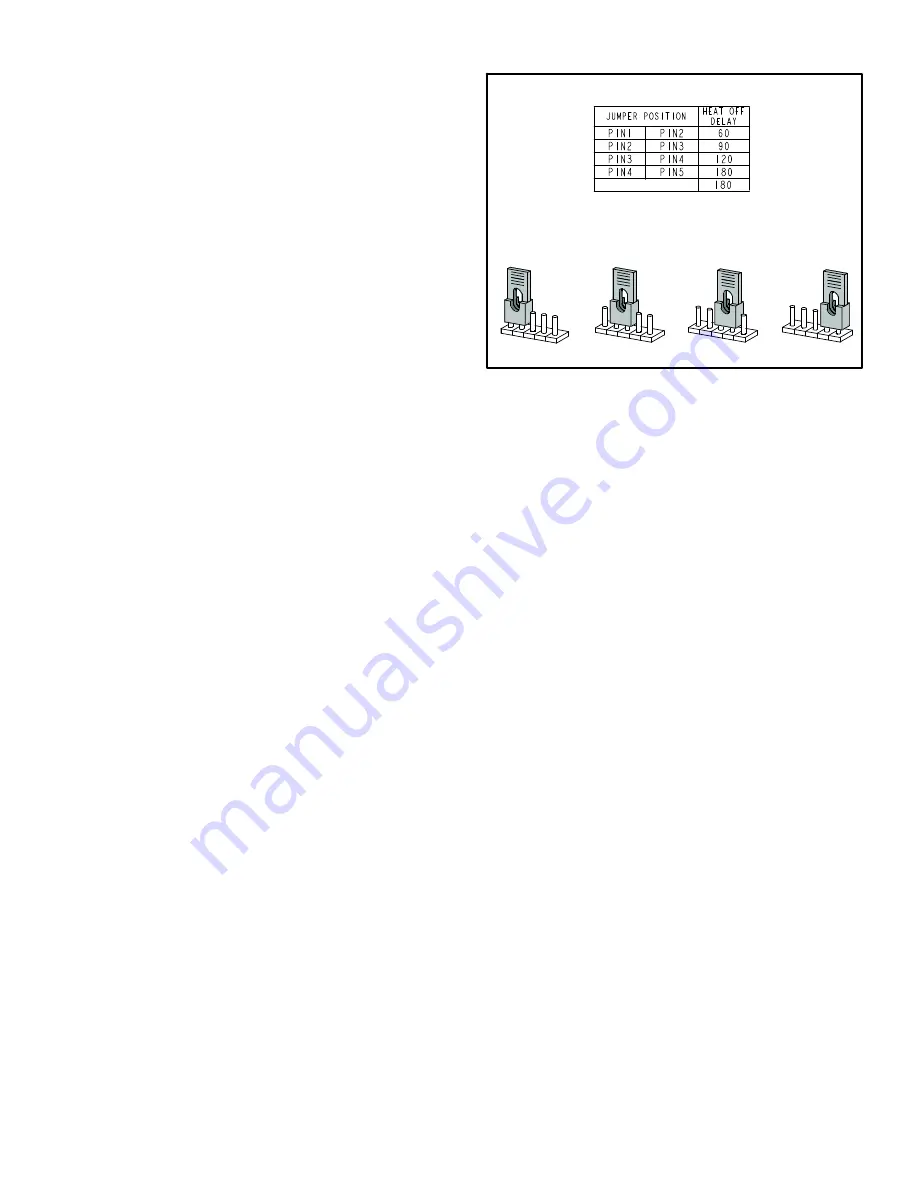
Page 41
Other Unit Adjustments
Primary Limit
The primary limit is located on the heating compartment
vestibule panel. This limit is factory set and requires no ad-
justment.
Flame Rollout Switches (Two)
These manually reset switches are located on the front of
the burner box.
Pressure Switch
The pressure switch is located in the heating compartment
on the cold end header box. This switch checks for proper
combustion air inducer operation before allowing ignition
trial. The switch is factory−set and must not be adjusted.
Temperature Rise
After the furnace has been started and supply and return air
temperatures have been allowed to stabilize, check the
temperature rise. If necessary, adjust the blower speed to
maintain the temperature rise within the range shown on
the unit nameplate. Increase the blower speed to decrease
the temperature. Decrease the blower speed to increase
the temperature rise. Failure to adjust the temperature rise
may cause erratic limit operation.
Fan Control
The fan on time of 30 seconds is not adjustable. The fan off
delay (amount of time that the blower operates after the
heat demand has been satisfied) may be adjusted by
changing the jumper position across the five pins on the
integrated control. The unit is shipped with a factory fan off
setting of 120 seconds. The fan off delay affects comfort
and is adjustable to satisfy individual applications. Adjust
the fan off delay to achieve a supply air temperature be-
tween 90° and 110°F at the moment that the blower is de−
energized. Longer off delay settings provide lower return
air temperatures; shorter settings provide higher return air
temperatures. See figure 56.
Thermostat Heat Anticipation
Set the heat anticipator setting (if adjustable) according to
the amp draw listed on the wiring diagram that is attached
to the unit.
Electrical
1 − Check all wiring for loose connections.
2 − Check for the correct voltage at the furnace (furnace
operating).
3 − Check amp-draw on the blower motor.
Motor Nameplate__________Actual__________
HEAT FAN-OFF TIME IN SECONDS
To adjust fan−off timing, reposition jumper across pins to
achieve desired setting.
NO JUMPER
FIGURE 56
60
90
120
180
60
90
120
180
60
90
120
180
60
90
120
180
60 Second
off Time
90 Second
off Time
120 Second
off Time
180 Second
off Time
Blower Speeds
Follow the steps below to change the blower speeds.
1 − Turn off electrical power to furnace.
2 − Remove blower access panel.
3 − Disconnect existing speed tap at integrated control
speed terminal.
NOTE
− Termination of any unused motor leads must be
insulated.
4 − Place unused blower speed tap on integrated control
PARK" terminal or insulate.
5 − Connect selected speed tap at integrated control
speed terminal.
6 − Resecure blower access panel.
7 − Turn on electrical power to furnace.
8 − Recheck temperature rise.
Electronic Ignition
The integrated control has an added feature of an internal
lockout. The feature serves as an automatic reset device for
integrated control lockout caused by ignition failure. This
type of lockout is usually due to low gas line pressure. After
one hour of continuous thermostat demand for heat, the in-
ternal lockout will break and remake thermostat demand to
the furnace and automatically reset the integrated control to
begin the ignition sequence.
Exhaust and Air Intake Pipe
1 − Check exhaust and air intake connections for tightness
and to make sure there is no blockage.
2 − Is pressure switch closed? Obstructed exhaust pipe
will cause unit to shut off at pressure switch. Check ter-
mination for blockages.
3 − Obstructed pipe or termination may cause rollout
switches to open. Reset manual flame rollout switches
on burner box assembly if necessary.