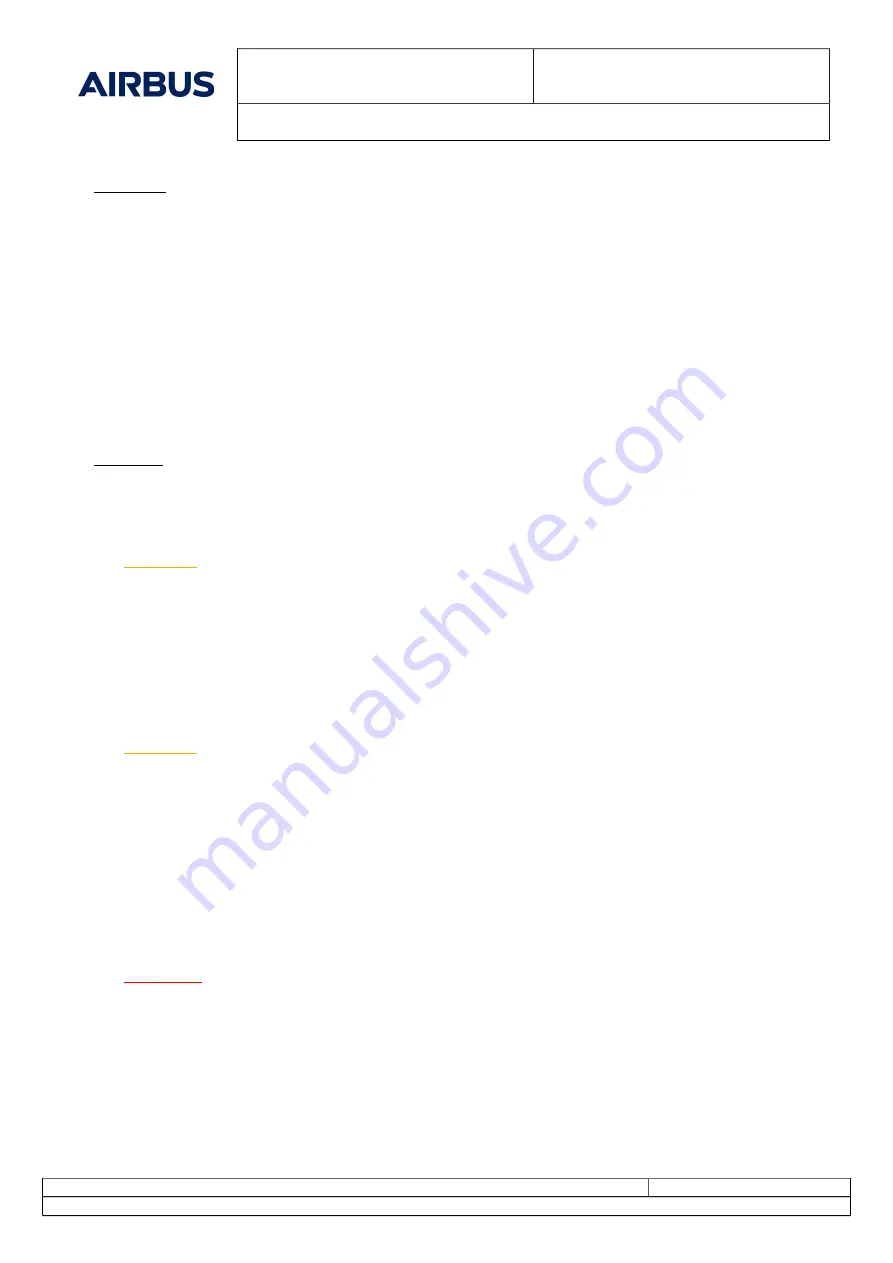
Customer : CSN
Type : A318/A319/A320/A321
Rev. Date : May 01, 2018
Manual : AMM
Selected applicability : 0317-0317
71-11-11-300-014-A - Repair the Aerodynamic
Sealant on the Air Intake Cowl or the P2/T2 Sensor
Print Date: July 02, 2018
Page 5 of 7
© AIRBUS S.A.S. ALL RIGHTS RESERVED. CONFIDENTIAL AND PROPRIETARY DOCUMENT.
3.
Job Set-up
Subtask 71-11-11-941-061-A
A.
Safety Precautions
(1) On the center pedestal, on the ENG panel 115VU:
(a) Put a WARNING NOTICE(S) to tell persons not to start the engine.
(2) Make sure that the engine 1(2) shutdown occurred not less than 5 minutes before you do this
procedure.
(3) On the overhead maintenance panel 50VU:
(a) Make sure that the ON legend of the ENG/FADEC GND PWR/1(2) pushbutton switch is off.
(b) Put a WARNING NOTICE(S) to tell persons not to energize the FADEC 1(2).
(4) Put the ACCESS PLATFORM 2M (6 FT) - ADJUSTABLE in position.
4.
Procedure
Subtask 71-11-11-350-065-A
A.
Remove the damaged aerodynamic sealant
(Ref. Fig. Aerodynamic Sealant Replacement)
CAUTION:
MAKE SURE THAT YOU DO NOT CAUSE DAMAGE TO THE ANODIZED SURFACE OF
THE LIPSKIN OR THE ACOUSTIC STRUCTURE. USE ONLY PLASTIC TOOLS AND PUT
PROTECTIVE MATS ON THE COWL.
(1) Use SPATULA - PLASTIC to remove most of the damaged or disbonded sealant.
(2) Use teflon tape (Material No. V02-007) and put a strip on each side of the repair area.
Subtask 71-11-11-110-060-A
B.
Clean the repair area.
CAUTION:
MAKE SURE THAT YOU DO NOT CAUSE DAMAGE TO THE ANODIZED SURFACE OF
THE LIPSKIN OR THE ACOUSTIC STRUCTURE. USE ONLY PLASTIC TOOLS AND PUT
PROTECTIVE MATS ON THE COWL.
(1) Soak a piece of waterproof silicon carbide (Material No. V05-020) in Methyl Ethyl Ketone, Technical
grade (Material No. V01-076) and remove any remaining sealant or contamination.
(2) Use a clean piece of lint free cloth to dry the area before the cleaning fluid dries.
(3) Make sure there is no unwanted material on the repair area.
Subtask 71-11-11-380-051-A
C.
Prepare the aerodynamic sealant
WARNING: KEEP FLAMES AND ELECTRICAL EQUIPMENT WHICH IS NOT FLAMEPROOF AWAY
FROM THE WORK AREA. THE SEALANT IS FLAMMABLE.
(1) Use a pre-filled semkit cartridge and prepare sealant (Material No. V08-141) or
sealant (Material No. V08-146) as follows:
(a) Hold the cartridge and pull out approximately 25% of the dasher rod.
(b) Push the ramrod into the hollow end of the dasher rod and inject approximately 33% of the
contents into the cartridge.