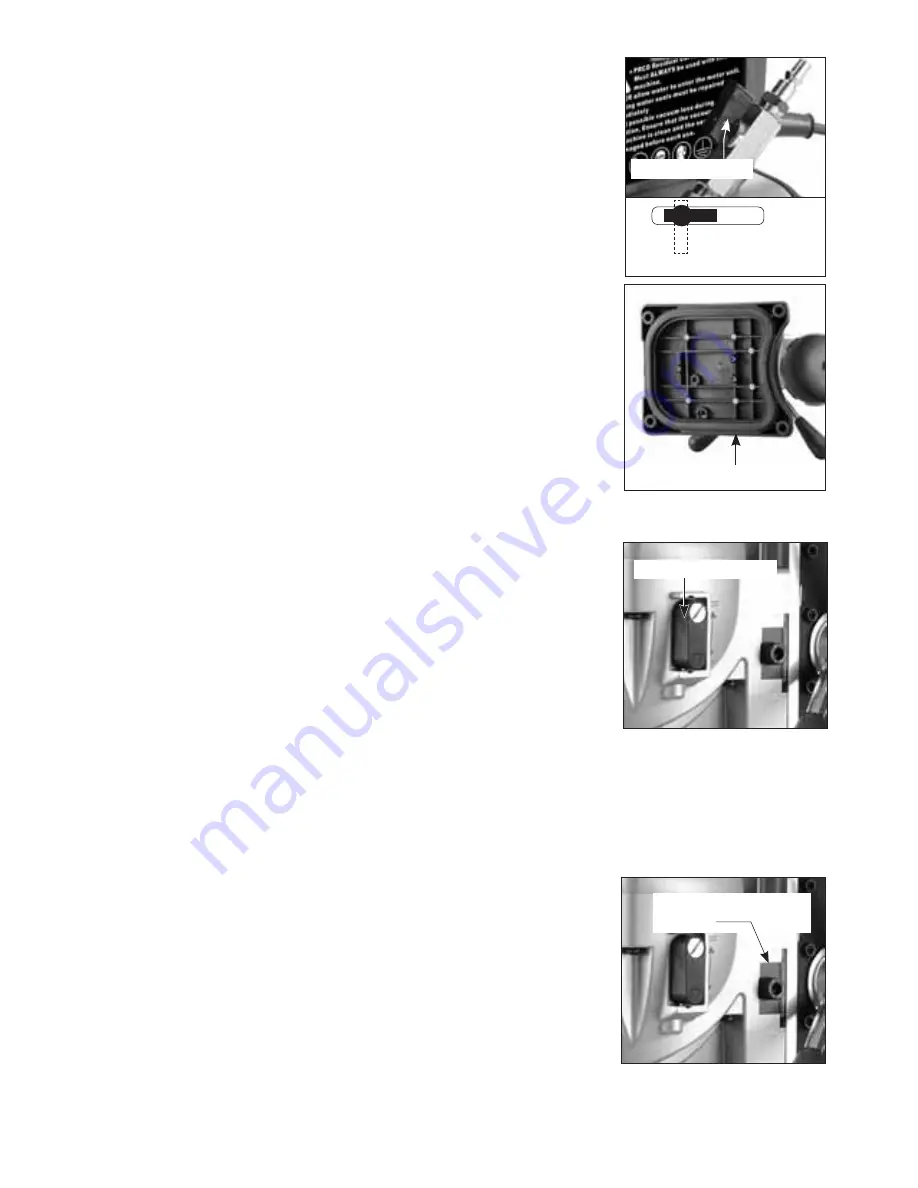
8
3. Vacuum Pump
This machine must be used in conjunction with a vacuum pump.
Connect the vacuum hose quick-release coupling to the vacuum
valve fitting on the vacuum base of the machine.
WARNING: Never attempt to use this machine without a vacuum
pump or if the vacuum base is damaged. Ensure that the vacuum
base of the machine is clean and the seal is undamaged before
each use. Never attempt to clamp the machine in any way other
than that which it was designed. This could cause a hazard.
WARNING: Never attempt to drill unless there is a minimum of 10 psi
(0.7bar) of vacuum.
4. Selecting Speeds
There are 2 speed ranges to suit the bit size and work piece
hardness. Choose the slowest speed for large diameter bits and
hard materials.
CAUTION: Never attempt to change gears on a running
machine! Only adjust when the machine is at rest.
Select the desired gear range by first swinging the gear selector
tab out of the detent slot then shifting up or down into the desired
gear. Then pop the selector tab back into the detent. It will usually
be necessary to turn the spindle by hand a little to get it to shift all
the way.
5. Motor Head Height Adjustment (See page 2 )
The height of the motor head on the slide is adjustable on this
machine to suit different sizes of diamond core bit. It is always
wise to keep the slide as low as possible in the guidance gibs yet
still have enough stroke to finish the cut. This will make the drilling
operation more stable. A good starting point would be start with
the slide at the bottom of its stroke. Then raise the slide slightly
more than the amount of the desired depth of cut. Then loosen
the motor head height adjustor (after you loosen it, give it a tap
to unlock the motor head). Now raise the motor head just high
enough on the slide so that the diamond core bit can fit with some
clearance.
Gear Selector Tab
Motor Head Height
Adjustor
Vacuum Base Seal
Vacuum Valve
Open
Closed
Summary of Contents for TC100
Page 13: ...13 WIRING MOTOR MAGNET SWITCH AC CARBON BRUSH CARBON BRUSH ...
Page 16: ......