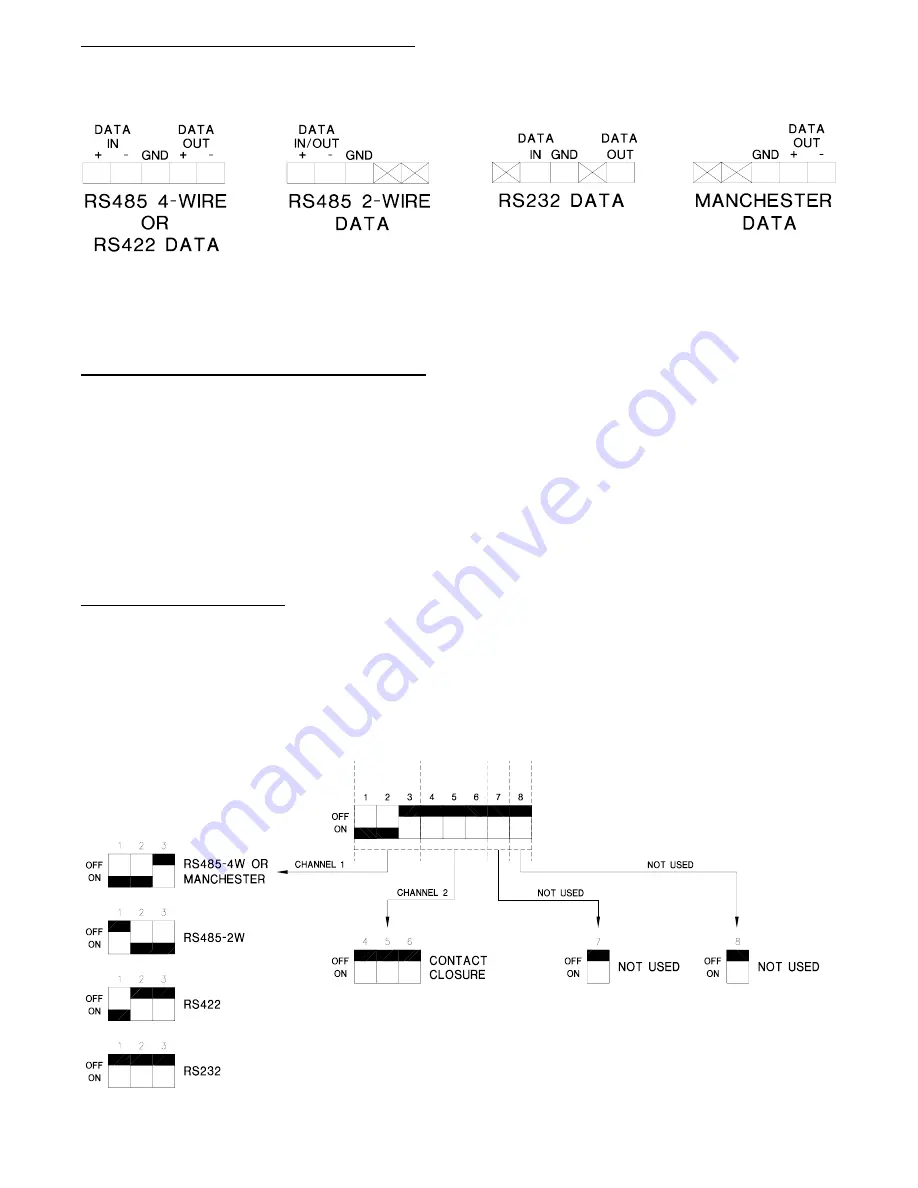
4
DATA INPUT / OUTPUT CONNECTIONS
Data input and output connections are made via terminal blocks on the right side of the unit. See the
drawings below for proper orientation of the input and output connections for Data Channel 1. Please
note that the far right pin on each connection drawing corresponds with the terminal block pin located
closest to the base of the unit.
Follow the label on the unit for proper orientation of the input and output contact closure connections for
Data Channel 2. The GND and IN terminals of CONTACT DATA CH 2 should be connected to the
contact closure input signal. Creating continuity between these two terminals will activate (close) the
two terminals labeled OUT on the corresponding MR-915D or RR-915D.
TYPICAL SYSTEM DATA CONNECTIONS
The RS422 or RS485 four wire interconnection between the MT-915D and the copper device to which it
is attached is based on industry standard EIA terminology for the transmission of electronic data
signals. Using this terminology, the driver of an electronic signal is labeled TX or Data Out.
Correspondingly, the receiver of an electronic signal is labeled RX or Data In. Following this standard,
the Data Out of the copper device is connected to the Data In of the MT-915D. The plus terminal of the
copper device is connected to the plus terminal of the MT-915D and the minus is connected to the
minus. The reverse flow of data from the MT-915D to the copper device follows the same pattern. Not
all manufactures follow standard EIA terminology. Consult the installation instructions for your copper
device if you are unsure which two wires are the drive (data out) wires and which two wires are the
receive (data in) wires.
DATA CONFIGURATION
NOTE: This unit is shipped in the following default configuration.
Channel 1: RS485 (4 wire) data
Channel 2: Contact Closure (dry)
For other configurations of Channel 1, please refer to the drawing below for changes to the default
switch settings. These configuration switches are located on the left side of the unit and can be
modified without opening the unit. Please note that switches # 4 through switch # 8 must remain in the
up position.