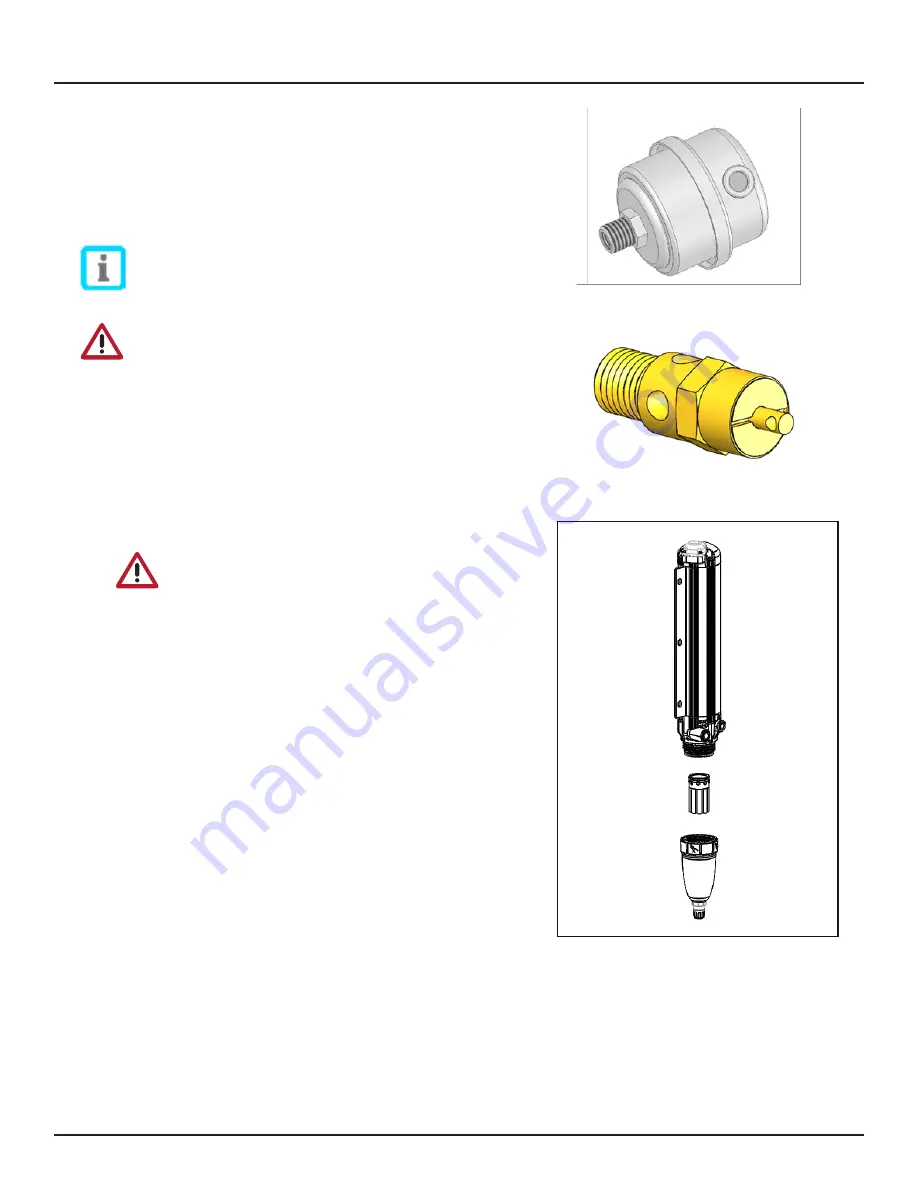
Page 17
Air Techniques, Inc.
Air Techniques, Inc.
Page 16
Maintenance
4.2.2
Changing suction filters
The suction filter (example Figure 3)
needs to be changed only once a year,
if the surrounding conditions are clean.
If the atmosphere is excessively dusty the
suction filter must be changed more often.
Dirty filters decrease the delivery output and
the lifespan of your product!
Warning!
Prior to changing filters, switch
product off by placing the Main power /
pressure switch to “O” - “OFF” position.
To change the air filter, proceed as follows:
1. Turn the filter housing (1) clockwise. The
bayonet lock opens and the filter can
be pulled off.
2. Exchange the air filter insert.
3. Turn the filter housing counterclockwise
until the bayonet lock is closed again
Attention!
Never clean filter inserts
with petrol or oil
4.2.3
Check safety valve function
The safety valve (see Figure 4) is set in the
factory at the tank pressure, tested and lead
sealed according to the current regulations.
Under no circumstance should the seal be
removed or the safety valve be reset. Any
tampering of the seal will invalidate all liability.
The safety valve is to be function tested
semi-annually. With working pressure in the
tank, turn the valve lifter (1) counterclockwise
until blown off compressed air is heard. Turn
the valve filter again in a clockwise direction
until it is closed.
Figure 3.
Inlet Filter
Figure 4.
Safety Valve 1 Knob
Figure 5.
Replace Sintered Filter