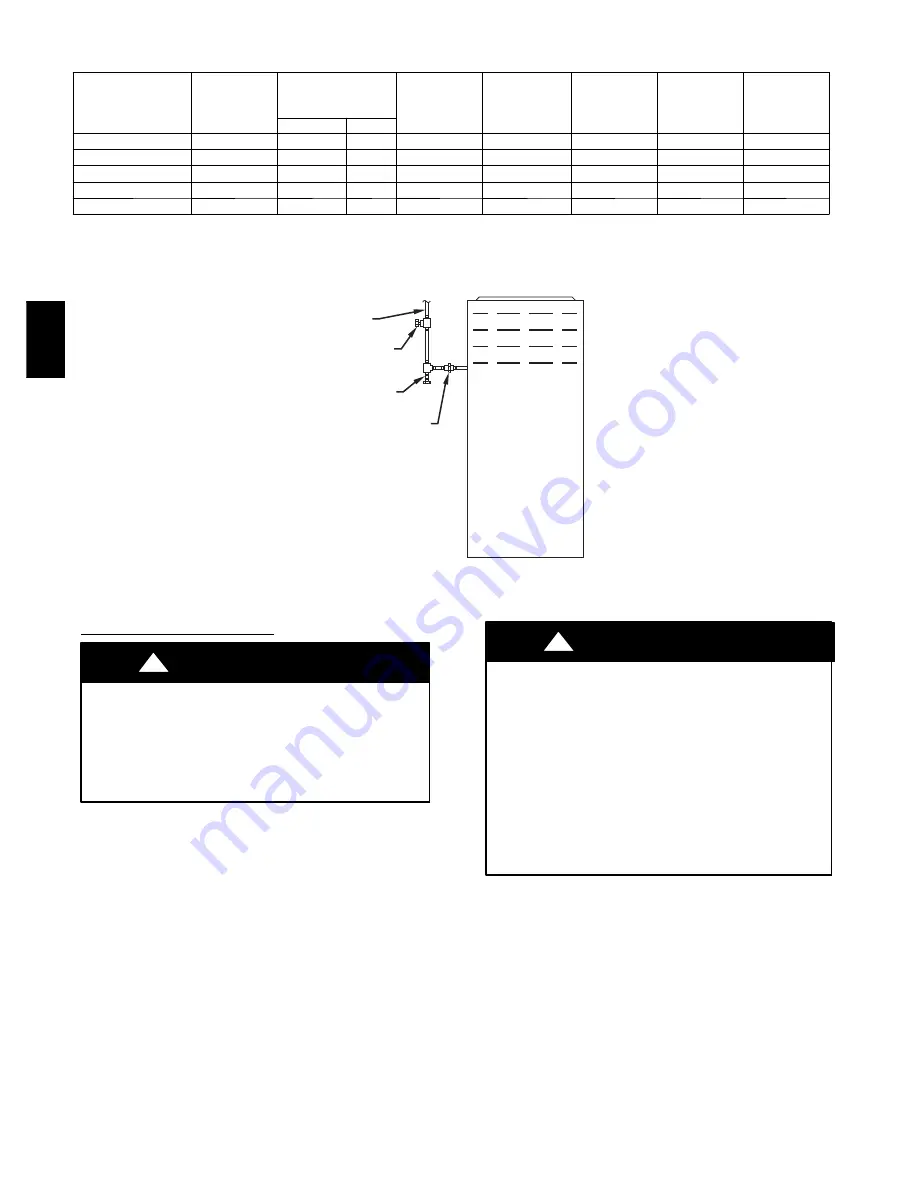
20
Table 7 – Electrical Data
FURNACE
MODEL
VOLTS---
HERTZ---
PHASE
OPERATING
VOLTAGE*
(VOLTS)
MAX UNIT
(AMPS)
UNIT
AMPACITY#
(AMPS)
MAX WIRE
LENGTH
}
FT. (M)
MAX FUSE/
CKT BKR
{
(AMPS)
MIN WIRE
GAGE
MAX
MIN
045---08 / 024045
115---60---1
127
104
8.1
10.9
34 (10)
15
14
070---16 / 048070
115---60---1
127
104
9.5
12.6
29 (9)
15
14
090---16 / 048090
115---60---1
127
104
10.3
13.4
27 (8)
15
14
110---20 / 060110
115---60---1
127
104
13.1
16.9
34 (10)
20
12
135---20 / 060135
115---60---1
127
104
13.1
16.9
34 (10)
20
12
* Permissible limits of the voltage range at which the unit operates satisfactorily.
# Unit ampacity = 125 percent of largest operating component’s full load amps plus 100 percent of all other potential operating components’ (EAC, humidifier,
etc.) full load amps.
{
Time---delay type is recommended.
}
Length shown is as measured 1 way along wire path between unit and service panel for maximum 2 percent voltage drop.
UNION
SEDIMENT
TRAP
MANUAL
SHUTOFF
VALVE
(REQUIRED)
GAS
SUPPLY
A02035
Fig. 22 -- Typical Gas Pipe Arrangement
ELECTRICAL CONNECTIONS
ELECTRICAL SHOCK HAZARD
Failure to follow this warning could result in personal
injury or death
.
Blower access panel door switch opens 115--v power to
control. No component operation can occur. Do not bypass
or close switch with panel removed.
!
WARNING
See Fig. 25 for field wiring diagram showing typical field 115--v
wiring. Check all factory and field electrical connections for
tightness.
Field--supplied wiring shall conform with the limitations of 63
_
F
(35
_
C) rise.
ELECTRICAL SHOCK AND FIRE HAZARD
Failure to follow this warning could result in personal
injury, death, or property damage.
The cabinet MUST have an uninterrupted or unbroken
ground according to NEC ANSI/NFPA 70--2008 or local
codes to minimize personal injury if an electrical fault
should occur. This may consist of electrical wire, conduit
approved for electrical ground or a listed, grounded power
cord (where permitted by local code) when installed in
accordance with existing electrical codes. Refer to the
power cord manufacturer’s ratings for proper wire gauge.
Do not use gas piping as an electrical ground.
!
WARNING
PG
8M
EA
Summary of Contents for PG8JEA
Page 4: ...4 A10269 Fig 2 Clearances to Combustibles PG8MEA ...
Page 28: ...28 A10133 Fig 33 Chimney Inspection Chart PG8MEA ...
Page 38: ...38 Table 13 Orifice Size and Manifold Pressure In W C for Gas Input Rate A10180 PG8MEA ...
Page 39: ...39 Table 13 Orifice Size and Manifold Pressure In W C for Gas Input Rate CONT A10180A PG8MEA ...
Page 40: ...40 Table 14 Orifice Size And Manifold Pressure In W C For Gas Input Rate A10181 PG8MEA ...
Page 41: ...41 Table 14 Orifice Size And Manifold Pressure In W C For Gas Input Rate CONT A10181A PG8MEA ...