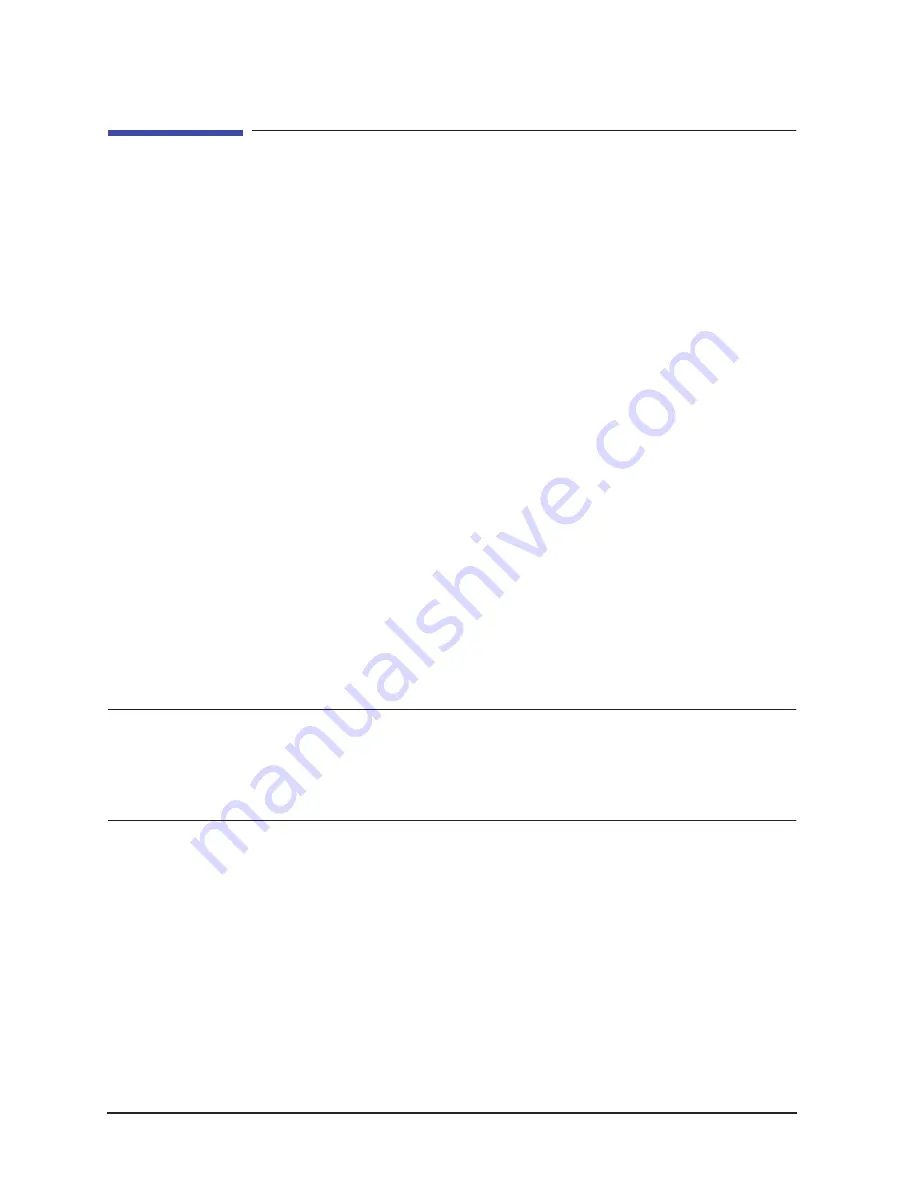
3- 6
85051B
Use, Maintenance, and Care of the Devices
Gaging Connectors
Gaging Connectors
The gages available from Agilent Technologies are intended for preventive maintenance and troubleshooting
purposes only. They are effective in detecting excessive center conductor protrusion or recession, and
conductor damage on DUTs, test accessories, and the calibration kit devices.
Do not use the gages for
precise pin depth measurements.
Connector Gage Accuracy
The connector gages are only capable of performing coarse measurements. They do not provide the degree
of accuracy necessary to precisely measure the pin depth of the kit devices. This is partially due to the
repeatability uncertainties that are associated with the measurement. Only the factory—through special
gaging processes and electrical testing— can accurately verify the mechanical characteristics of the
devices.
With proper technique, the gages are useful in detecting gross pin depth errors on device connectors. To
achieve maximum accuracy, random errors must be reduced by taking the average of at least three
measurements having different gage orientations on the connector. Even then, the resultant average can be
in error by as much as ±0.0001 inch due to systematic (biasing) errors usually resulting from worn gages and
gage masters. As the gages undergo more use, the systematic errors can become more significant in the
accuracy of the measurement.
When to Gage Connectors
Gage a connector at the following times:
•
Prior to using a device for the first time: record the pin depth measurement so that it can be compared
with future readings. This serves as a good troubleshooting tool when you suspect damage may have
occurred to the device.
NOTE
When measuring pin depth, the measured value (resultant average of three or more
measurements) contains measurement uncertainty and is not necessarily the true value.
Always compare the measured value with the
observed
pin depth limits (which account for
measurement uncertainties) in
and with previously recorded values to
evaluate the condition of device connectors.
•
If either visual inspection or electrical performance suggests that the connector interface may be out of
typical range (due to wear or damage, for example).
•
If a verification device is used by someone else or on another system or piece of equipment.
•
Initially after every 100 connections, and after that as often as experience indicates.
Summary of Contents for 85051B
Page 4: ...iv 85051B ...
Page 7: ...85051B 1 1 1 General Information ...
Page 12: ...1 6 85051B General Information Clarifying the Terminology of a Connector Interface ...
Page 13: ...85051B 2 1 2 Specifications ...
Page 19: ...85051B 3 1 3 Use Maintenance and Care of the Devices ...
Page 37: ...85051B 4 1 4 Performance Verification ...
Page 40: ...4 4 85051B Performance Verification Recertification ...
Page 41: ...85051B 5 1 5 Troubleshooting ...
Page 43: ...85051B 5 3 Troubleshooting Troubleshooting Process Figure 5 1 Troubleshooting Flowchart ...
Page 46: ...5 6 85051B Troubleshooting Contacting Agilent ...
Page 47: ...85051B 6 1 6 Replaceable Parts ...
Page 50: ...6 4 85051B Replaceable Parts Introduction Figure 6 1 Replaceable Parts ...