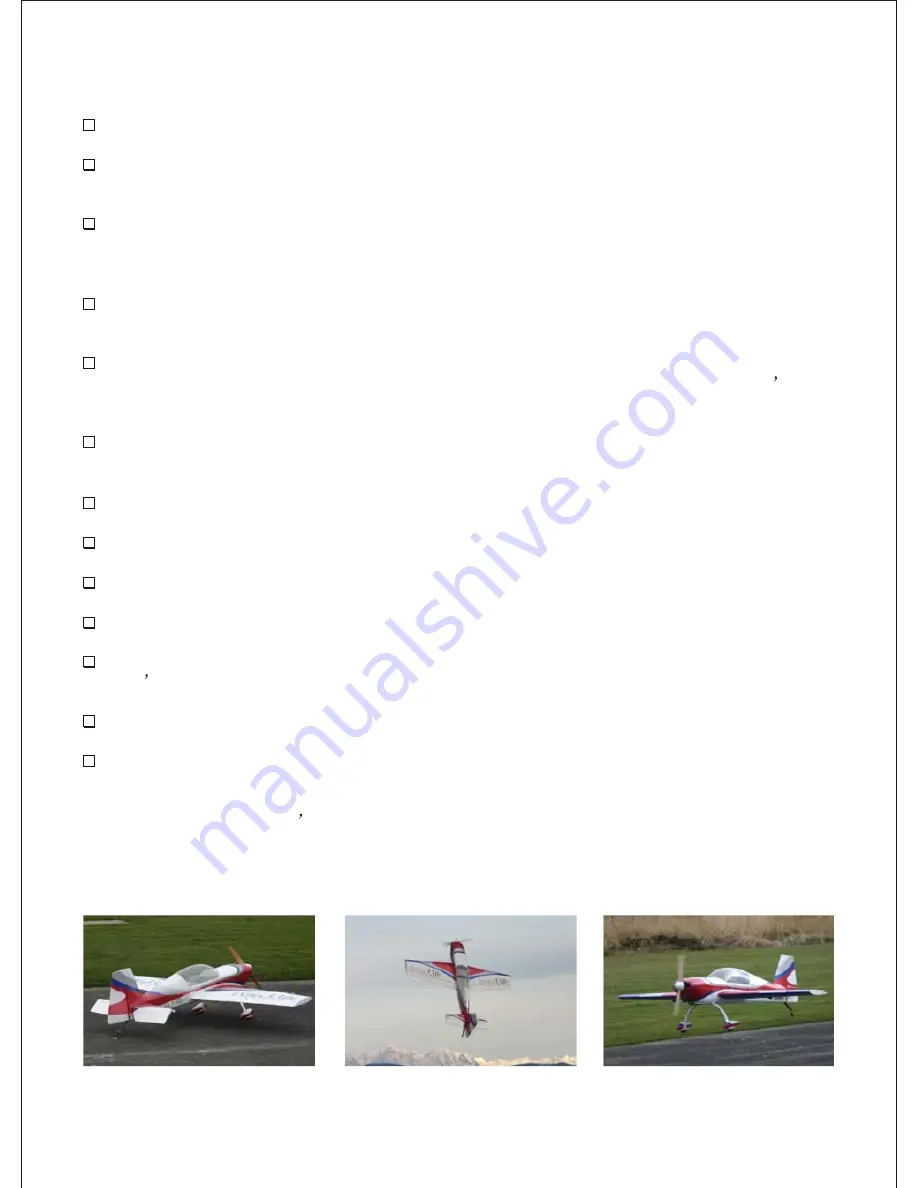
21
Lets go over the airframe and perform a pre-flight to make sure everything is in order.
This concludes your pre-flight checks. After your maiden flight, repeat these steps to perform a post flight to
ensure nothing has loosened. It s always a good habit to use a checklist like this one to go over your aircraft
prior to the first flight of the day.
Flying!
Inspect the airframe for any visible damage and loose covering that may have occurred during assembly.
Inspect the main landing gear and tail wheel assembly. Ensure all mounting hardware and collars are
fastened properly.
Inspect your motor installation and cowl to ensure all bolts are tight and the muffler is firmly mounted in
place. Check the motor and muffler for possible contact with the cowl. Inspect ignition module and
spark plug wire for proper mounting. Check propeller and spinner to ensure they are both secure.
Inspect the inside of the fuselage to ensure your batteries, switches, regulators (if equipped), fuel tank
and lines are securely fastened. Check nylon wing bolts to ensure they are in place and secured.
Inspect all control surfaces and control surface hardware. Gently tug on each surface to make sure the
hinges are properly bonded. Check the four 4/40 horizontal stabilizer fasteners and ensure they re in
place and secured.
Check all servos for mounting screws. Check servo arm mounting screws and inspect that the 4/40 links
have been secured with lock nuts.
Fill fuel tank and inspect for any leaks.
Check your batteries in both your aircraft and radio to ensure they are fully charged
Turn on radio to inspect all controls for binding, proper direction and throw while on high rates.
Re-check CG. It should be anywhere from 5 to 6 -1/2 inches depending on your flying style.
Secure aircraft using a buddy or hold down and start motor according to manufacturers guidelines.
Don t forget to lower your throttle prior to ignition.
Perform a proper range check with the motor running using your radio manufacturers instructions.
Make sure you go back to low rates for your maiden takeoff and enjoy!