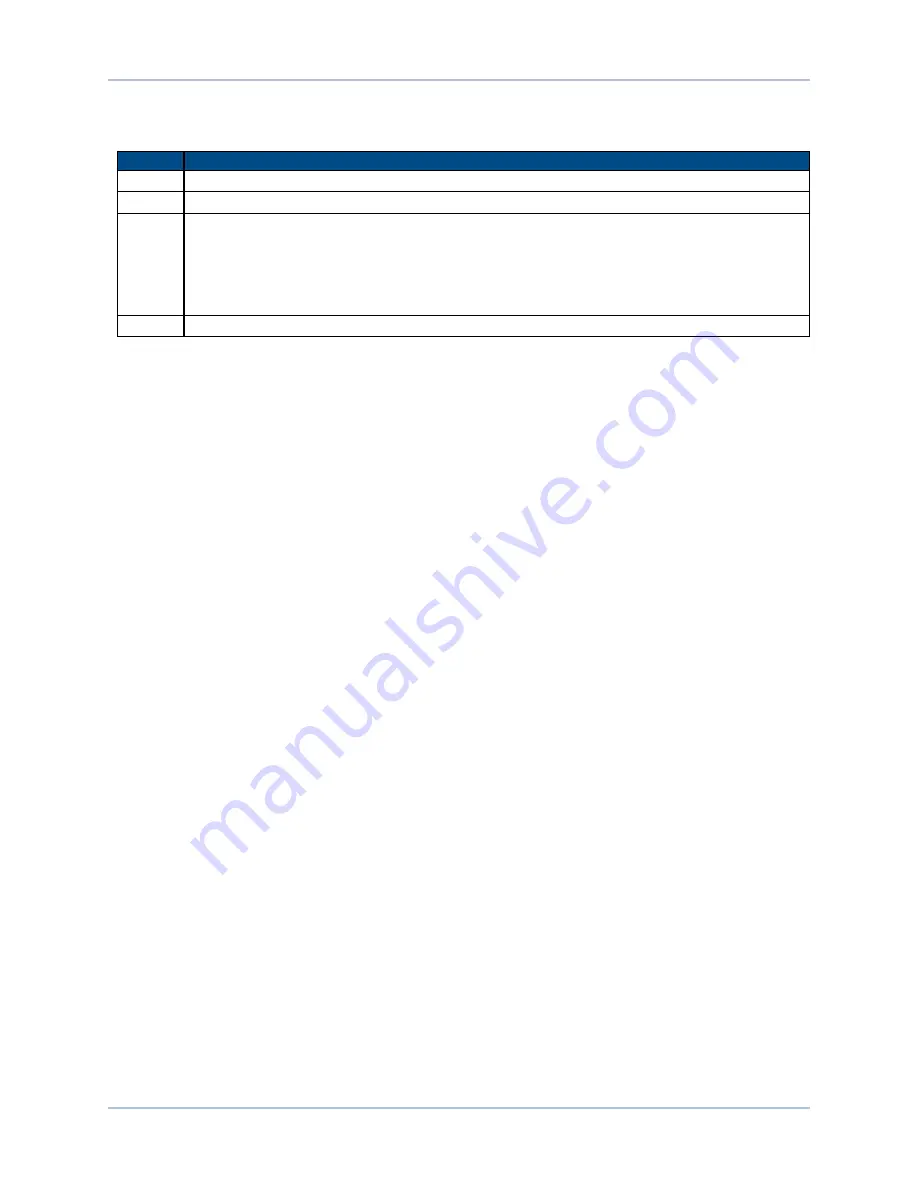
ARMS Hardware Manual
Revision History
Appendix B: Revision History
Revision
General Information
1.03.00
Complete manual revision
1.02.00
Changed motor feedback pin 8 to reserved
1.01.00
l
Declaration of Incorporation added
l
Environmental Specifications added
l
Safety information and warnings added/updated
l
Motor Specifications added
l
Note about wire current and voltage requirements added
1.00.00
New manual
www.aerotech.com
Appendix B
45