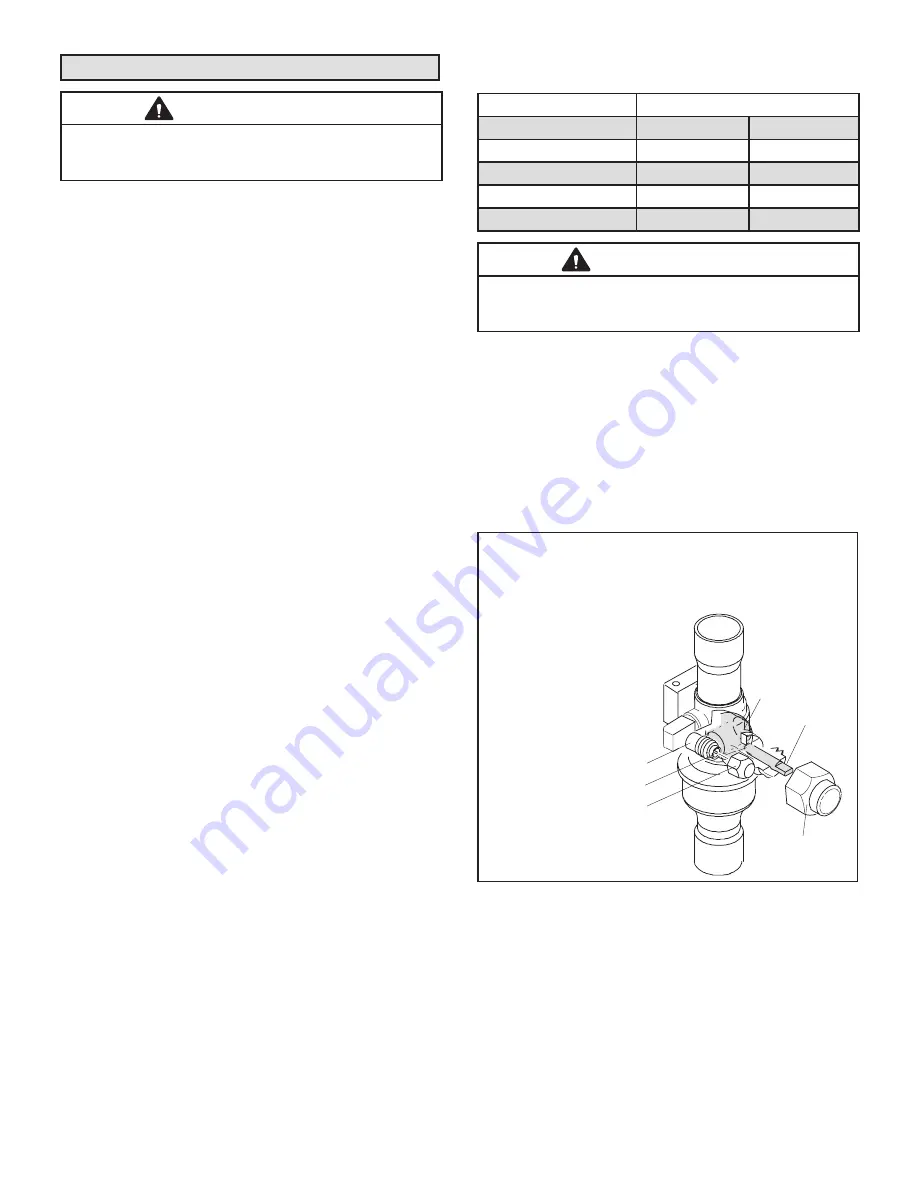
Page 13
STEP 5 – UNIT START-UP
IMPORTANT
If unit is equipped with a crankcase heater, it should
be energized 24 hours before unit start-up to prevent
compressor damage as a result of slugging.
1 - Rotate fan to check for binding.
2 -
Inspect all factory- and field-installed wiring for
loose connections.
3 - After evacuation is complete, open the liquid line
and vapor line service valve stems to release the
refrigerant charge (contained in outdoor unit) into
the system.
4 - Replace the stem caps and tighten to the value
listed in table 2.
5 - Check voltage supply at the disconnect switch. The
voltage must be within the range listed on the unit’s
nameplate. If not, do not start the equipment until
you have consulted with the power company and
the voltage condition has been corrected.
6 -
Connect manifold gauge set for testing and
charging.
7 - Set the thermostat for a cooling demand. Turn
on power to the indoor indoor unit and close the
outdoor unit disconnect switch to start the unit.
8 - Recheck voltage while the unit is running. Power
must be within range shown on the unit nameplate.
9 -
Check system for sufficient refrigerant using the
procedures outlined under
Checking Refrigerant
Charge.
OPERATING MANIFOLD GAUGE SET AND SERVICE
VALVES
The liquid and vapor line service valves are used for re-
moving refrigerant, flushing, leak testing, evacuating,
checking charge and charging.
Each valve is equipped with a service port which has a
factory-installed valve stem. Figures 15 and 16 provide
information on how to access and operate both angle- and
ball-type service valves.
Torque Requirements
When servicing or repairing heating, ventilating and air
conditioning components, ensure the fasteners are appro-
priately tightened. Table 2 lists torque values for fasteners.
TABLE 1
TORQUE REQUIREMENTS
Parts
Recommended Torque
Service valve cap
8 ft.-lb.
11 NM
Sheet-metal screws
16 in.-lb.
2 NM
Machine screws #10
28 in.-lb.
3 NM
Compressor bolts
90 in.-lb.
10 NM
Gauge port seal cap
8 ft.-lb.
11 NM
IMPORTANT
To prevent stripping of the various caps used, the
appropriately sized wrench should be used and fitted
snugly over the cap before tightening.
Using Manifold Gauge Set
When checking the system charge, only use a manifold
gauge set that features low loss anti-blow back fittings.
Manifold gauge set used with HFC-410A refrigerant sys-
tems must be capable of handling the higher system oper-
ating pressures. The gauges should be rated for use with
pressures of 0 - 800 psig on the high side and a low side
of 30" vacuum to 250 psig with dampened speed to 500
psi. Gauge hoses must be rated for use at up to 800 psig
of pressure with a 4000 psig burst rating.
BALL (SHOWN
CLOSED)
SERVICE PORT
CORE
TO
OPEN,
ROTATE STEM
COUNTERCLOCKWISE 90°.
TO
CLOSE,
ROTATE STEM
CLOCKWISE 90°.
SERVICE PORT
SERVICE PORT
CAP
STEM CAP
VALVE
STEM
1 - Remove stem cap with an appropriately sized wrench.
2 - Use an appropriately sized wrench to open. To open valve, rotate
stem counterclockwise 90°. To close, rotate stem clockwise 90°.
OPERATING BALL-TYPE SERVICE VALVE
FIGURE 14