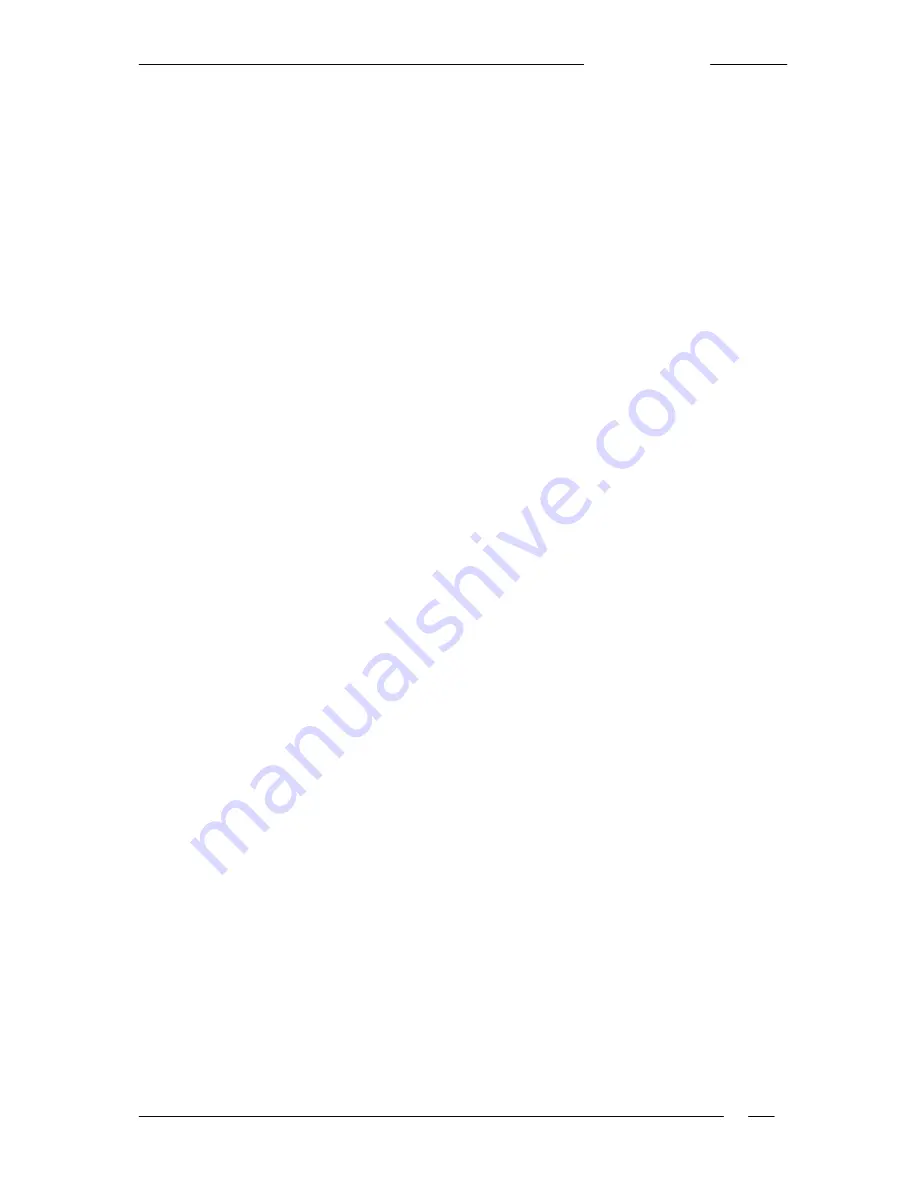
Pober Pixie
Pober Pixie building instructions
4
Wheel spats
The wheel spats are supplied as vacuum-moulded ABS parts; see drawing (DET. 5).
•
Cut out the spat components along the marked lines, sand the cut edges carefully and trim the
parts to fit together accurately - you will find the material is easy to cut and sand.
•
Cut out the opening for the wheel in each wheel spat and check that the wheel spigots fit.
•
Assemble the wheels and spigots as shown in the drawing (DET. 5), place them in the spats and
glue the trimmed outer spat shell in place with cyano.
•
The method of attaching the wheel spats is shown in the drawing (DET. 5).
•
The spat assemblies can easily be fitted and screwed to the undercarriage unit after they have
been filled and painted.
Tailwheel unit
•
Sand the tailwheel support #4 (channeled part) to follow the shape of the fuselage as shown in the
drawing, and glue it in place.
•
Cut through the fuselage using a razor blade to expose the channel, and fit the tailwheel unit in the
slot.
•
Drill two 2 mm Ø holes at the marked points in the tailwheel unit to accept the 2.5 x 12 mm
woodscrews.
•
The tailwheel unit can be glued and screwed in place permanently once the final finish has been
applied.
•
We recommend that you install a steerable tailwheel as shown in the drawing (DET. 1): make up
the guide (wire loop) and install it in the rudder after it has been covered.
•
Cut the steerable tailwheel “snake” to length and run it through the prepared guide (loop).
Tailplane and fin
Horizontal stabiliser - tailplane and elevators
The tailplane is made of balsa and can now be prepared for installation. The same applies to the
elevators, which are attached using film hinges.
•
Assemble the tailplane and elevators on a flat surface and place the joiner in position.
•
Drill holes for the elevator joiner in the elevators, taking care to space the holes to match the exact
length of the joiner - see drawing (DET. 2).
•
Sand the tailplane / elevator panels lightly overall, wipe off all dust and cover them with iron-on
film.
•
If you wish to use the covering film as the elevator hinge (see DET. 3), this is the procedure:
o
Prepare a strip of film slightly longer than the tailplane and elevators.
o
Cover the top surface of the tailplane and elevators.
o
Lay the tailplane on the workbench and fold the elevators up and over onto the tailplane.
o
Iron the strip of film to the underside of the elevators (position the elevators carefully
beforehand - align them with the outside edge of the tailplane).
o
Cut off the film at the ends using a very sharp knife (use a steel straight edge).
o
Turn the tailplane and elevators over and cover the underside.
o
Again cut off the film accurately at the ends, leaving it overhanging by about 5 mm. Carefully
iron down the edges.
•
Carefully pierce the film at the joiner hole positions and glue the steel joiner in both elevators.
•
Alternative elevator control linkage: prepare two steel rods with a 90° bend (see DET. 4) and fit
them in the elevators with the angled rods located inside the fuselage. Solder the rods together
and attach a linkage ball to accept the elevator ball-link.
•
This option is rather tricky, and should only be attempted if you are a competent, accurate builder.
•
Place the tailplane on the fuselage and position it accurately, i.e. “square” to the fuselage centre-
line and lateral axis, as shown in the drawing.
Tip:
use a length of thread to check that it is square relative to the fuselage centreline - attach one
end to the centre of the cabane; the distance to both tailplane tips should be identical.
•
Use a soft pencil to draw a light mark on the underside of the tailplane where it meets the
fuselage. Remove the tailplane, slit the film with a sharp knife and peel it away about 5 mm from
the edge of the fuselage, so that the joint surface is bare wood; the film should overhang the joint
area by about 5 mm. This ensures a strong, resilient glued joint.