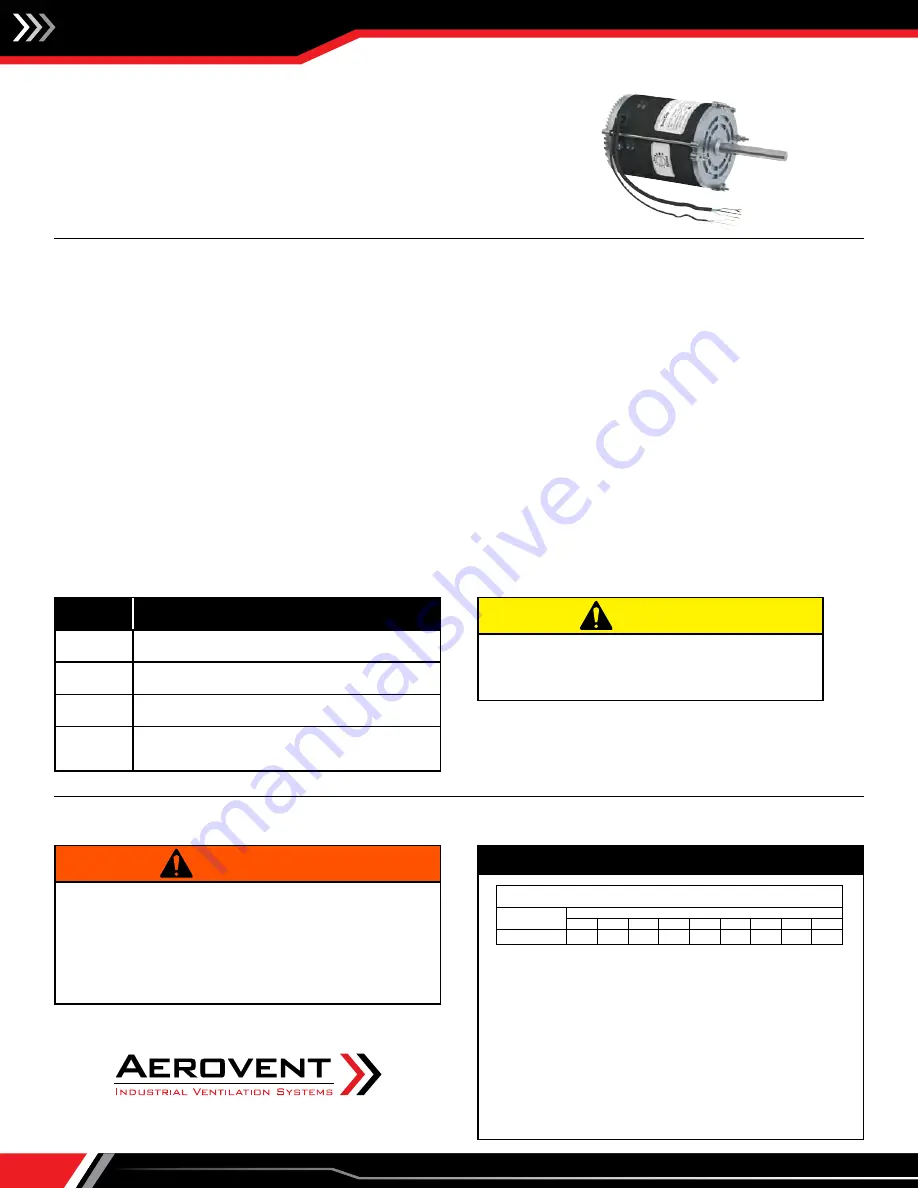
Installation, Operation & Maintenance Manual
IM-502
10
*Suggested lubrication interval under continuous operation in adverse loading or with
elevated temperatures. For operation less than 24 hours per day or under ideal conditions,
lubrication frequency may be reduced. Relubricate while running, if safety permits, until
some purging occurs at seals. Adjust lubrication frequency depending on condition of
purged grease. Hours of operation, temperature and surrounding conditions will affect the
relubrication frequency required.
1. Lubricate with a high quality NLGI No. 2 lithium-base grease having rust inhibitors and
antioxidant additives, and a minimum oil viscosity of 500 SUS at 100°F (38°C). Some
greases having these properties are:
Shell - Gadus S2 V100 2
Mobil - Ronex MP
Mobil - Mobilith SHC100
Mobil - Mobilith SHC220
2. Lubricate bearings prior to extended shutdown or storage and rotate shaft monthly to aid
corrosion protection.
Fans with Ball Bearings
Relubrication Schedule (Weeks)*
Ball Bearing Pillow Blocks
Shaft DIA
Speed (RPM)
500
1000 1500 2000 2500 3000 3500 4000 4500
3
⁄
4
" (19 mm)
6
6
5
3
3
2
2
2
1
1. This equipment must not be operated without proper guarding
of all moving parts. While performing maintenance be sure
remote power switches are locked off. See installation manual
for recommended safety practices.
2. Before starting: Check all set screws for tightness and rotate
impeller by hand to make sure it has not moved in transit.
WARNING
Safety & Bearing Lubrication Instructions
Fan Bearing Maintenance
(refer to safety section)
Proper lubrication of the fan drive bearings helps assure maximum bearing life. All fans are equipped with decals indicating the
recommended relubrication intervals for normal operating conditions.
The standard pillow block bearings on belt driven ventilators are factory lubricated and are provided with external grease fittings.
Annual lubrication is recommended, or more frequently if needed (see
Greasing Intervals
table). It is recommended to add fresh grease
at start-up, but do not over-grease. Use only 1 or 2 shots of a recommended lubricant with a hand gun in most cases. Maximum hand
gun rating 40 P.S.I. Rotate bearings during lubrication where good safety practice permits. The most frequent causes of bearing failure
are not greasing often enough, using an excessive quantity of grease or using incompatible greases. Excessive vibration, especially if
the bearing is not rotating, will also cause bearings to fail. Bearings must also be protected from water and moisture to avoid internal
corrosion.
During the first few months of operation it is recommended that the bearing set screws be checked periodically to ensure that they are
tight. The rotating impeller requires particular attention since materials in the air being handled can build up on the blades to cause
destructive vibration or weaken the structure of the impeller by corroding and/or eroding the blade metal. Regular inspection and
corrective action at intervals determined by the severity of each application are essential to good service life and safety.
Suggested Fan Bearing Greasing Intervals
INTERVAL
(MONTHS)
TYPE OF SERVICE
12 to 18
Infrequent operation or light duty in clean atmosphere
6 to 12
8 to 16 hrs./day in clean, relatively dry atmosphere
3 to 6
12 to 24 hrs./day, heavy-duty or if moisture is present
1 to 3
Heavy-duty in dirty, dusty locations; high ambient
temperatures; moisture-laden atmosphere; vibration
Greases of different soap bases (lithium, sodium, etc.) may
not be compatible when mixed. Prevent such intermixing
by completely purging the bearing of old greases.
CAUTION
EC Motor Information
See IM-4055 for EC motor details.