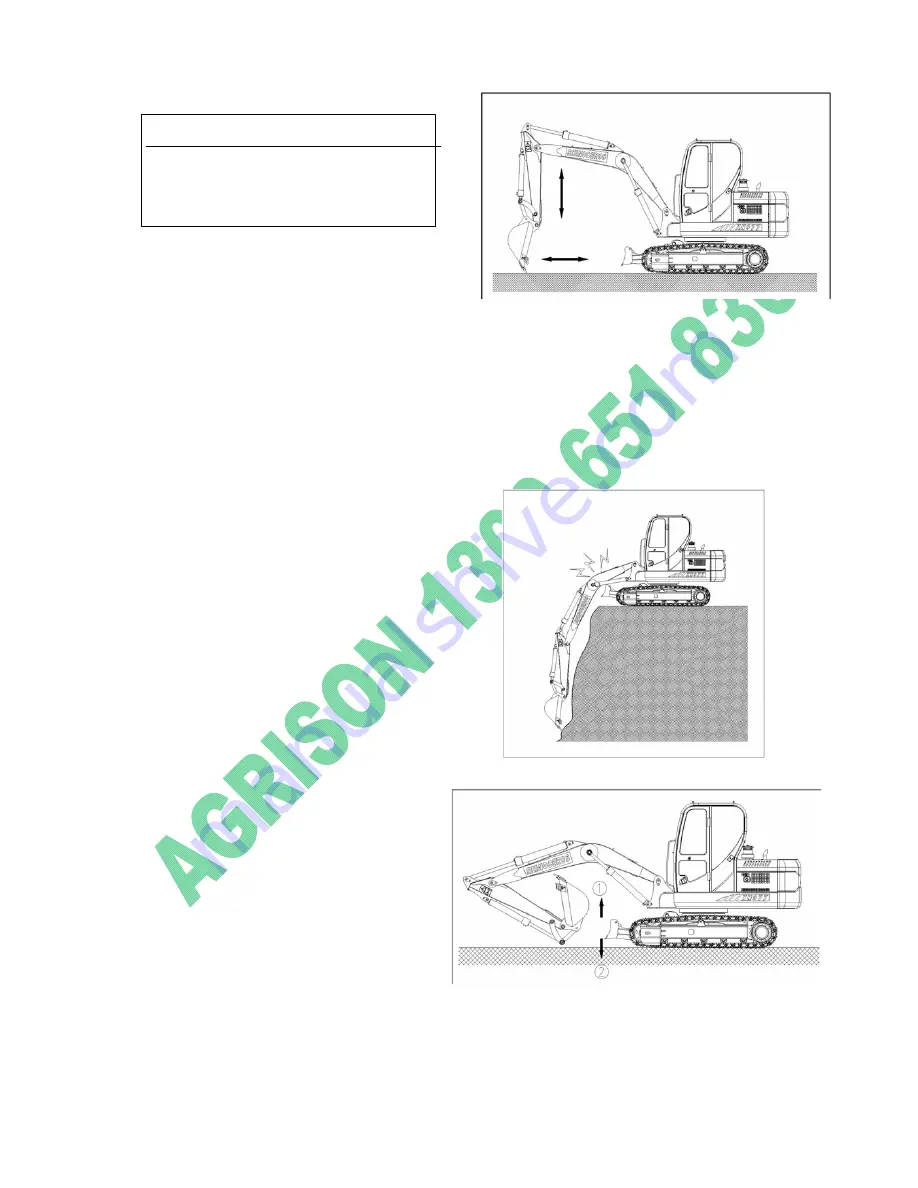
56
IMPORTANT
Do not overuse the bucket to lev
ground; otherwise some parts wi
el
ll
Level ground
break due to overload working.
1 . Using the dozer plate to level
ground.
2. Using the boom, bucket arm and
bucket.
A. When level the ground from front to back, raise the boom, at the same
time slowly move the bucket arm, when the bucket arm is near the machine,
stably lower the boom to let the bucket move horizontally.
B.Do in the reverse order when level ground from back to front.
Pay attention to the position
of dozer plate
1.The dozer plate may touch the boom
cylinder and the bucket when it is
forward, be careful.
2.Keep the dozer plate backward when
digs deeply.
1
.
the dozer plate is to bulldoze, not for
digging, otherwise it will hurt the
dozer plate and the hydraulics.
2.The dozer plate can not stand
heavy thing
3.Do not let the dozer plate hookup
any thing when walks.
4.Be sure the ground is even and
solid when using it to support
the excavator.
Fig 3-60
https://tractormanualz.com