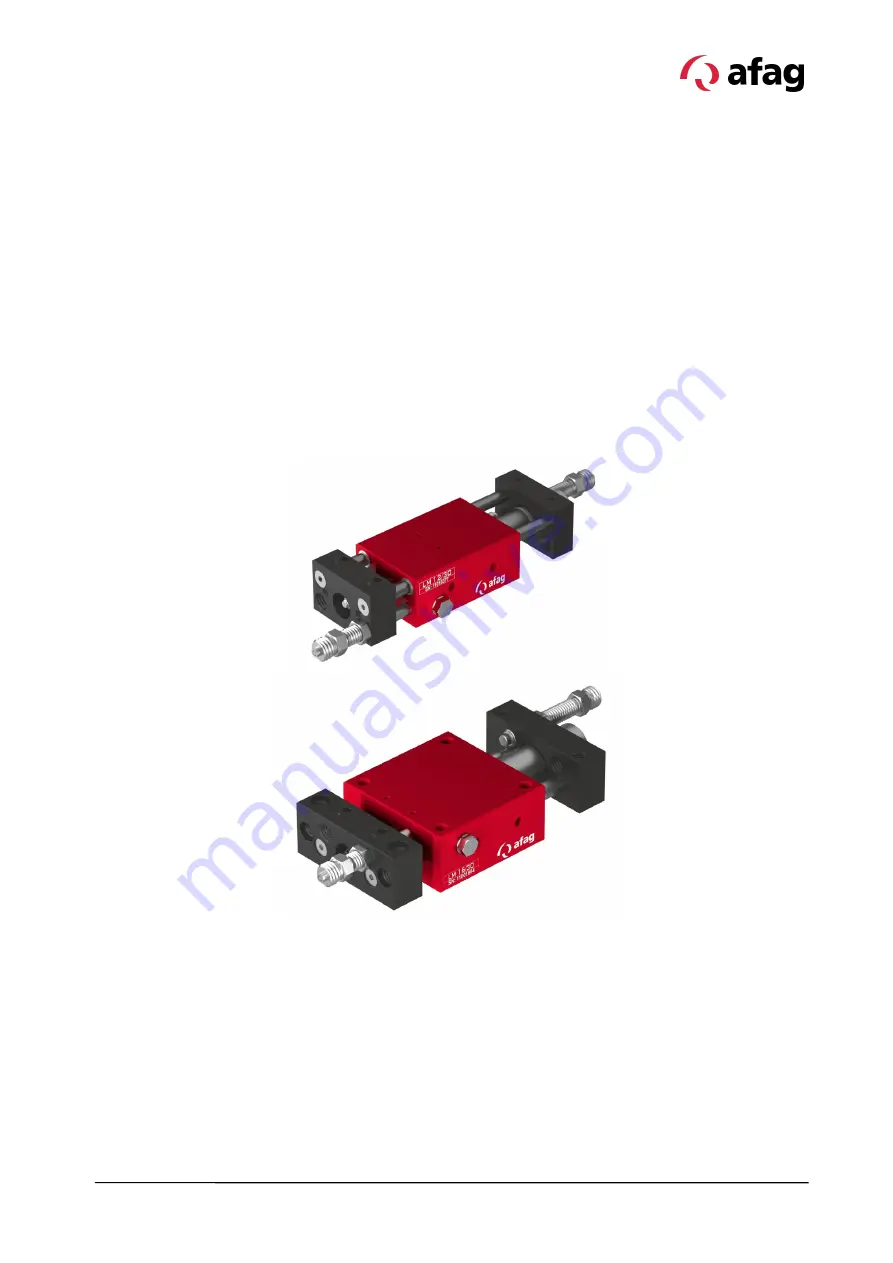
Assembly Instructions EN
LM 12 I LM 16
Edition 11/2020
Rev. 2.5
1–52
Assembly and operating instructions
Linear Modules
LM 12
I
LM 16
Translation of the Original Assembly Instructions EN
LM 12/30
Order No.: 11010377
LM 12/60
Order No.: 11010378
LM 12/90
Order No.: 11010379
LM 16/30
Order No.: 11001864
LM 16/60
Order No.: 11001865
LM 16/90
Order No.: 11001866