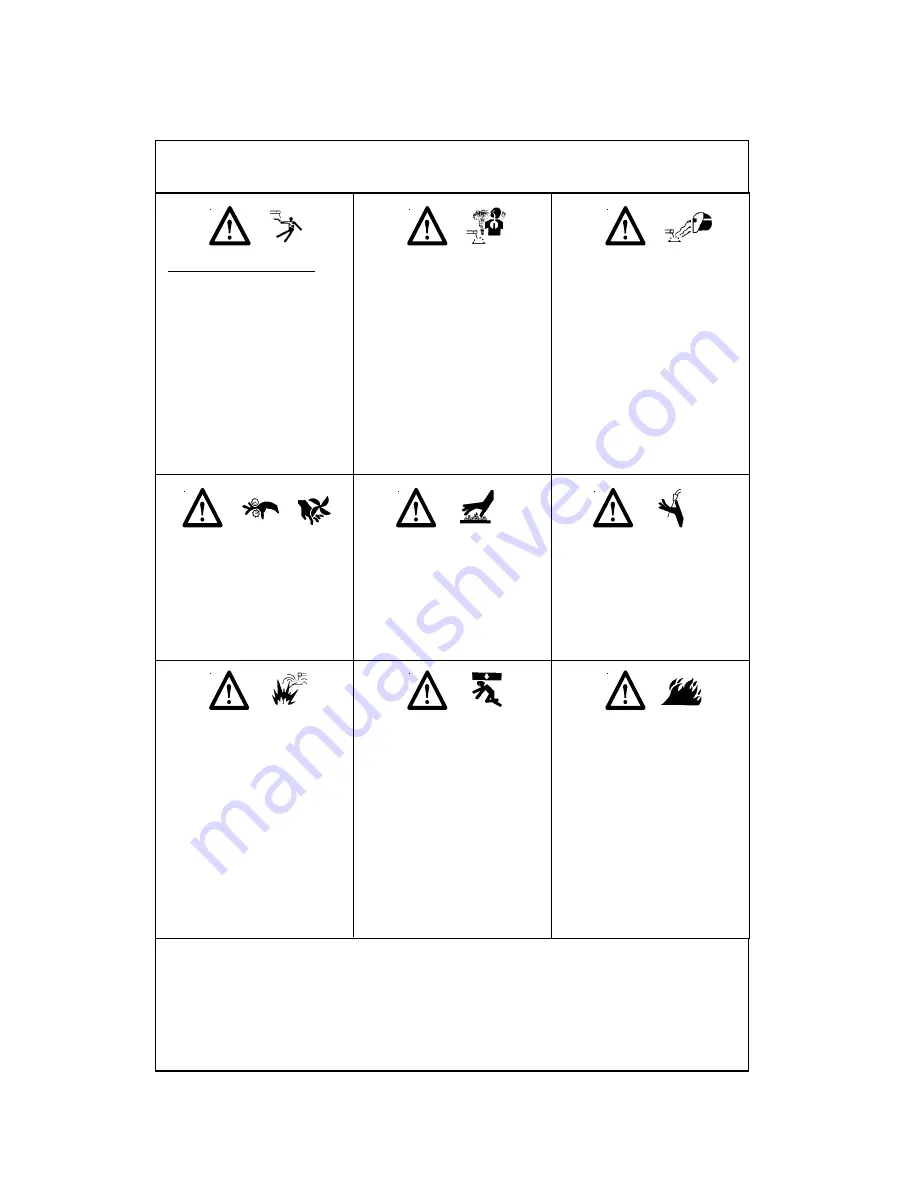
6
EQUIPMENT INSTALLATION AND MAINTENANCE MUST BE PERFORMED IN COMPLIANCE
WITH LOCAL SAFETY STANDARDS.
• INSTALLATION AND MAINTENANCE OPERATIONS MUST BE PERFORMED BY QUALIFIED PERSONS ONLY.
• BEFORE INSTALLING the power source, check that the power socket satisfies ampere and voltage require-
ments (see data table plate). ENSURE that the socket is protected by appropriate fuses and automatic
switches.
• CONNECT an approved standard plug corresponding to the system socket to the power supply cable.
Electric shock could be fatal
1. Never touch exposed electrical
parts.
2. Switch off and disconnect the
power source before installing
or opening.
3. Installation may be performed
by qualified persons only.
4. Installation procedure must
comply with national electricity
standards and all other relevant
regulations.
Fumes and gases may represent
a safety hazard.
Fumes and gases generated dur-
ing welding may be dangerous if
inhaled over a long period of
time.
1. Keep clear of fumes.
2. Ventilate welding area or wear a
breathing mask.
3. Install a natural or forced air
ventilation system in the work
area.
Use a protective mask with suit-
able glass filter (at least NR10) to
safeguard eyes.
1. Wear appropriate eye, ear and
body protection equipment.
2. Protect face, ears and neck dur-
ing welding operations. Advise
other persons in the vicinity to
look away and stand clear of arc
rays and hot metal.
The positioning of welding equip-
ment on inflammable surfaces
could lead to fire outbreak or
explosion.
1. Never position equipment on
combustible or inflammable
surfaces.
2. Do not install equipment in the
vicinity of inflammable liquids.
A falling power source or other
equipment may cause serious
injury to persons or damage to
objects.
1. Always make use of the handle
to lift power source (applies to
portable models).
2. Use eye bolts and adequate lift-
ing equipment to raise the
power source.
WELDING MAY CAUSE FIRES OR
EXPLOSIONS. Never weld near
inflammable materials.
1. Beware of weld flame. Always
keep a fire extinguisher close at
hand.
2. Never place welding equipment
on inflammable surfaces.
3. Do not weld in closed containers.
4. Let welding equipment and
material cool before handling
them.
Moving parts may cause injury.
1. Keep clear of hazardous areas,
such as moving rollers.
2. Keep all doors, panels and
covers closed and in place.
Hot areas may cause injury.
Let the power source or other
parts cool before performing
any maintenance or servicing.
Welding wire may cause injury.
Do not point the torch toward
any part of the body, other per-
sons or any type of metal when
unwinding welding wire.
Summary of Contents for T 150i AC/DC
Page 14: ...14 6 T 150i AC DC ELECTRICAL DIAGRAM...
Page 15: ...15 7 T 150i AC DC SPARE PARTS LIST...
Page 16: ...16...